Audi special report: Managing from the centre and the periphery
As ever with a sprawling entity like the Volkswagen Group, power shifts between the centre and its satellites. In Wolfsburg, Konzernlogistik (group logistics), led by Thomas Zernechel, has responsibilities that include group programme planning, setting standards (including IT and returnable packaging) and transport tenders. It also manages bundled and network transport flows, including ocean containers and ro-ro shipping, and consolidated logistics for all suppliers in the transport network.
Audi special report: Vorsprung durch Logistik
-
Audi special report: Vorsprung durch Logistik
-
Audi special report: Managing from the centre and the periphery
-
Audi special report: Strong at the core
-
Audi special report: A fast, flexible network
-
Audi special report: A question of complexity and convergence
-
Audi special report: One crossdock, many brands
-
Audi special reports: A global outlook
-
Audi special report: Outbound delivery accuracy
-
Audi special reports conclusion: Experts at managing change
At the other end of the spectrum are the plants, each with considerable autonomy over operations and planning, especially for in-plant and logistics centres, as well as direct inbound and just-in-sequence deliveries.
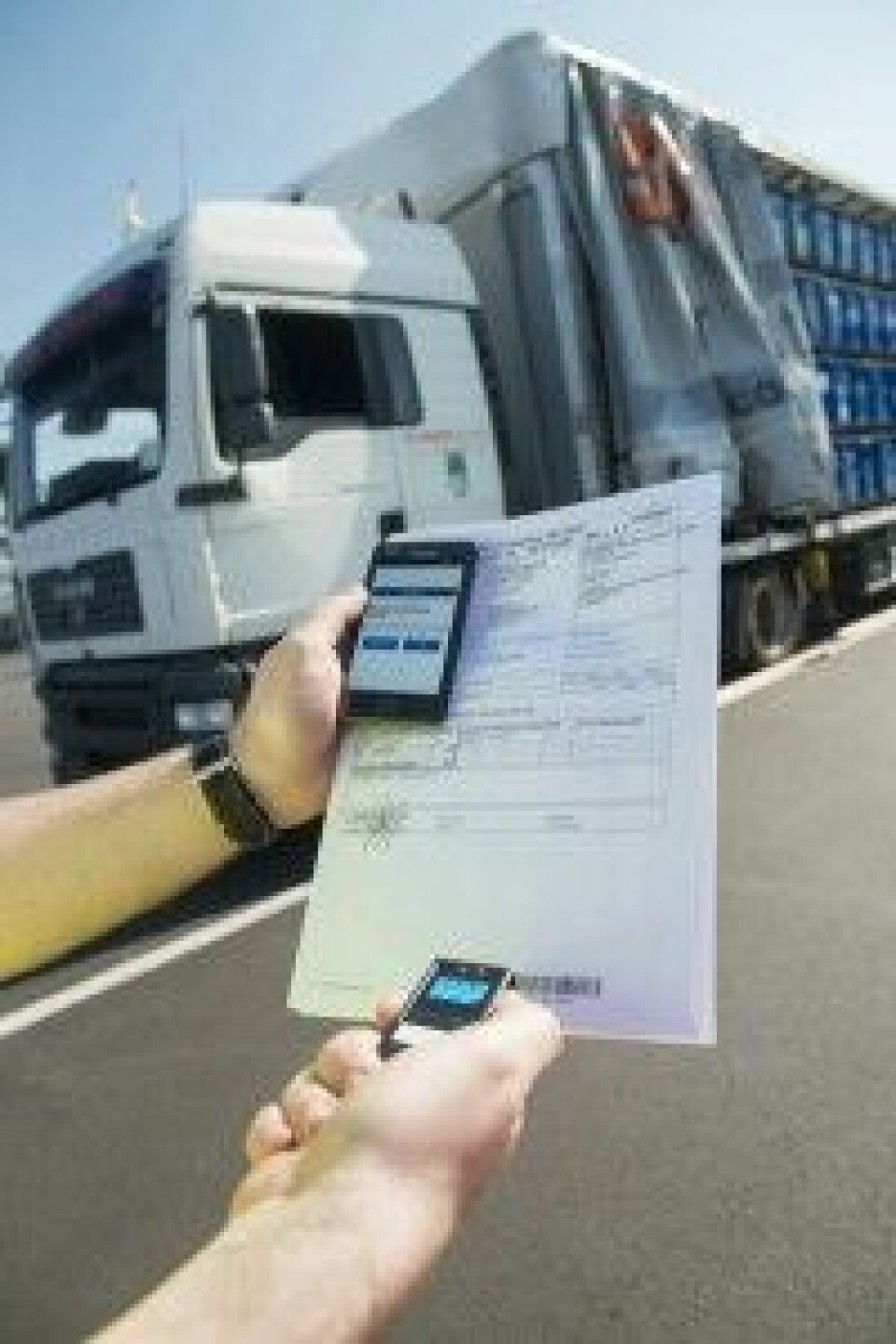
Markenlogistik (brand logistics) sits between the capital and the villages, so to speak. Dr Michael Hauf oversees Audi’s cross-plant logistics processes and areas that include inbound and outbound transport, concept and programme planning, pre-series logistics, information processes, and international logistics. Brand logistics represents logistics on two group-level committees.
“Brand and plant logistics work closely with each other, so that all the planning and systems processes are defined at a brand level, and we plan, operate and adjust to the daily reality at the plant,” says Johannes Marschall, head of plant logistics at Ingolstadt.
While responsibilities for plant, brand and group logistics are distinct, there are overlaps. Procurement is a group function, but each brand has its own purchasing, while each plant has its own disposition. Much of the selection process for inbound and especially in-plant logistics providers is carried out locally at plants together with brand management. “For example, if Neckarsulm is looking for a new LSP, we [plant logistics] get involved with the Audi freight purchasing department and together we make a bidding list,” says Dieter Braun, head of production control and plant logistics at Neckarsulm. “The final results go through Wolfsburg, but the other processes stay with us.”
However, the co-location of models across brand and group plants, as well as more shared suppliers, requires more central control. “You need one common point from which to control the suppliers, so the more that you have common production at plants, the more you need a common function,” says Hauf.
Examples already include a move towards group-wide crossdocks, including an important operation in Bratislava. There could also be potential for a more active sharing of logistics providers within the group. Today, although Audi may share providers with other group brands, it is not the result of both brands having jointly contracted these providers. Often it is a case of regional overlaps or even shared facilities, such as at the packing centres in Kassel or Martorell. However, in future the brands could consider jointly assigning providers.
Regardless of the balance between plant, brand and group control, the centre is only as strong as its periphery. Hauf points out that innovations often come from plants, be they IT systems or sustainability concepts. It’s the role of brand and group logistics to take the best ideas across plants, and turn them into global standards. For example, a performance tracking system that started in Neckarsulm, which documents all information on truck arrivals, accuracy and part quality, has now been rolled out at a group level.
Ingolstadt, meanwhile, has recently introduced a GPS-based ‘geo-fencing’ system – part of software-provider Inform’s truck appointment system – that automatically monitors trucks up to 50km away and allows them to check in while still on the road. Having recently won a group-wide innovation award, this system will be extended to other group plants, says Hauf.