You gotta carry that weight: how bigger vehicles and EVs will challenge logistics
With forecasts for strong growth in marketshare for electric vehicle and hybrid vehicle sales over the next decade, moving parts and vehicles will require new equipment, processes and standards across OEMs and logistics providers
Despite efforts by OEMs to use lightweight materials, average vehicle weights are generally going in the other direction. According to our estimates, vehicles are putting on about around 10kg more each year – and could become portlier still as sales transition more to electrified powertrains (see our full report and powertrain forecast to 2030). This will have implications for logistics providers, including finished vehicle logistics equipment and processes.
Vehicle weight is rising because of changing consumer preferences as well as regulations. There has been a notable global shift – encouraged by OEMs – to larger and heavier SUVs and crossovers over sedans and compact vehicles (in the last six years the sales mix in the US, for example, has shift from being 50:50 light trucks and SUVs versus sedans, to more than 70% light trucks). Tougher crash protection regulations, such as Euro NCAP and US NCAP, also require OEMs to add more material to crumple zones and impact areas. Thirdly, customers expect more features and technology as standard, such as air conditioning, electric windows and infotainments systems, which all inevitably add weight.
And that’s just for a standard internal combustion (ICE) vehicles, which on average weigh around 1,400kg. Electric vehicles, meanwhile, tend to be heavier, thanks mainly to batteries that are typically 300-500kg. According to our analysis of top-selling models, EVs currently weigh around 1,600kg on average.
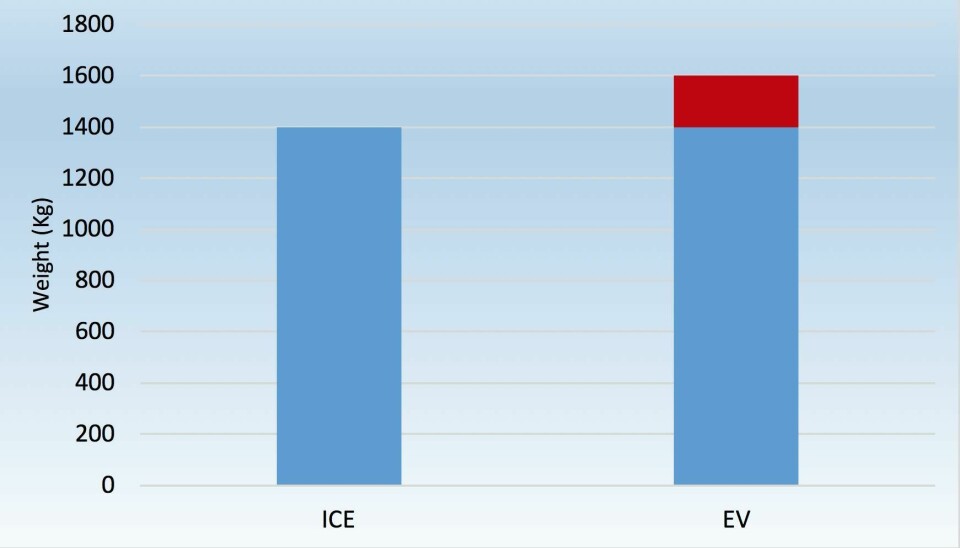
Download our global powertrain forecast and analysis below
Electric vehicles do save weight in some areas compared to ICEs where they have fewer parts, especially powertrains modules like engines and gearboxes. But range is critical for EVs and installing larger batteries helps achieve this. ‘Full hybrids’, which have combustion engines as well as electric motors with smaller batteries (such as the Toyota Prius), also typically weight more than standard ICEs. However, this extra weight is not mere flabbiness on EVs. With technology such as regenerative braking, the car’s bulk can actually help charge electric motors as energy is recovered during braking.
Nevertheless, vehicles are set to get heavier still, including a higher growth of electric SUVs and pickup trucks. According to our latest forecast and analysis (download forecast below), electrified powertrains are set to gain substantial marketshare among new vehicle purchases over the next decade, with battery electric vehicles rising from around 2.5% of global sales currently to around 15% by 2030, and hybrid variants also growing strongly in many regions.
More weight on LSPs shoulders
More EV production and sales will challenge automotive logistics providers, adding more complications and likely more costs. Regulations around the transport of hazardous battery cells, modules and packs, for example, vary from region to region; they are not permitted on commercial flights and require specific packaging and handling because of their flammability and hazardous material status. While more logistics providers are gaining certifications to handle this equipment, there is still a general lack of standards across regions, despite the global nature of EV battery production and supply.
The weight of the battery and vehicles themselves could also be an issue for finished vehicle logistics providers. Many legacy car carrier trailers are not designed to cope with the size and weight of these larger, heavier vehicles coming to market. Carriers often face weight limit restrictions for operating on roads in certain regions. In the both the US and EU, for example, full loads of some model types would already exceed regulated limits. Extra weight also means higher fuel costs (with a mass electrification of heavy goods trucks unlikely in the medium term).
The changing dimensions of vehicles also complicate investments in vehicle logistics assets like trailers, rail wagons and ships, many of which last 20-30 years. The industry is poised to shift dramatically to electric and alternative energy vehicles in the coming years, but at different paces across regions. A combination of more flexible equipment, retrofitting and close communication with OEM models plans will be critical.
Electric vehicles present operational problems for vehicle logistics providers loading many vehicles onto car carrying trailers or a freight liner at port. For example, the state of charge required for vehicles at different points of the supply chain, such as in compounds, varies by OEM. There are also questions of charging infrastructure within port and distribution centres, and how longer charging times might impact overall loading processes and delivery time.
Staff require additional training on how to charge and handle all the different types of EVs, especially procedures in case of electrical faults or fires. Weather can also impact how and when vehicles are charged. Vehicles waiting for longer at compounds may need batteries and other electrical systems disconnected to avoid issues, which in turn have certain requirements when they are reconnected.
None of these issues is insurmountable for logistics providers, or necessarily more complicated than other technological changes to vehicles. Where the industry currently struggles is in a lack of common standards among OEMs even in one country let alone regions. To keep things getting too heavy in the shift to electrification over the next decade, OEMs need to work in closer coordination with their service providers.