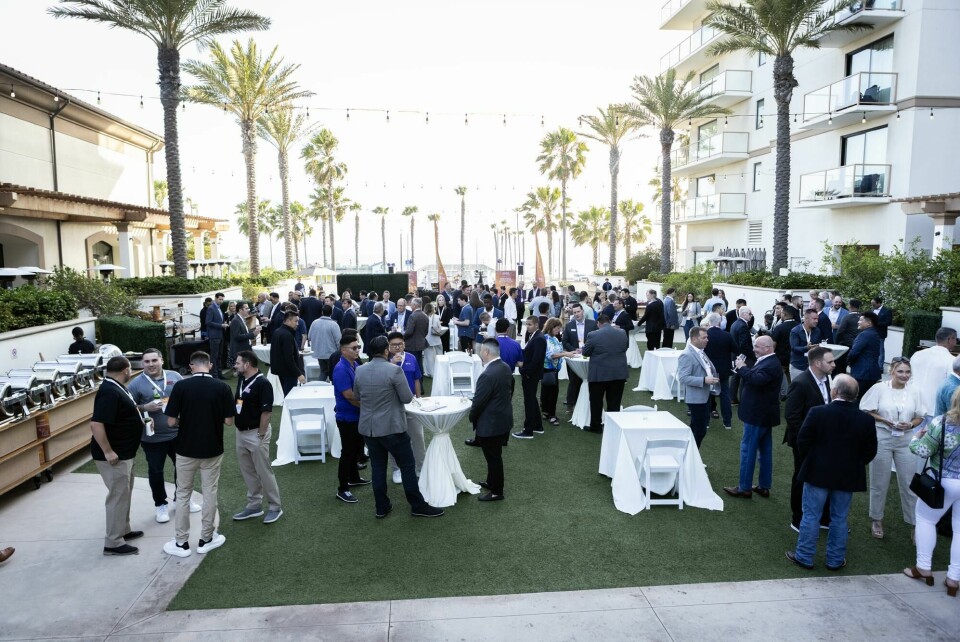
Finished Vehicle Logistics North America: Recap blog
Follow our recap blog below for key highlights and knowledge shared at Finished Vehicle Logistics North America 2024. We will be sharing news and videos straight from the main stage and the Red Sofa, including insight, data and quotes from the automotive experts who discussed how they are disrupting the status quo, and raising performance through innovation, flexibility and partnerships.
17th June
In the last Red Sofa intrerview, our chief content officer sat with Anu Goel, executive vice president of group after sales and services at Volkswagen Group, who discussed pivotal strategies Volkswagen has implemented to excel in vehicle logistics. Highlighting the shift towards a North American regional perspective, Goel emphasised how this change enhances connectivity and efficiency across borders. Watch the full video for an in-depth look at how Volkswagen is leading through innovation and collaboration in vehicle logistics.
4 June
In one of the four Ideas Labs held at this year’s Finished Vehicle Logistics North America conference in California, Ford’s team lead on vehicle business solutions, Alex McMall was joined by Nathan Lawson, vice-president of delivery and customer success at vehicle tracking and supply chain visibility provider FreightVerify.
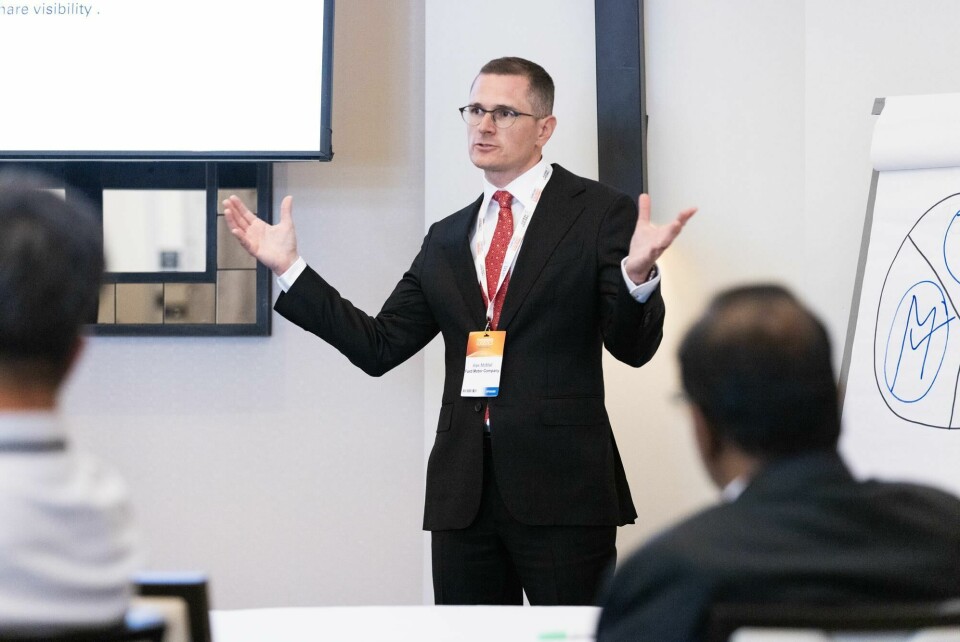
Ford has been working with FreightVerify for five years and vehicle telematics is at the core of the service.
“We’re at a very important inflection point in the industry,” said McMall. “I think when it comes to visibility, telematics is really the thing that has been the biggest differentiator.”
Communicating vehicle milestones and providing visibility at handover points through the vehicle delivery chain is at an all-time high and carmakers have different ways of aggregating the information, but according to McMall, telematics is really what is driving ETA calculations and final mile visibility.
Ford is working closely with FreightVerify to provide that visibility and the technology provider’s VinView tool provides vehicle status information to the dealerships.
“It’s enabled the dealer to really take things into their own hands and go grab the vehicles, which is really key,” said Lawson. “It’s been a huge customer satisfaction advantage, and also a win for the OEMs that have deployed it.”
However, it is also about striking a balance on the amount of information shared with the dealer, something manufacturers want to limit to avoid harassment if something delays a vehicle in transit.
3 June
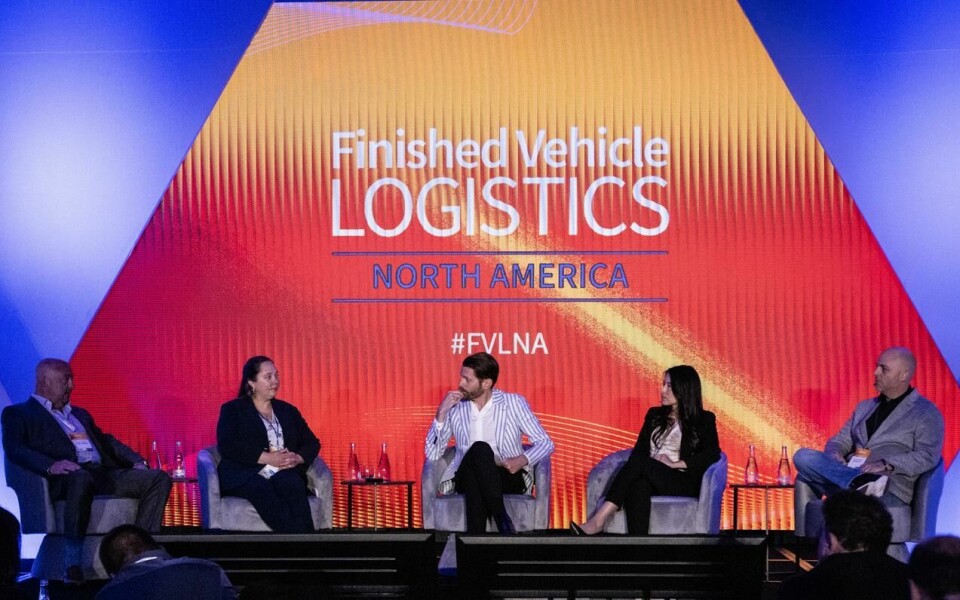
Jack Cooper’s Sarah Amico, Navistar International’s Shane Stierley, Glovis America’s Marisol Vasquez and Jeremy White from Autos in Motion explained what they were doing to improve services after a succession of disruptions over recent years in finished vehicle logistics. The region’s top performers believe disruption is fertile ground for innovation, and said they are taking further measures to be more flexible and resilient.
30 May
Christine Casey, deputy secretary for Freight Policy, California State Transportation Agency took to the Red Sofa to tell Christopher Ludwig, chief content officer, Automotive Logistics about the investments into California’s FVL sector.
Watch her talk about the creation of her role, and the need for a high-level position to coordinate and oversee the stakeholders in the FVL supply chain.
24 May
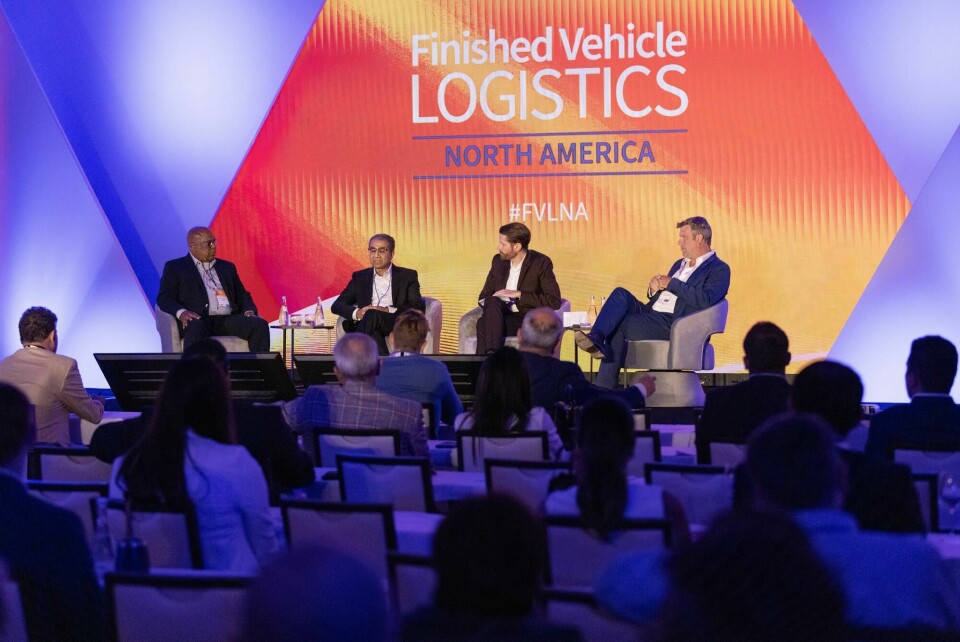
Carmakers and logistics providers are redefining partnerships to improve collective competitiveness and foster long-term success. But how is a win-win ensured for both sides?
Prashant Swadia, director of Global Logistics Purchasing, General Motors, Stephen Hubert, key account manager, Höegh Autoliners and Charles J. Franklin II, senior national manager, Business Development, Glovis America took to the main stage on the first day of the conference to discuss increasing transparency and lengthening contracts.
24 May
Our second Red Sofa from FVL North America 2024 sees Raúl Gamboa, head of Logistics, Production Control and Production Systems at BMW Group Plant San Luis Potosí speak to Richard Logan, senior content producer, Automotive Logistics about the progress and challenges facing the carmaker in the finished vehicle sector.
23 May
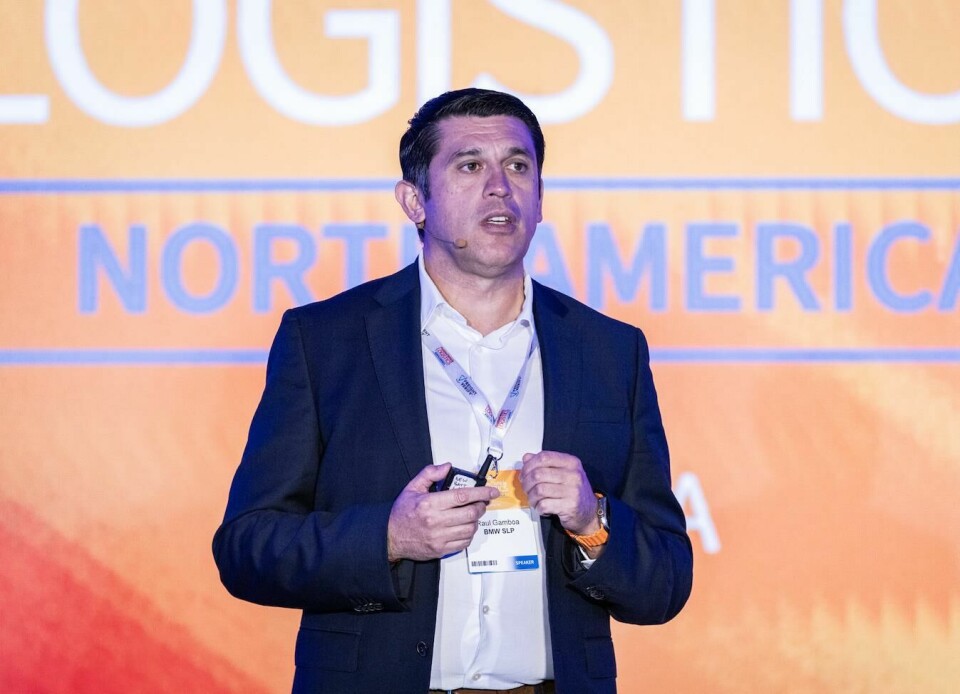
BMW Group’s Raúl Gamboa, head of logistics, production control and production systems at the carmaker’s San Luis Potosí plant in Mexico, outlined how his team squared up to the transport capacity constraints that several carmakers have faced in the region in the last year.
The San Luis Potosí plant makes 450 vehicles a day, with exports going to North America (32%) and Europe (50%). In 2023 Gamoa said that there were multiple external effects nationwide that caused disruption to outbound logistics. They included delay on delivery of 20,000 vehicles because of port congestion, the shortage of road-based haulage equipment and drivers, and capacity constraints for finished vehicle deliveries by rail. That meant that the plant’s vehicle inventory rose from around 2,000 vehicles to more than 14,000.
Ports have been congested for a number of reasons, including ro-ro vessel delays and the shortage of ocean and inland transport capacity for import/export volumes. Added to this however, Gamboa pointed to the federal government’s decision to gain better control of the country’s borders by allocating marine corps to take over on the customs process.
“This, of course, brings a different challenge because the army does not have experience of the automotive industry and sees that every industry has to be treated exactly the same way,” said Gamboa.
That meant space at the ports was contested and infrastructure strained, especially at Veracruz, which was not able to handle that amount of inbound and outbound vehicles shipping on established routes leading to a backlog.
“Many of the vehicles for export did not meet the vessel schedules and a lot of our truck capacity was captured at the ports and unable to return to the plant to pick up additional vehicles,” said Gamboa. “On top of that, we had issues with road transport capacity and it all created a big challenge for the logistics infrastructure.”
BMW Group needed to react very quickly and with creative ideas to solve the outbound shipments while maintaining quality. The logistics team acquired additional capacity on the spot market, including the use of flatbed carriers and by putting cars in containers. It also secured additional space at the port of Altamira for vehicle storage, and to build and release volumes to the shipping lines, which was constrained at Veracruz.
One of BMW’s main goals to manage vehicle exports was to gain greater transparency of the outbound supply chain.
“Our outbound operations are standardised with what we are doing in the rest of the world, but in this situation we found that we were not able to cope with [varied] information from our suppliers,” said Gamboa. “So first of all we decided to centralise all the information and develop digital tools to control that information enabling us to react and make decisions faster based on this information.”
The logistics team also redefined which KPIs were most useful to steer the mitigation action properly and took lessons from its inbound operation, including the creation of predictive tools. Importantly, BMW worked to improve working relationships with service providers, both inside the plant and in the wider network.
“Basically, we were looking for a long-term relationship with our partners and include them in the digitalisation and transparency setup that we were looking for,” said Gamboa.
With that greater transparency BMW Group has improved efficiency in its plant yard and port operations, said Gamboa. The carmaker has centralised information enabling it to react faster, supported proactively with predictive software tools. It is also supported by closer, longer term relationships with its logistics providers at the San Luis Potosí plant, helping it comply with the delivery dates given to customers.
BMW Group now has a healthier inventory level at the plant of 4,000 vehicles at the plant and fluid output to the ports of export. Gamboa said the company has created a sustainable strategy on output from San Luis Potosí. “These challenges of the last year may not be completely over but we able to react faster to deal with them.”
23 May
Good news - our Red Sofa interviews are back! We’re kicking off the sofa discussions with Nissan’s Steve Jernigan, who tells Automotive Logistics’ Richard Logan about the improvements and investments the carmaker has been making, and the challenges it’s facing, including US/Mexico border disruptions and the impact on the wider North American network.
23 May

Patrick Manzi, chief economist at the National Automobile Dealers Association (NADA), provided delegates at this year’s FVL NA conference with an overview of the sales and production performance in the US, a market still dominated by larger vehicles (80% light truck) but one in which buyers are also looking out for savings and sedans as inflation and interest rates take their toll. That is reflected in the fact that more affordable vehicles have a lower inventory level on the ground.
Monthly new loan payments average out at $722 in April, slight lower than the same month last year ($726), while average lease payments stand at $623 in the same month, down from $643 in April 2023, according to figures from JD Power.
The average transaction price for new vehicle stood at almost $47,000 (March YTD), while the used car average was just over $28,000.
US vehicle sales continue to hover just short of 16m, with the seasonally adjusted annual rate standing at 15.7m in April, and the fleet share of new vehicle sales accounting for 18%. The top three carmakers by market share year-to-date (YTD) are GM (16%), Toyota (15.3%) and Ford (13.1%). Crossover utility vehicles (CUV) are by far the segment with the greatest share, standing at 49.7%. The ever-popular US pickup was the next biggest segment YTD accounting for 16.5% of sales. Ford’s F-150 continues to take the lead in terms of model sales, with more than 198,000 sold in April. The Chevrolet Silverado and Toyota RAV4 were second and third.
In terms of powertrain mix, internal combustion-engine (ICE) vehicles accounted for 82% of sales, with pure electric vehicles, just 7% of the market, around the same level over the same period in 2023, according to Wards Intelligence. The share of hybrid vehicles increased by more than 2% on last year to take 8.7% of the market.
BEV sales in the US are expected to climb from around 1.5m forecast this year to more than 5.5m by 2029. Last year 1.1m EVs were sold and 40% of that volume through franchised dealers. According to Manzi, legacy carmakers will capture the market because a lot of people “just want to get ride of Elon”. Manzi said that BEVs will account for 35% of vehicle sales by 2029 and there will be alternative ways to purchase and own them, but the idea that BEVs would account for 60% of market by 2030 is far-fetched.
The average days of vehicle supply in the US stands at 51 for April, though there is considerable variance between brands, with Tesla standing at five days of supply and the Dodge Ram standing at 129 days, at either end of the scale. Pickup inventory stood at 74 days’ supply in April, with almost 704,700 on the lots. There is also variance by powertrain with EVs averaging 114 days of supply compared to ICE vehicles standing at 74, according to Cox Automotive.
Light vehicle production in the US is forecast to hit 16m this year, marking plant capacity utilisation at 83.3%.
Planned annual battery plant capacity in North America is expected to hit 1,200 GWh by 2030 (from 55 GWh in 2021). $100bn in investments.
22 May
Adapting to unexpected obstacles in a more innovative and exceptional way [see below] is also something Volkswagen Group has done in North America, as Anu Goel executive vice-president for group aftersales and service explained. That strategy was very much underlined by data-driven decision-making and collaborative relationships with logistics providers.
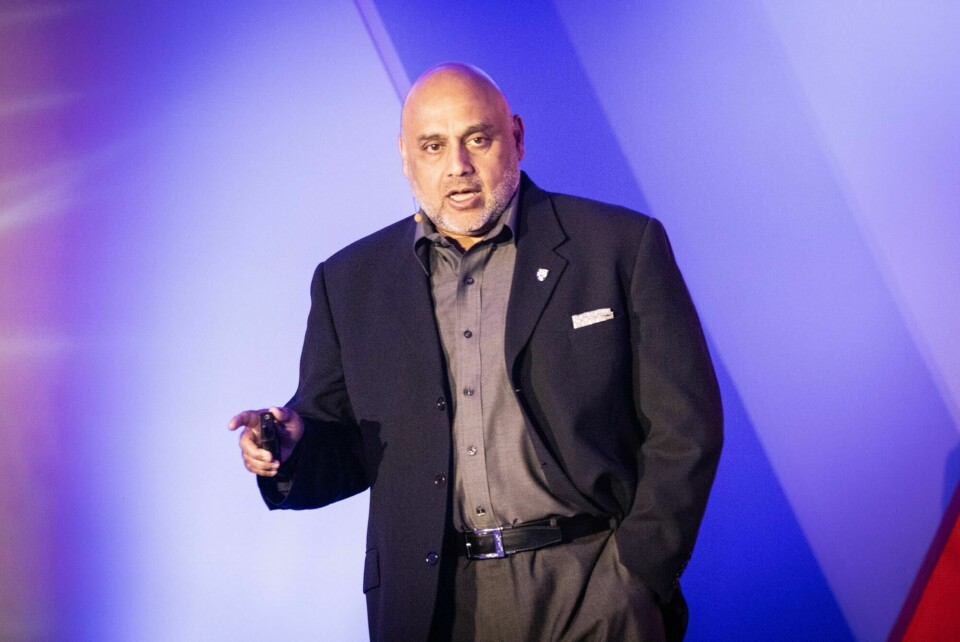
According to Goel, by May last year VW Group of America’s sales were up by 73% and the carmaker revised its production plan across North America and doubled it in June. By July, however, the whole world had been turned upside down. The transport capacity required to move vehicles from its Puebla factory in Mexico to the rest of North America did not materialise. The company was looking at $1.6 billion worth of vehicles on the ground in Mexico unable to move. There were a number of reasons for the backlog. They included a shortage of railcars and congestion at the port of Veracruz because of vessel arrivals that were between 5-8 days late. Tight ro-ro capacity was exacerbated by bad weather. There was also a shortage of road haulage equipment and the people to drive the vehicles to the port. Plant to port logistics was anything but smooth.
“ Immediate action was required and we needed to get the cars moving to support [North American] sales and reduce working capital,” said Goel, adding that working capital became another metric to factor in alongside cost, quality and dwell time.
The action taken included first thinking of North America as one region with one team, as opposed to the existing set up where the US, Canada and Mexico all had their own independent organisational structures for vehicle logistics, even though the movement of those vehicles was interconnected across North America.
VW Group of America started working virtually together as a single North American taskforce that met every day to look at what was going where, and how and when it could be there. Key performance indicators were brought into line.
“ We had to start doing things to make good regional decisions, which was the role of the taskforce that was working transparently and with a single source of data,” said Goel.
The carmaker worked to sign a long-term contract with one of the two finished vehicle rail providers working out of Mexico. It also connected with the purchasing department to get extra trucking capacity into Mexico. VW also opened a third port facility at Tuxpan in Mexico, just north of Veracruz, and chartered a dedicated short-sea vessel into the port of Houston. It also increased yard capacity at Veracruz and optimised shipping schedules that included two additional ro-ro vessels, with full visibility on vessel arrival. In addition, it transported 20,000 vehicles in containers to the US over 6-8 week period, moving from two cars per container to between four and five, which brought the higher cost for containerised vehicle deliveries down by roughly two to three times what it was.
VW Group of America is now moving short-sea volumes to the port of Freeport, which has storage space for 15,000 vehicles.
The whole idea, according to Goel, was to get cars moving faster through the system from Mexico to the US, with a 30-day delivery schedule from the end of the assembly line in Pueblo to the dealer network in the US. ”Every day you can take out of that frees up roughly 10-14m in working capital,” according to Goel.
Based on its hard work, innovation and agile response to the problem, VW Group of America has now announced a formal organisational structure for the US, Canada and Mexico that reports Goel.
22 May
In the first session of this year’s Finished Vehicle Logistics North America conference vehicle logistics leaders from Ford and Subaru talked about the benefits of disrupting the norm to deal with unforeseen interruptions to vehicle logistics. That change in approach to traditional methods through innovation, greater flexibility and stronger partnerships has proven valuable in dealing with the disarray the automotive sector has seen over the last year.
Paul Roosen, vehicle logistics planning manager for North American vehicle logistics at Ford, outlined how the carmaker had solved last year’s transport capacity problems for vehicle shipments out of Mexico to the US and Canada. Ford was down to between 60-70% railcar order fulfilment in the latter half of 2023, which was putting real strain on the network.
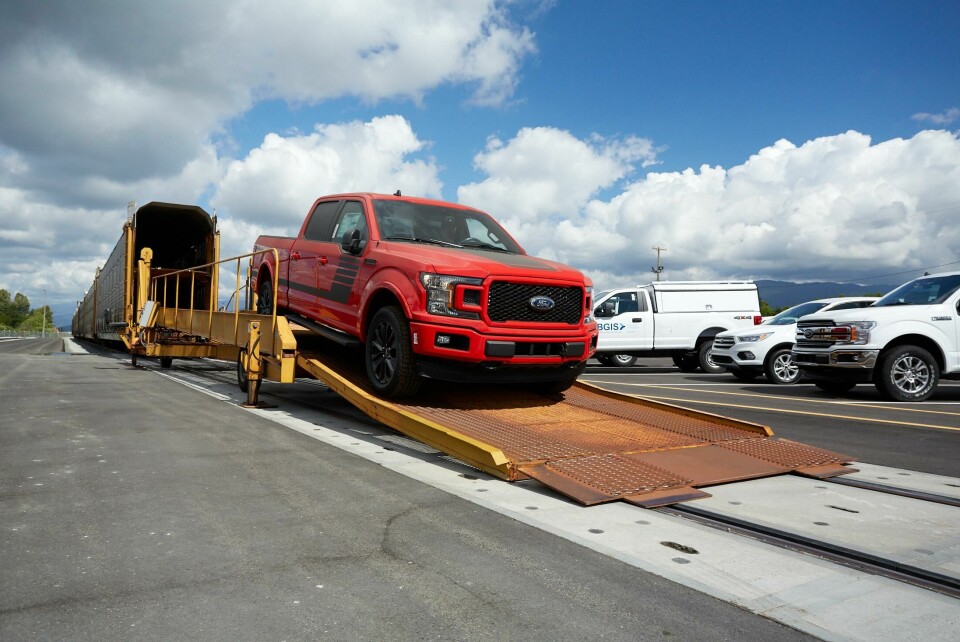
“What we did to try and mitigate some of this was to lean into key rail partnerships and look at how we could redesign our network to generate more empties and give ourselves more lift out of Mexico,” said Roosen.
Ford also benefitted from support at the port of Veracruz, which already has strong rail infrastructure. However, the tightness in railcar capacity meant Ford had to also rely on transport by road, which threw up a new bottleneck because Veracruz, the busiest North American vehicle handling port only had four gates for truck access. Now it has 19 thanks to a reorganisation by the port. That has helped Ford with short-sea exports to the rest of North America and for deep-sea exports to Europe.
For Subaru, innovation and flexibility came in to play at the Canadian port of Vancouver, through which it imports the majority of its vehicles for North America. Lisa Kline, vice-president of vehicle planning and logistics at Subaru of America, pointed out that the port hit its record for Subaru import volumes last autumn at a time of record throughput at the port in 2023. Kline recognised the tremendous accomplishment by the port but said that the record volume had to be moved inland to the dealership network in the face of railcar shortages, which required taking a new approach to inland distribution. That involved studying the metrics and looking a different ports of entry for a certain region of operations. Importantly for Kline, that did not necessarily mean new partnerships but working with existing logistics partners for a long-term solution.
Roosen added that the Pacific north-west ports have been dealing with significant increases in volumes because of ro-ro capacity and limits on vessels transiting a Panama Canal in drought which resulted in a land-bridge from the US west coast eastwards.
“When these networks got designed it was at a time when the ocean capacity was not there and the rates going through the Panama Canal were cost prohibitive,” he said. OEMs are now revising their approach and, like Subaru, looking at dual coast or multiport solutions on the west coast. Those are long-term adjustments but more immediately carmakers are having to rely more on long distance trucking and a hub and spoke strategy, for example, between the west cost port of Portland and hubs in Las Vegas, Denver or Chicago for onward regional distribution?
“It’s really hard to build those loads going to five or six different dealers originating from Portland, but if you can centralise them all into one location and disperse from there, it’s getting vehicles to market,” he said. “The last thing the dealers or the customers want to hear is that there’s a railcar shortage in Portland and that’s why they don’t have their vehicle.”
Kline added that scheduling was crucial to sustain the efficacy of each port and its labour force, and that meant ensuring port leadership had visibility of what was coming down the pipeline.
“We’ve had to pivot in certain ways over the past 12 months to make sure that the product was moving to the right place as far as allocation is concerned,” she said.
22 May
And the conference is officially underway! Catch up with the Welcome Cocktail Reception that kicked off Finished Vehicle Logistics North America 2024 in Huntington Beach, California, hosted by Jack Cooper. Automotive Logistics’ chief content officer, Christopher Ludwig, warmly welcomed a diverse group of industry experts, setting the stage for an event dedicated to exploring the theme of disrupting the status quo in finished vehicle logistics.
21 May
We are looking forward to seeing you today in California for our Golf Day, sponsored by KHS, ahead of our Welcome Drinks Reception hosted by Jack Cooper. We have a busy few days ahead!
Tomorrow, the conference officially kicks off. On the main stage, we’ll hear from FVL experts from the likes of Ford, Subaru of America,VW Group, the National Automobile Dealers Association, BMW Group, Nissan, Navistar, GM and more. Topics will range from disrupting the status quo and redeisgning logistics on the Mexican border to sales and production outlooks and increasing telematic data sharing, with ideas labs in between sessions on the main stage.
We hope to see you there! You can still register to attend here. Otherwise, keep an eye on this blog for the latest updates and insights.
20 May
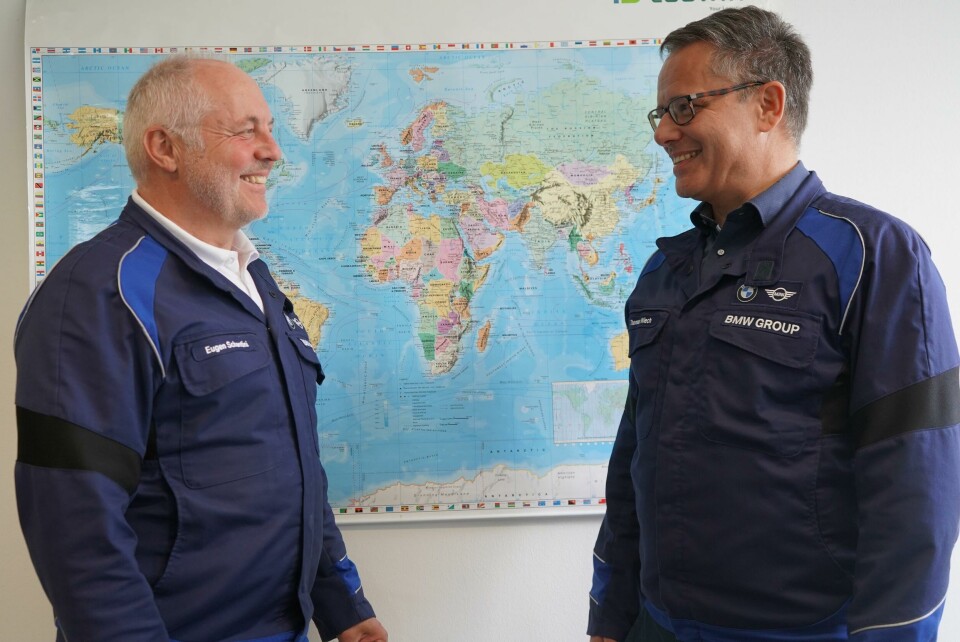
On Wednesday, Raúl Gamboa, head of Logistics, Production Control and Production Systems, BMW Group Plant San Luis Potosí will take to the main stage to discuss redesigning Mexico’s vehicle logistics to improve the North American network.
BMW Group has been utilising a new network strategy, as well as technology and tools, to manage disruption, secure capacity and plan ahead for a more sustainable outbound supply chain - something its heads of global vehicle distribution recently spoke to Automotive Logisitcs about.
Eugen Schantini and Thomas Wiech are responsible for BMW Group’s entire outbound transport network and believe it is important to know the location of every single vehicle in the network.
17 May
It’s only four days until FVL North America 2024 officially kicks off!
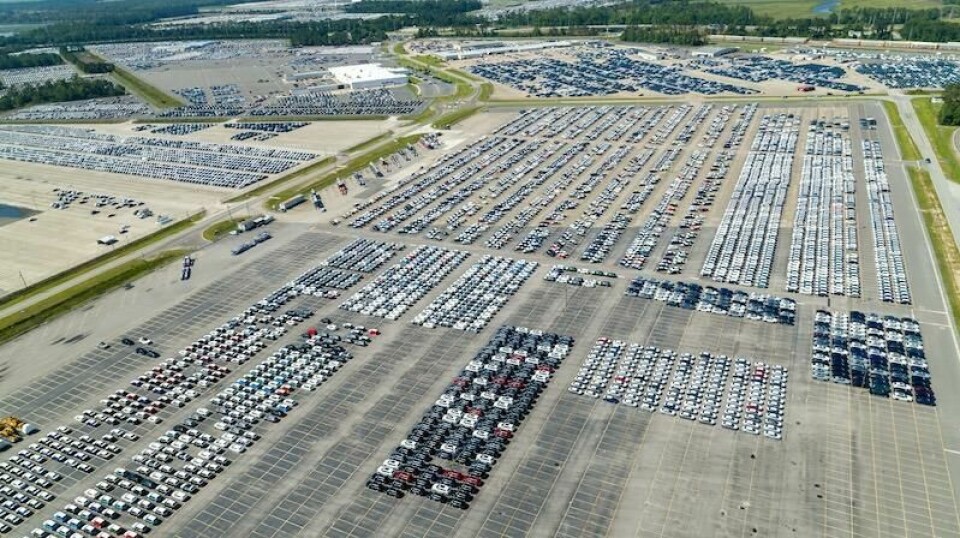
Whether you’re attending in person (there’s still time to register here) or planning to follow along with our blog, you can prepare for the event by getting up to date on the quickly evolving negotiations for rail workers in Canada. Threatened strike action could see North American FVL majorly disrupted, but as of today, Canadian Pacific Kansas City is resuming negotiations with Teamsters Canada Rail Conference union today in an effort to achieve a new collective agreement. Follow the latest news here.
Other modes of transport for FVL in North America haven’t been smooth sailing either, with recent disruptions having affected ports and congestion, culminating in March with the Baltimore bridge collapse. However, as our annual review of activity at the top-performing vehicle ports shows, that has only tested the mettle of agile cooperation between ports and inland logistics providers.
15 May
Lisa Kline, vice-president of vehicle planning and logistics, Subaru of America will be joining us on the main stage on day one of the conference this year to discuss how vehicle logistics needs to be re-imagined and why manufacturers and logistics providers must disrupt the status quo to raise the network’s performance.
Kline, who was appointed to the role in April last year, has been working to lead Subaru of America’s logistics team to more success through a balanced logistics and distribution network design. She previously spoke to Automotive Logistics about the importance of the carmaker’s long-term relationships with its suppliers and logistics providers, and the ethos of the Subaru Love Promise that extends across the supply chain and production.
Subaru’s vehicle logistics and distribution network design is one factor that likely supports its stable and reliable operations. Out of the OEM’s yearly volume of roughly 675,000, 337,000 are imports and 338,000 are produced domestically at the carmaker’s plant in Lafayette, Indiana, run by Subaru of Indiana Automotive (SIA). The carmaker’s import ports are evenly spread throughout the country, for example, helping it to balance distribution flows. It exports around 50,000 units out of Indiana per year and serves 639 retailers across the US.
Subaru also has an almost 50/50 split across rail and road shipping, with 52% of vehicles shipped by railway and 48% in truck volume. “It’s very unique that those volumes are so close to one another right now,” said Kline.
15 May
In May this year BMW started shipping the new Mini Countryman, including its battery electric versions, from its Leipzig plant in Germany to the dealer network in Mexico. BMW began producing the combustion-engine Countryman at the Leipzig plant in November last year and in March this year added production of the EV in two versions – the Countryman E (150 kW) and the more powerful all-wheel Countryman SE ALL4 (230 kW).
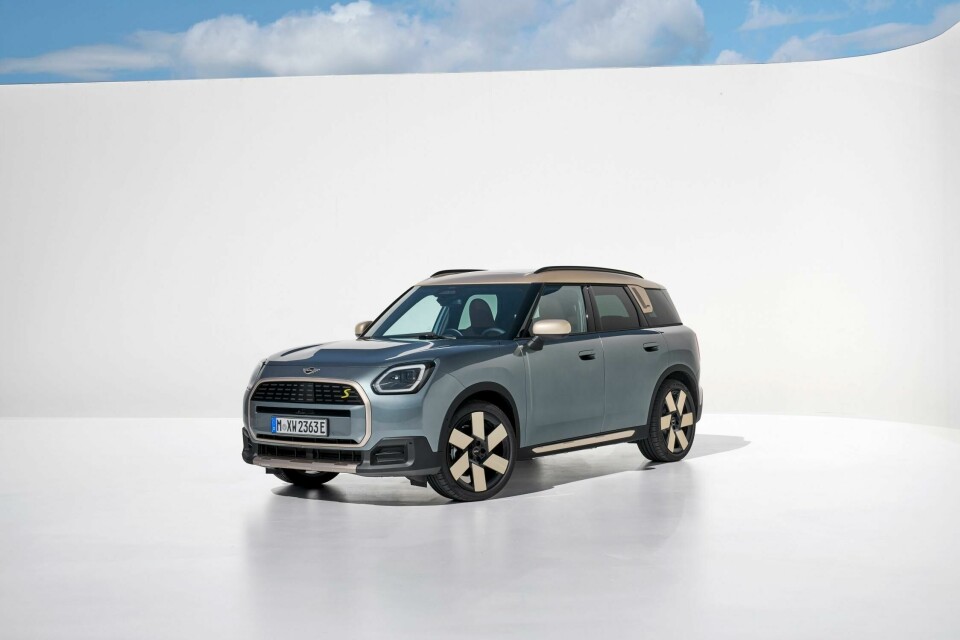
Arturo Orenday, director of Mini Latin America said that Mexico is the country that sells the most Minis in the Latin America region.
Along with other BMW exports to Mexico, the Minis are being taken by rail to the German port of Bremerhaven for export and delivered through the Mexican port of Veracruz. The cars are being distributed by truck from the compound at Santa Rita near the port to the respective dealers.
At the same time, BMW is taking its ‘local for local’ approach to manufacturing and supply chain to Mexico and has started construction on an 80,000 sq.m battery manufacturing facility next to its assembly plant in San Luis Potosi. The plant is due to start making the Neue Klasse electric sports activity vehicle there from 2027. The carmaker has not confirmed whether Mini electric vehicles join the production line at any point.
The San Luis Potosi plant currently builds the BMW 3 Series sedan for the global market, and is the exclusive production site for the BMW 2 Series Coupe and BMW M2. BMW said it currently had no plans to build the Mini Countryman in Mexico.
14 May
Next week’s Finished Vehicle Logistics North America conference in Huntington Beach, California will kick off with an opening session focused on reimagining the finished vehicle logistics network to enhance performance in the face of capacity shortages on land and sea. Ahead of that, Christoph Seitz, global vice-president for finished vehicles at DP World, has revealed a new service that DP World is providing for carmakers exporting vehicles from Mexico to the US and Canada.
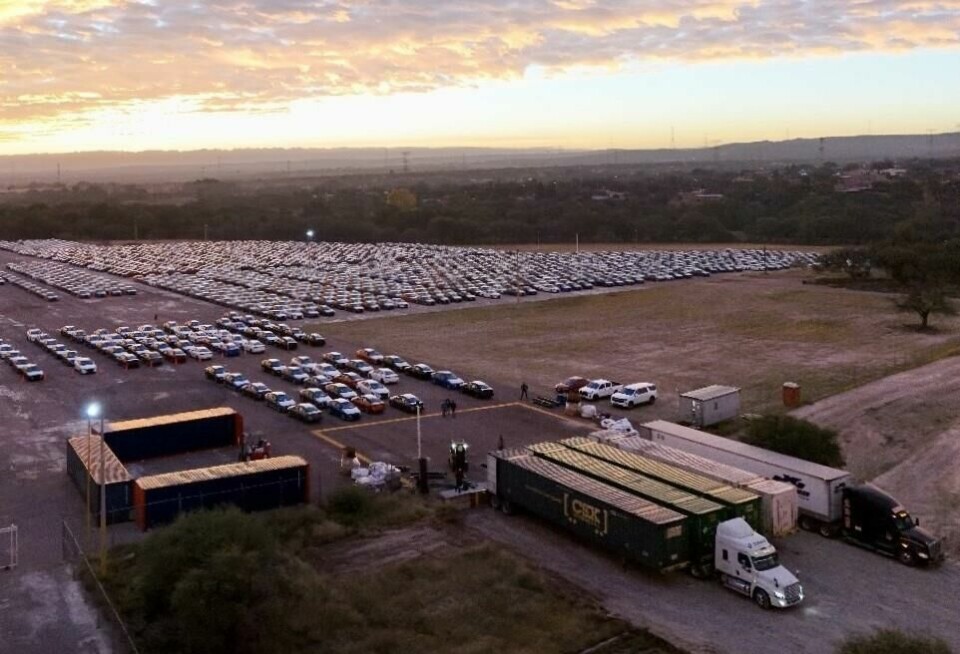
Following initial volume shipments in the first quarter of 2024 for a major OEM, from June DP World will be providing an intermodal rail service for containerised car shipments between Mexico, the US and Canada. The port terminal and inland logistics provider is using 16-metre (53ft) containers with racking systems in answer to the ro-ro and multilevel rail-capacity shortage for vehicle shipments in North America.
The 16-metre containers, which are common for general freight shipments in North America, will use special racking systems that can accommodate six vehicles per container for smaller passenger cars, compared to the four maximum that can be shipped in a standard 12.2m (40ft) container. Seitz said that enhances efficiency and reduces costs for OEM customers. DP World said it is the only logistics company currently providing the intermodal 53ft container solution for finished vehicles.
At the conference next week Seitz will be joined by Ford’s Paul Rooson vehicle logistics planning manager for North American vehicle logistics, Lisa Kline, vice-president of vehicle planning and logistics at Subaru of America, and Sean Baltazar, senior vice-president of sales at RPM.
Read more about the new DP World service
13 May
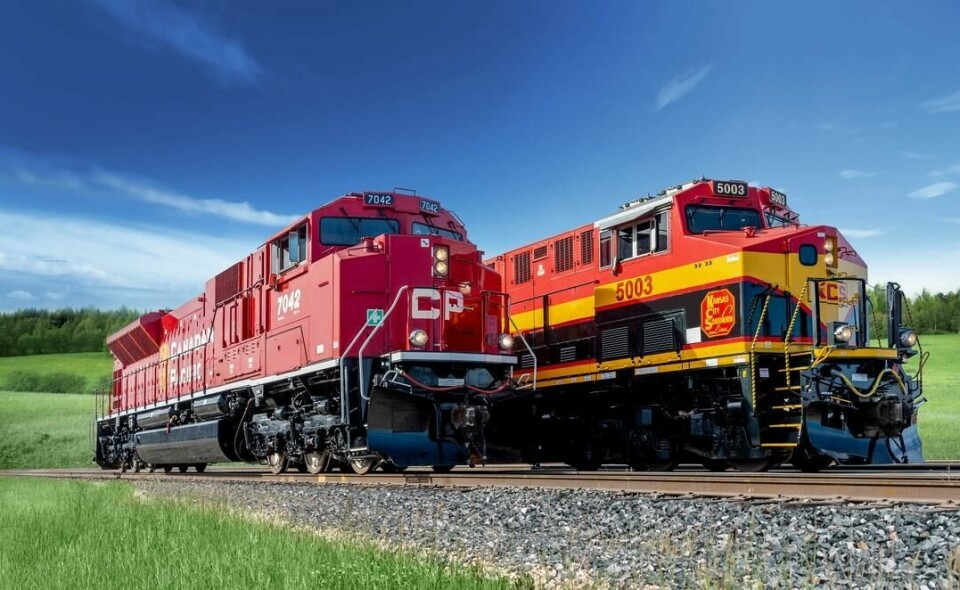
As we begin the countdown to Finished Vehicle Logistics North America 2024, taking place in Waterfront Beach Resort, Huntington Beach, California from 21-23 May, Automotive Logistics will share news and features that will tie into discussions on the main stage and feature some of the experts that will speak at the event, keeping you in the loop and armed with topics to discuss while networking in sunny California!
During the conference, we will hear from Raúl Gamboa, head of logistics, production control and production systems at BMW Group Plant San Luis Potosí and Steve Jernigan, senior director of supply chain management, Nissan North America, among others, about the importance of rail investment, particularly as Mexico becomes an increasingly strategic region for FVL.
Rail providers are looking at mergers and acquisitions, investing in infrastructure and digital technology, and collaborating on efficiency gains and network design, including with providers of road freight services to improve the sector’s efficiency. Automotive Logistics took a deep dive into how Class 1 rail providers are responding to demands on capacity, by working collaboratively and investing in technology and infrastructure for a more sustainable vehicle deliver network in North America.