Why just-in-time will remain the way forward for Toyota
Leon van der Merwe is leading inbound, outbound and service parts logistics for Toyota Motor Europe. At this year’s Automotive Logistics and Supply Chain Europe Live conference he told Christopher Ludwig about the carmaker’s strategy to modernise just-in-time and make Toyota’s logistics more sustainable
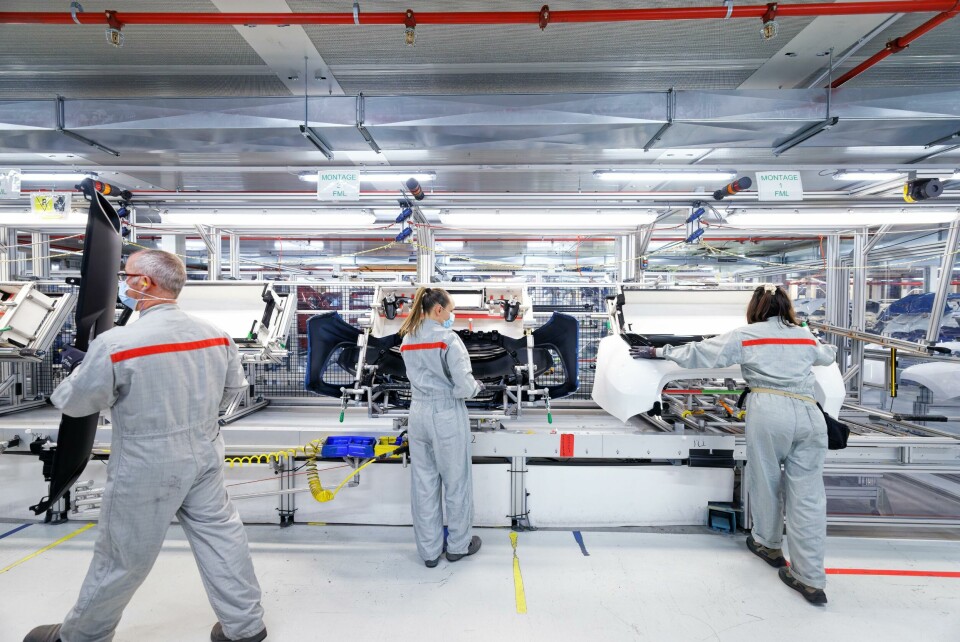
The death of just-in-time supply chains may have been greatly exaggerated.
While material and chip shortages, along with delays to container shipping, have strained automotive manufacturers’ low inventory strategies, to blame lean supply chains may in some ways misinterpret the principles of the Toyota Production System (TPS) and just-in-time logistics. When executed correctly, with the right balance of visibility and partnership, the kanban system of replenishment at the heart of TPS is based on a steady flow and smoothing bottlenecks – in effect leaning inventory where possible, and balancing stock with the right level of demand and production.
For lean experts, carmakers like Toyota may have been able to manage current disruptions better than others thanks to JIT – rather than in spite of it.
For Leon van der Merwe, vice-president of supply chain at Toyota Motor Europe (TME), TPS and JIT will remain at the heart of the carmaker’s strategy, including its ambitions to reduce emissions and meet sustainability goals in the coming years. He does, however, envisage modernising and strengthening Toyota’s JIT strategy, bringing sacrosanct processes up to date with new technology and ensuring the company has greater visibility in the supply chain beyond its tier one and two suppliers.
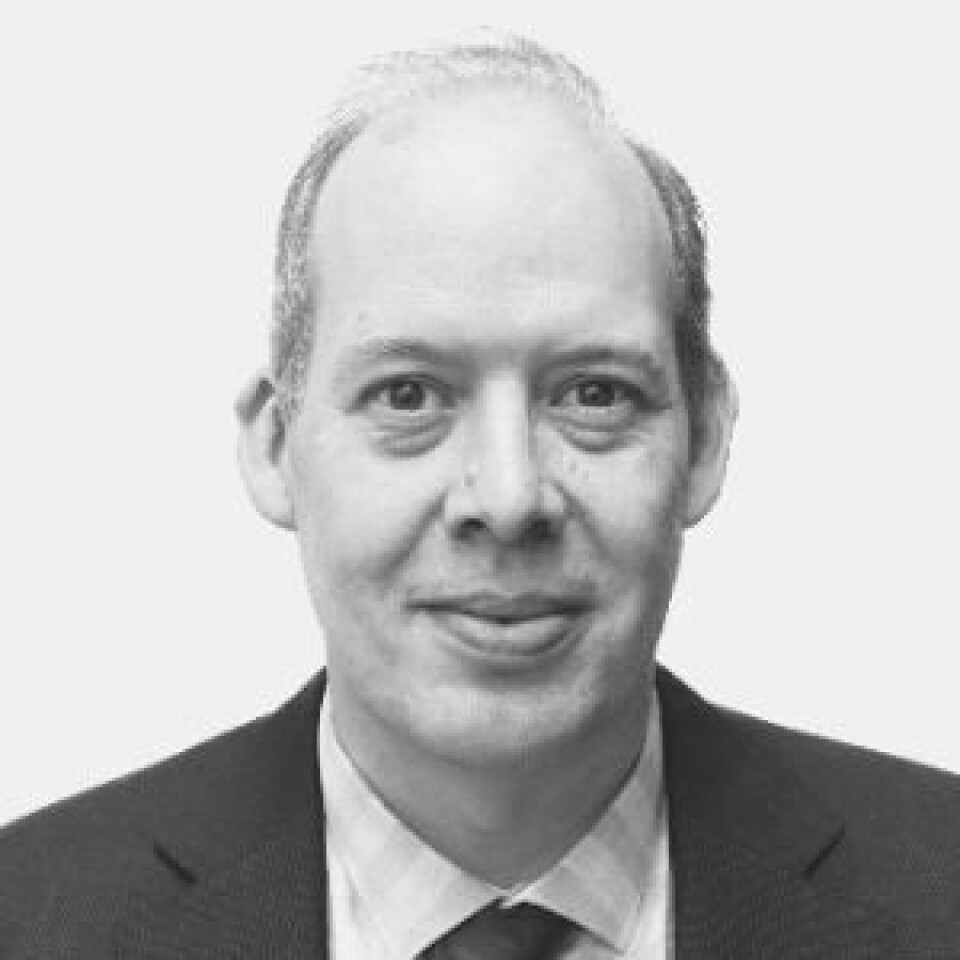
According to van der Merwe, TPS enables Toyota to take waste out of its supply chain network by accurate visualisation of the steps and the suppliers involved. JIT supply chain management is not simply about reducing stock, rather it is about having the right inventory where it needs to be when it is needed. That allows any problems in supply to be identified and solved more quickly but it also reveals where Toyota can reduce waste and emissions.
Under van der Merwe’s direction in Europe, the carmaker is setting out for its logistics sustainability programme to catch up to the progress it has begun to make in manufacturing, including a more strategic use of transport modes, a greater focus on rail and multimodal, cutting truck kilometres and the adoption of sustainable fuels for last-mile truck deliveries.
Van der Merwe also explains that part of his role is to make sure the decision makers in R&D, purchasing and manufacturing understand the impact of their decisions on Toyota’s supply chain both in terms of cost and environmental. That is important in a company in which decision making has totally changed and become a lot more cross-functional, including in the wake of the coronavirus pandemic.
The company has also gone through some organisational changes as it seeks a clearer end-to-end vision of its supply chain and logistics. That move has given van der Merwe responsibility for inbound, outbound and service parts logistics, a new integration for the carmaker in Europe. While those three areas are essentially distinct, they are built on common foundations that include safety, environmental sustainability and people development, and bringing them together gives Toyota more opportunities to optimise processes, systems and develop skills.
Since van der Merwe walked into the role in 2019 he has seen major upheavals including the coronavirus crisis and the UK’s departure from the EU, and most recently the semiconductor shortage. He also oversees a supply chain that is having to adapt to the seismic shift to electrification, driven in Europe by strict regulatory demands on cleaner transport. It has all required greater flexibility as mobility patterns change and the consumer demand for immediate gratification grows ever stronger. But Van Der Merwe is intent on being better prepared and self-sustainable in the face of what comes next, and he is confident Toyota’s supply chain and logistics principles will help it to meet the coming challenges.
Christopher Ludwig: Toyota has its own net carbon zero targets and there are initiatives underway. What will they mean for European logistics?
Leon van der Merwe: Toyota first introduced its zero emissions targets about five years ago. It was about how we achieve zero impact on society by 2050. It is core to what Toyota thinks. The purpose of doing this is how we influence society. We have brought in hybrid vehicles and we have brought in hydrogen vehicles. Within the [vehicle] lifecycle we have done a lot to reduce [emissions]. Within manufacturing, for example, our sites are 78% less impactful to society today than they were five years ago [in terms of pollution].
For us in logistics going forward, we believe the starting point is a strategy taking in three areas: how do we reduce the impact of our sites, how do we reduce our impact through plastics – the supply chain is after all single use and plastics hungry – and how do we neutralise the CO2 impact of our transportation. That is going to be the most difficult area because the first challenge I’ve come across is that no one across the industry measures the CO2 impact in the same way. The first thing we have to do is standardise the way we measure it.
Then it is about how we do the things in supply chain we should always be doing. That is about more efficiency, better truck density, fewer kilometres. Once that is optimised then it is about looking at alternative fuels and alternative modes that are less impactful to the environment.
Ludwig: Do you now have that standard for measuring the impact of logistics or are you still looking for it, and should it be a standard for Toyota or across the industry?
Van der Merwe: It should absolutely be an industry standard. We haven’t got it in Toyota yet. A KPI [key performance indicator] should be something you use to manage and change your business. Too often the tendency is to take a KPI that makes us look good. What we have really got to do is find a KPI that will allow us to manage our business so that by 2050, and by our own standards, we have zero [environmental] impact on society. That is what makes finding the right KPI so difficult.
Ludwig: What are the most important long-term objectives that you would identify now?
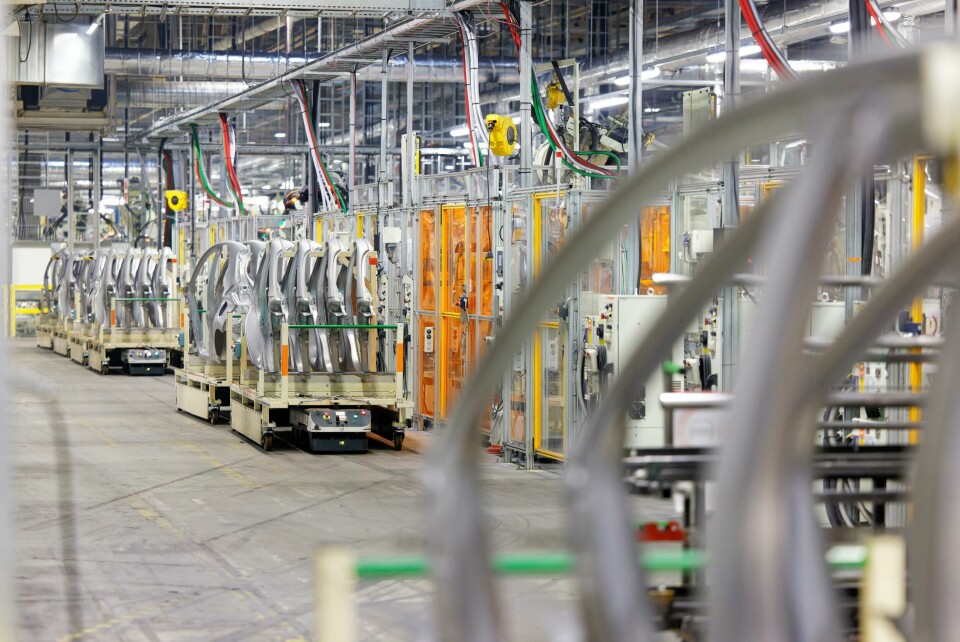
Van der Merwe: The change of transport mode is both short term and long term. A lot of that structural change of mode takes a lot of investment. Do you have the right railheads? Do you have the right rail wagons? Are the trucks optimised for their routes.
Longer term the two real challenges are rail and what is the right fuel type in trucking. It doesn’t matter how much we can move to rail, last mile is always going to be reliant on road transport. So how do we get the road transport to a point that it has zero emissions? That is one of the biggest challenges.
Ludwig: We see the industry using biofuels and compressed natural gas (CNG) or liquified natural gas (LNG). How important of a role in the short to medium term can those fuels play in greener logistics?
Van der Merwe: Toyota and everyone else in the industry has to start experimenting. Whether we look at LNG or CNG, or hydrogen, the big challenge is the infrastructure. Until the industry starts investing and using some of these alternative fuels, the government and the rest of the support industry are not going to start moving in that direction. That to me is the big question that we don’t have an answer on. But we must answer it in the next few years. If we are going to move to hydrogen, we will need hydrogen stations across Europe and make sure it works. That is nowhere near ready to happen at the moment, neither in strategy nor concept.
Long-term as an industry we need to lobby the government to go in the right direction but first we need a clear picture ourselves of what the long-term strategy is. Some alternative fuels are very good as stop gaps, while others are the long-term solution. Right now, as an industry, I don’t think we all agree what the long-term solution is.
Ludwig: Do you see TPS and JIT working as core parts of the greener supply chain strategy or do you see some evolution in those processes?
Van der Merwe: Toyota will never achieve its 2050 [environmental] goals without TPS. The principle of TPS is how to eliminate waste and visualise your supply chain to make sure you can see abnormalities. This is not something that you suddenly do after the fact. TPS is the principle on which we build our supply chain network. That is what makes it successful.
One of the big misunderstandings of JIT – which included my misunderstanding when I joined Toyota – is that the purpose of JIT was to reduce stock. But actually, the ultimate target of JIT is to have the right stock in the right place at the right time because this allows you to visualise where you will have problems and therefore react quickly to solve them.
One of the big misunderstandings of JIT… is that the purpose of JIT was to reduce stock. But actually, the ultimate target of JIT is to have the right stock in the right place at the right time because this allows you to visualise where you will have problems and therefore react quickly to solve them – Leon van der Merwe, Toyota Motor Europe
If I have got too much stock in one area, I will not find out that my supplier has a problem until all of that stock is used up. If I only have just enough stock to produce for the next hour, I can see within an hour that my supplier has a problem. I can therefore get involved and solve the problem.
Kanban is a pool system that starts with the customer. When one customer buys one car, each station orders one part. That goes back to the supplier and then it goes back to the sub-supplier. It is more complicated than that but that is the principle: one step at a time. Where we know we then have bottlenecks we put in a small buffer stock. It is not that we don’t believe in stock, it is about having the right stock in the right place to make sure that the next process doesn’t stop. Given the visibility, when you look back you can see your whole supply chain.
Ludwig: How important a role do you see regionalisation and local sourcing as part of a sustainable supply chain and does logistics cost and inventory will play a bigger role in the purchasing strategy?
Van der Merwe: Toyota’s principle when it started was to have as many suppliers as close to its factory as possible. This has been a principle for 50 years when TPS first started, in terms of how you bring as many of your suppliers as close as possible. That makes a very visible supply chain. That means for many years Toyota had taken total cost of part into account: purchase price, logistics price, disruption price. Everything to make a decision about the part.
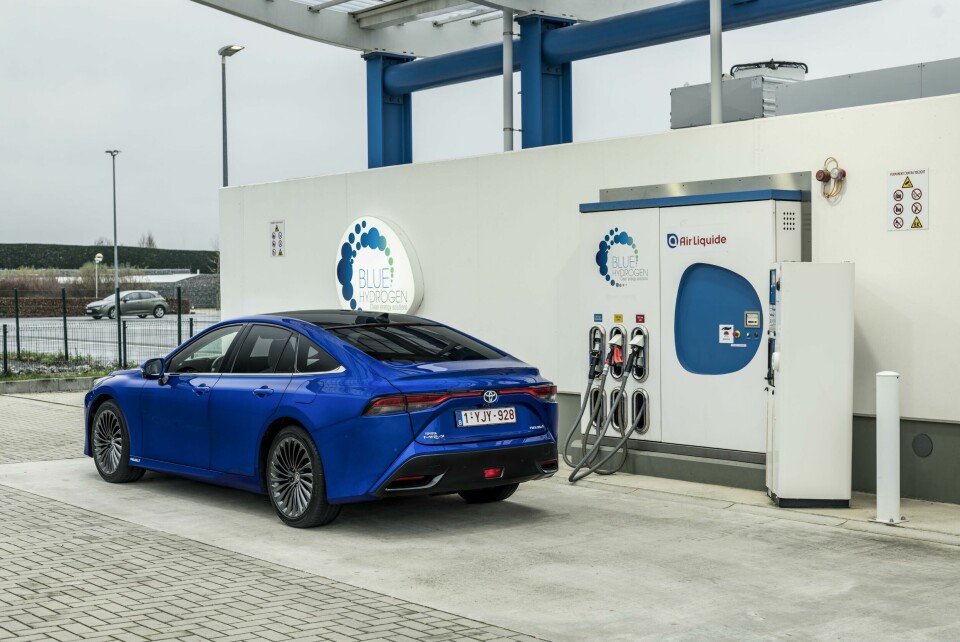
It is now a case of how we integrate CO2 impact into that same decision. Not CO2 impact of logistics but CO2 impact of total supply chain. That is the way you make the difference.
Ludwig: Toyota is highly advanced in hybridisation and is looking to ramp up battery electric vehicles and fuel cell electric vehicles, although you are not yet producing them in Europe. What are the key factors in logistics planning to support the eventual scale of production and distribution of these products?
Van der Merwe: Moving an EV brings some challenges. Transporting batteries is extremely difficult and different to moving engines. They are both heavy and big, but you can’t substitute one for the other. We do need to sit down and look at what is the right way to do it. Are we making the batteries and transporting them, or are we transporting components? These are all discussions that for the next 20 years will keep on happening.
My biggest responsibility is to make sure the decision makers in R&D and manufacturing understand the impact of their decisions on supply chain both in terms of cost and environmental impact.
Ludwig: Do you think logistics will play that strategic role in making sourcing and production decisions for EV and battery?
Van der Merwe: Yes. I don’t think we [in logistics] are going to lead it at Toyota but we will be a key player across many areas.
One of the big benefits of bringing the three sides [inbound, finished vehicle and service parts] of the logistics business together is that it makes us a significant part of the organisation that the other parts need to sit up and listen to.
Ludwig: Do you see hydrogen fuel cells playing a role in the supply chain in the coming years?
Van der Merwe: It is a niche, but it is a niche that is growing quite fast. Toyota has already sold 10,000 units of the Mirai [a hydrogen fuel cell vehicle]. If we look at Tesla, we achieved our first 10,000 Mirais quicker than Tesla achieved its first 10,000 [electric] cars.
From a Toyota perspective, in the supply chain we don’t manufacture trucks. But we do believe that hydrogen is one of the pillars of a carbon-free environment. How it will play a part in supply chain I’m not yet sure, but will it play absolutely play a part.
Ludwig: How are you performing on inbound and outbound logistics when we consider some of disruptions currently affecting the automotive industry?
Van der Merwe: Because of the way we run our logistics on TPS principles, we can see problems very quickly. Yes, we have buffer stock in various places but what has saved us up until now has not been buffer stocks but the ability to react very quickly.
Secondly, Toyota treats it suppliers as partners. As part of TPS that means every one of our partners is supported by Toyota on a continuous basis, from a production perspective of how they run their plants and how to optimise them. Because of this relationship we have had visibility of our supply chain beyond most other suppliers but also visibility of where the problems are and how we can support those problems to be fixed. That is what has made the difference.
Ludwig: Our poll on whether OEMs should change JIT [see box out] showed that most of our audience believe that some adjustment to lean inventory will be necessary and that has been presented in some of the analysis here. How do you respond to that?
Van der Merwe: If I was voting I would have said we needed to change it too, but it would have been a different change to most other people. It is not that we have to change away from JIT but bring it up to date to the current scenario. We have to make sure our visibility is deeper beyond tier one and two [suppliers], but also make sure our support structure for our suppliers is far stronger. Those are the changes I would bring but it is not a change away from JIT it is a change to modernise and strengthen JIT.
Ludwig: How would you rate the measurability of the inventory right now? Can you do that in real time? Where are the gaps?
Van der Merwe: For inbound our visibility is where I would like it to be at 70%. But sometimes to have that visibility is hard work. We need to find ways to make that easier.
For outbound our visibility is very high. What we lack there is the link to upcoming problems and the impact that has on our visibility. We can see where every car is, but we struggle with seeing how problems affecting inbound supply impacts the outbound.
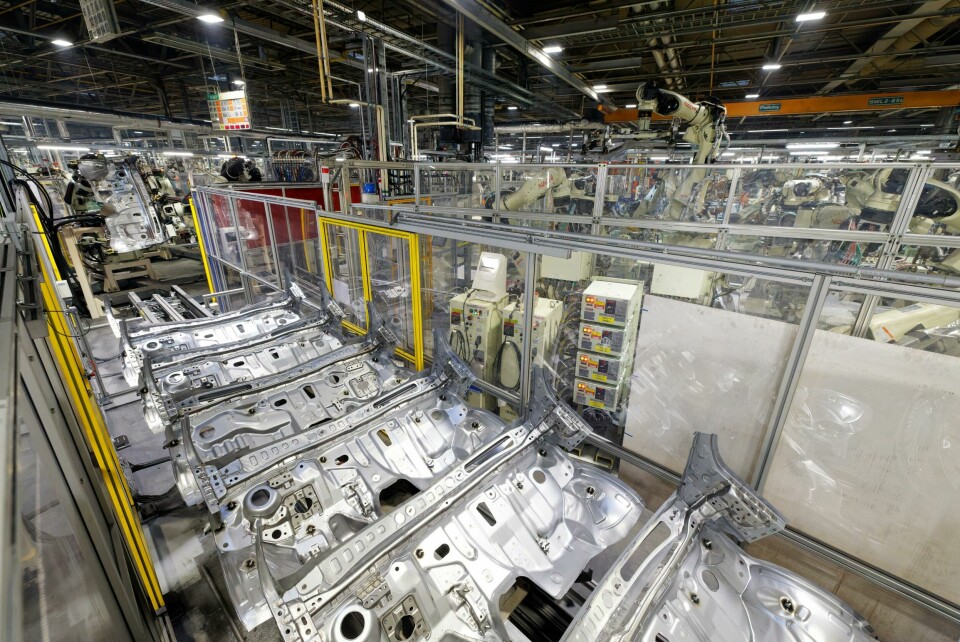
Ludwig: With the right IT and visibility will Toyota and the industry be able to come closer to the JIT vision?
Van der Merwe: Absolutely, it is one of things we need to do to modernise, to look at IT systems and ask how we use them. But again, there are two points. The IT system should be there to support our processes. We should not change our processes to match the IT system.
Secondly, when you are talking about IT systems for visualisation, stability is key. We shouldn’t be going for the latest technology – we should be one step behind the front to see it is proven. The last thing you want to do is put in a new system to give you total visibility but because it is unproven technology it gives you less visibility than you would have without an IT system. It is about how you choose and what the purpose of IT is.
Too many times people see IT systems as a solution to the problem. Rather, IT systems is the tool to reinforce the process.
Ludwig: What are digital tools and systems that Toyota is looking at now for its logistics?
Van der Merwe: We are looking at two big areas at the moment. The first is service parts and how do we put the right system in place. Starting everything from inbound planning to yard management, to stock management. We need to look at that whole system for the future.
Likewise, the whole backbone system that manages finished vehicles. On a continuous basis we should be looking at these opportunities. There is no one area that I would highlight. It is about taking a step forward and listening to our customers and interacting with them to see what we need.
Ludwig: Covid has led to a surge in ecommerce and in many cases expanded online sales channels for vehicles too, for example ‘click and collect’ or even home delivery. Are you seeing impacts to Toyota’s vehicle logistics as a result?
Van der Merwe: At Toyota we believe that ecommerce for vehicle sales is going to increase in the future. Will it be 100% of vehicle sales online by 2030 or 20%? I have no idea. But we do see it increasing.
But at Toyota we believe absolutely that our retailers are a key part of our future. When you are buying a product that for most people is half their annual income, it is not just a product you want to buy online, arrive at your house tomorrow morning with no experience and no explanation.
Also, the vehicle of the future is becoming more complicated. Vehicles will be either reserved online or bought online a lot more. There will be a level of home delivery, but we don’t see that home delivery necessarily being managed centrally [by Toyota]. We believe it will be managed through retailers so the person delivering the vehicle can do a handover and say, “thank you for buying a new car, let me sit down and do handover to show you the navigation and safety features, how do you change a tyre.”
Whatever you need to do the customer needs that knowledge and experience. A finished vehicle truck driver is not the person to do it. He transports every make of car so how can he really know a Toyota?
Ludwig: Has Covid permanently changed the way you operate in logistics? What lessons have been learned?
Van der Merwe: Covid has permanently changed the way we do things. Never has Toyota Motor Europe had such a turbulent year. We have had to design tools to allow us to stop doing things. Normally our focus is on designing tools to start doing things. That has had an impact.
Working from home has totally changed how we manage logistics. There were sceptics that didn’t believe we could have a 100% of support staff working from home but it has proven possible. On the other side, Covid fatigue has proven that people want to get back to the office. Working from home is going to be a strong part of our future but it won’t be 100%. We’ll get a hybrid scenario.
Decision making in Toyota has totally changed. We have always spoken about one team but Covid has created one team. Otherwise, we would not have survived. We have had cross-functional decision-making advance to such a level that none of us could have comprehended [previously]. We need to find a way to keep that.
I think for me I came into logistics as a novice and have had to learn very quickly how to manage crises and empower members to manage them too, as there were so many I could not manage them all. In many cases the first time I heard about a crisis is when my team told me they had resolved it. So, the changed management style is something I personally need to find a way to keep.
Ludwig: By 2025 what is the most important thing you hope to have achieved?
Van der Merwe: Toyota is now self-sustainable so if ever another Covid comes we will not be taken by surprise like we were this time.