Covid and semiconductor crises have ‘pushed logistics industry forward’
The pandemic and the semiconductor shortage have encouraged more visibility and transparency between OEMs and automotive tier suppliers, helping the industry not only to recover but to advance further, according to experts.
During this year’s Automotive Logistics and Supply Chain Global conference in Dearborn, Michigan, a panel of experts said the crises have exposed areas of weakness within the supply chain and provided lessons for the sector.
Renee Wawrzynski, executive director, Global Logistics at GM said: “It all starts with Covid, when we all thought we would shut down plants for a couple of weeks and come back and everything would be normal, but we’re still not back to normal. We discovered where our tier supply base was located while Covid was going around the world, and then with the semiconductor crisis too.”
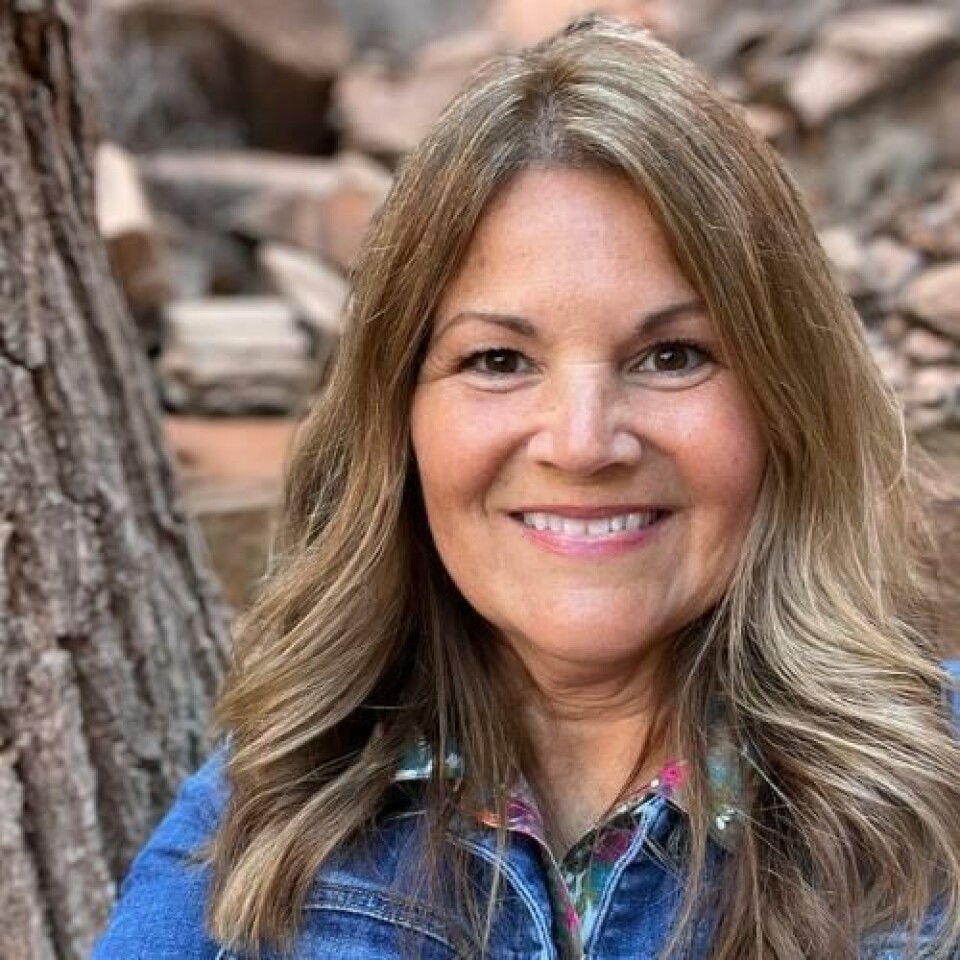
She said that pre-pandemic, GM didn’t have complete visibility of its entire tiered supply base. “We knew that we didn’t have that, but we didn’t know what the impact was going to be,” she said. “We have that data now, so we’re going to be better moving forward.”
The situation continues to be dynamic, but now there is better visibility which helps OEMs and suppliers to be more flexible and able to adapt. But Wawrzynski said carmakers need to ensure their suppliers know how to access this visibility, and have enough resources for it.
“Particularly on the FVL side, visibility, capacity planning and making sure the investment is there is so important, and we probably have to do a better job on providing that future outlook and what the volumes and flows are expected to be,” she said. “We provide a two-year outlook by month for every one of our assembly and production plants on our supplier portal, but I’m not sure if everyone knows that information is there. Our tier-1 suppliers do, but on a wider scale I don’t know. I think we can work better together with the providers to share data back and forth, and there is opportunity for new technology and more sharing on both sides.”
Similarly, Chris Styles, vice president, Supply Chain Management for Nissan North America said: “Our ability to predict became very hard during those challenging times, and sometimes we’re able to [predict] but our suppliers cannot, because they had to cut back during those challenging times and maybe they don’t have the money or the resources needed for that visibility.” He added: “We’re going to have to continue to balance our priorities. The suppliers are starting to invest in this, but this type of resource doesn’t come within a week.”
Speaking about the lessons learned following the semiconductor shortage, Wawrzynski said: “One of the things that came out of that crisis was that we have so much proliferation in the types of semiconductors that we had, so we completely reengineered our supply chains going forward. Unfortunately, it always takes a crisis to do these kinds of things.”
For more insights from ALSC Global 2023, follow our live blog here.