The quest for greater unity
One of the main priorities for inbound supply chain managers from a packaging perspective is the proper management of returnable containers and packages so they are delivered as quickly, efficiently and economically as possible.
To achieve this, many North American OEMs have up to now insisted on their own forms of labelling, leaving tier suppliers with no choice but to manage a wide variety of labelling systems. As a result, an industry-wide labelling standard providing more consistent trackable labels on packages and a more universal standard for packaging itself are needed more than ever.
Bulk vs accuracyDepending on the containers they are used on, labels in North America are currently comprised of various materials, from paper to metal and plastic. Nearly every label used in the continent’s inbound automotive supply chain features barcodes and, increasingly, RFID inlays, according to Ed Nabrotzky, chief solutions officer of Omni-ID.
Barcode scanning is highly cost-effective and as pervasive within the North American automotive supply chain as elsewhere. Companies can easily order pre-printed barcode labels, sometimes finished with a protective top layer for more resilience, or just encode them themselves. RFID inlays are also becoming more affordable, says Nabrotzky.
“High volume logistics requires automated scanning for bulk, in comparison to manual barcode scanning for accuracy,” Nabrotzky says. “With RFID, you receive the automated scanning and a barcode, along with readable instruction, for a very low cost. RFID prices have come down as the technologies have vastly improved.”
However, there are some drawbacks to both barcode scanning and RFID, of which OEMs, packaging suppliers and distributors must be aware.
Bridget Grewal, director of packaging continuous improvement at Magna International, has had to utilise an advance shipping notice in addition to the traditional, globally used label recommended by the US Automotive Industry Action Group (AIAG), which in Magna’s case features a 2D barcode. This advanced shipping notice has been particularly helpful since the AIAG label does not notify the automotive supplier of when shipments are actually arriving, she points out.
While Grewal is investigating using RFID for empty containers, Magna has not yet used the technology, she says, as it can’t read containers that are lost – a common issue in the automotive supply chain.
“If RFID isn’t in a closed loop, it doesn’t work well,” Grewal confirms. “Not to mention, the AIAG label doesn’t have a database, nor does it provide any indication of how to optimise.”
She adds: “The real problem is that everybody is working independently. When you have a database, all of the data is collected in one place, but everybody is still trying to do it their own way – there isn’t a collaborative effort. This has potential to be overcome really soon, due to up-and-coming software.”
“The real problem is that everybody is working independently. When you have a database, all of the data is collected in one place, but everybody is still trying to do it their own way – there isn’t a collaborative effort. This has potential to be overcome really soon, due to up-and-coming software” - Bridget Grewal, Magna International
Apart from barcode scanning and RFID, kanban systems with cards (which require cardholders or clips) and placard or textured label area systems are two more primary methods for labelling. According to Andy Schumacher, vice-president of the packaging systems division at Schaefer Systems International, kanban systems are especially useful for reducing waste in inbound automotive supply chains, as they only reorder parts when they are truly needed.
Placard or textured label area systems, meanwhile, use removable and expandable labels for each shipment; no sticky residue is left behind when the labels are removed.
“Kanban and placard or textured label area systems are really the same, but rather than using cards, some companies use labels,” Schumacher states. “If an OEM uses labels, then cardholders and clips add zero value to their system. Instead, they should use placards or textured label areas to place the labels on the side of the containers. Regardless of which one is chosen, they’re both visual systems that will replenish inventory, reduce waste and improve the environment.”
Losses through labellingUsing such labels may ensure an adequate supply of containers, but there are other concerns. For example, conventional labels must be scanned by operators with barcode readers, which can be an unreliable process thanks to such factors as dirty labels, mixed boxes and high-volume operations.
Frequently, densely packed pallets or vehicles don’t allow a clear line of sight for scanning, resulting in inaccurate tracking of containers and owners or users who don’t know where their containers actually are. Most returnable container users report the loss of 20-33% of their stock annually, according to Nabrotzky.
“If containers aren’t available when shipments are necessary, duplicates may be ordered or fabricated, or temporary materials such as cardboard may be put into service with [the potential for] greater damage to the shipment or problematic handling at the end-use point,” he stresses.
Nabrotzky advises tier one suppliers to optimise their pool of containers via real-time tracking, preferably using cloud-hosted software that can predict how long containers will dwell in their cycles.
“Being predictive implies two things – you can analyse past traffic to set fixed expectations for workflows, or you can use an advanced rules engine to set parameters for current conditions, based on certain things happening,” he says. “Either is good, it just depends on business requirements.”
According to Grewal, improper tracking of containers can cost tier one suppliers millions of dollars, an issue that can be addressed with technology such as blockchain data collection, using a combination of tags, labels and software.
AutoSphere to the rescueTo help solve the issue of poor container management, a number of OEMs and tier suppliers have begun working with Surgere, using its cloud-based COS platform, to create a common RFID-based standard within the automotive industry. RFID, stresses Nabrotzky, continues to mature and is experiencing rapid growth, as it is small, reliable and has eliminated the barcode scanning requirement for line of sight.
“This is an absolutely huge step forward and is part of almost every strategic conversation we’re having in the industry,” Schumacher says. “The most common method of application is to inlay the RFID tag into the label and adhere a permanent label to the tote in two locations — the easiest and most cost-effective way to apply labels for batch-type orders.”
Surgere’s AutoSphere shared platform, announced in May 2018 at The Supply Chain Conference in Atlanta, will allow OEMs and their suppliers to use a common supply chain data network, so they can share information with each other and transport, manage and track containers and parts more effectively together. This should help address the automotive supply chain’s current estimated $2 billion annual cost from container and part losses.
Nabrotzky believes visual tags will also continue to become more popular, as they offer the same advantages as RFID, along with the ability to display other information and barcodes – just like paper has in the past.
“This means a hybrid deployment is possible where some elements of the supply chain can be invested in RFID infrastructure, while others just use manual recognition or barcode scans to gather shipment details,” he explains. “Therefore, real-time instruction tracking and changing can occur as conditions change within workflows.
“Imagine a customer changing a delivery address online and having the address automatically change on the label in real time. That’s the benefit of a dynamic e-paper or e-label,” he continues.
Grewal agrees that visual tags (which can be read anywhere in the world via GPS) are the most effective labels on the marketplace right now. Although GPS is expensive, its costs have begun to decline within the last couple years. Despite the diminishing costs of GPS, however, Grewal is also beginning to trial Bluetooth beacons that allow people with cellphones to read the tags free of hardware charges using an appropriate app.
“Within one to two minutes, my operators can tell where tools are by using the Bluetooth beacons,” she says. “The bars on the app become smaller or larger depending on how close the beacon is to the phone.”
Since the beacons depend on batteries that are likely to die within three to five years, Magna Powertrain currently uses RFID tags as a backup. While inexpensive to use, the beacons are expensive to purchase. Nonetheless, Grewal believes such beacons will become more affordable as volumes increase, the software becomes more compatible and standardisation occurs.
“The beacon has been redesigned to use an AAA battery,” she states. “Solar energy can’t be used because products are stored inside. [But] water or wind at warehouses and distribution centres could be used to create energy for the beacon in the future.”
Nabrotzky adds that energy harvesting and bi-stable materials (e-paper or plastic substrates) are making other exciting, new applications possible. “For example, sensing can now occur when temperatures change and labels can change colours to flag [this to] workers, all without additional power.”
Overcoming obstacles to standardisationNabrotzky believes the standardisation of containers, packaging and dunnage systems within North America’s automotive industry is “easy to say, hard to do.” Although everyone needs the same containers and uses the same types of parts flow, he says, they can’t seem to agree on a common approach, especially with regards to software workflows and data item records. Instead, they all have their particular ways of working and legacy systems in place.
[mpu_ad]“Surgere’s recent announcement [about its AutoSphere shared platform deployment], along with the involvement of the AIAG Committee, is a step in the right direction, though,” he says. “It promises to get the right players around the table to come to an agreement on data flow through the AIAG. Industry-wide standards would be a really effective way to drive change.”
Schumacher believes RFID tags can offer some assistance with pooling, but that the North American automotive industry is not entirely at ease with the concept of pooling, as individual companies want to stand out from each other and have different packaging to their competitors.
“Although a lot of different philosophies have prevented pooling in the past, the fact that most OEMs are working with one technology company [Surgere] is huge,” he states. “It really drives home the concept of an industry solution.”
Grewal stresses that differences in culture must not be overlooked either. She says she has noticed that truck drivers in Europe actively participate in the movement and tracking of returnable containers, requiring the number of empty containers placed on a truck to match the number of full ones removed. They also place a value on the containers — a practice she says truckers in North America simply haven’t implemented yet.
“European truck drivers feel honoured to have their positions,” she suggests. “It would be to our advantage to do what Europe has done. If we can get coordinated, it can happen.”
Getting involved earlyAs the North American automotive industry prepares for potential future standardisation, packaging engineers are also becoming involved to some degree.
According to Nabrotzky, it is important for engineers to be involved after initial product design has occurred but before any production specs have been established. Production specs are a critical element of part design and such designs can’t be finalised until packaging, and removal from packaging for assembly, have been completely determined.
“In many cases, handling and delivering a part is more expensive than the part itself,” Nabrotzky continues. “So it makes sense to consider incorporating sensors or transponders at the beginning of the design stage to ensure optimal savings and process efficiencies.”
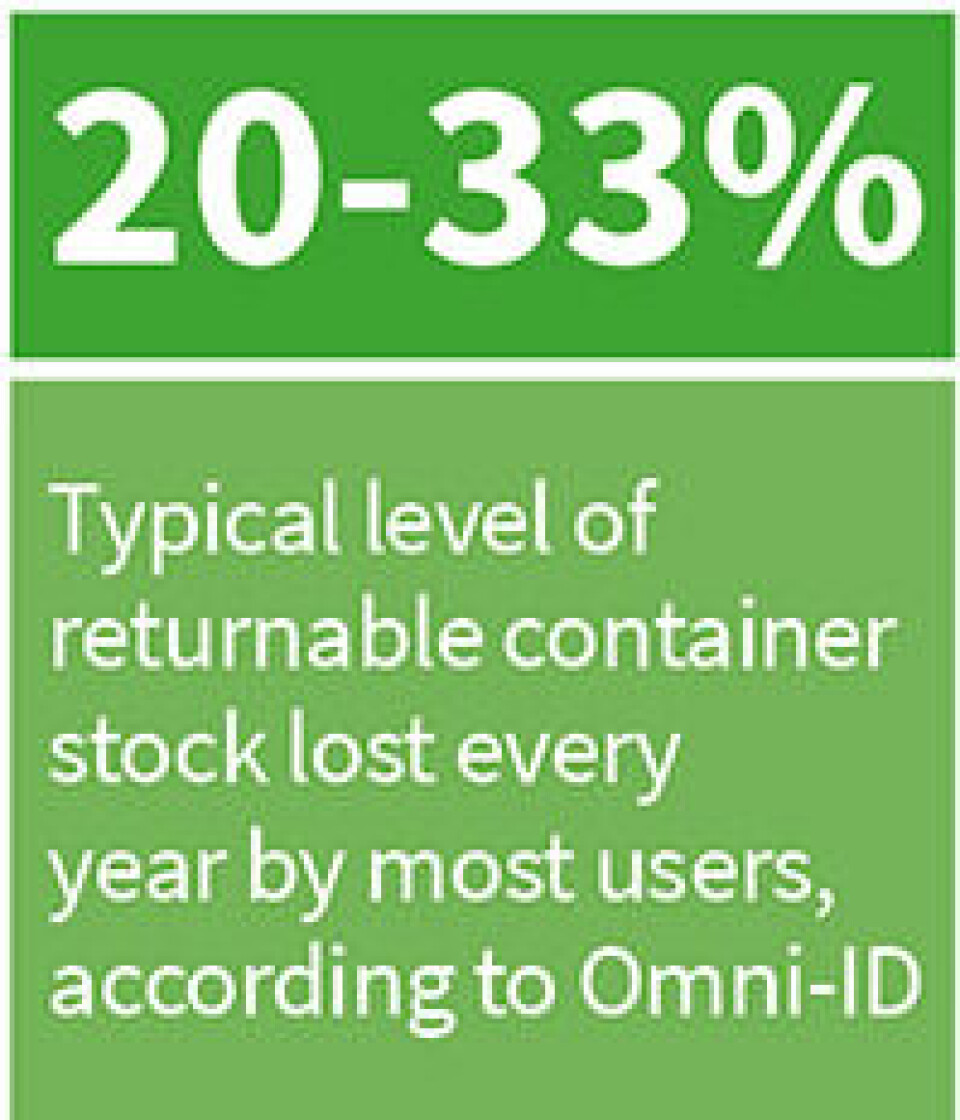
In addition, it is important to remember that the development of the returnable container system is entirely dependent on the complexity of the containers themselves. For instance, engineers are designing standard, expendable or returnable containers five months before programme launch; if the container is not standard, seven or more months are usually required, according to Grewal.
“Packaging engineers are often working on projects that are one to three years in advance of the standard operating procedure,” Schumacher adds. “Every project is different but, ultimately, most packaging engineers have almost no say in standardisation. The standards are being driven by the OEMs.”
Regardless of initiatives from organisations like Surgere, much more still needs to occur to ensure carmakers, packaging providers and suppliers can collaborate more effectively, improve standardisation for the inbound automotive supply chain and develop a more efficient, quality-conscious process for the timely inbound delivery of parts.
“Organisations like the AIAG are a platform to improve collaboration and parts delivery. However, the engagement has traditionally been very siloed,” Nabrotzky says. “OEMs usually meet with their own supply chain, while tier two players act as intermediaries or thought-leaders to bridge the gaps.”
This silo issue is due, at least to a degree, to software issues. Nabrotzky believes returnable totes’ common size standards have proved that collaboration is possible, but organisations don’t want to share any best practice on how they track their totes, in case they lose their competitive advantage.
“Everyone agrees on the data that needs to be there, but the important frontier that hasn’t been bridged yet is the common handling of the data for sharing,” he states.
This issue may ultimately be solved some day, thanks to the recent efforts of Surgere, as well as organisations such as the AIAG and AutoSphere.
“Everyone agrees on the data that needs to be there, but the important frontier that hasn’t been bridged yet is the common handling of the data for sharing” - Ed Nabrotzky, Omni-ID
“The biggest initiative for a more efficient process for inbound parts delivery is what Surgere is doing to help keep track of packaging through RFID technology,” Schumacher says. “This technology will also help greatly with increased visibility and inbound part identification.”
Future of trackable labellingAlthough Nabrotzky supports collaboration on labels, as well as the creation of proper trackable labelling on packaging, he believes labels may be needed less today than before.
“When people bought their routers for their home network, a label was placed on it with all of the passwords, and so forth. Now they buy equipment and it just works,” he says. “The vision of smart materials is that they should communicate with the systems around them without humans getting involved. It is automatic: the container negotiates its own path – no label or discretion is required.”
Nabrotzky suggests software and process standardisation levels are therefore now more pressing issues. Regardless of the technology being used to collect data, the interplay of data, along with its transfer between vendors, users and an increasing number of customers, will always need to be solved.
“Customers are demanding transparency in the supply chain as Amazon trains people to track everything and know when it will arrive,” Nabrotzky comments. “That expectation is driving change in non-traditional areas. The internet of things (IoT) will eventually get us to a fully transparent supply chain, as parts will be seen as they’re built and transported throughout their supply chain journey.”
Meanwhile, despite the present and future influence of software, Grewal suggests proper trackable labelling of packaging can be created with a very mature technology: that of the mobile phone.
“If you use signals that are coming from cellular towers for the labels, a signal will always be available. Cellular technology, combined with Bluetooth, will make tracking very cheap and easy (and the labels will be very cheap as well),” she states. “It should create standardisation. That’s where I would put my eggs – in that basket.”
Evolving standardsRegardless of the initiatives of organisations like Surgere and the AIAG, Nabrotzky is not overly optimistic about the potential for a more universal standard of packaging within the automotive industry. In fact, he doesn’t even believe there will be a set of standard sizes and characteristics, as the market is seeking more customisation right now, rather than less.
“Although there are common returnable packages in common sizes that people use, I don’t think there will ever be a one-size-fits-all,” he says. “However, we will get more standard systems and data handling, as the market drives this as an imperative.”
Grewal is more positive, stressing that sleeve packs – virtually collapsible, lightweight, tri-laminate plastic sleeves – are a new standard of returnable packaging that, in spite of their lack of exposure so far, will eventually become as common as pallet boxes. Due to stacking requirements, pallet boxes and sleeve packs will need to be compatible for optimal transport cube utilisation, she adds.
“Sleeve packs have a higher return ratio than pallet boxes,” she comments. “I believe they’ll be used more as time goes on.”
Development of a common packaging standard that everyone can use is being held back by a focus on capital outlay, suggests Schumacher.
“We have some customers looking at the total costs of the supply chain, but way too many customers are still looking at the upfront costs of the actual packaging,” he states. “Every item that is capitalised is always looked at upfront, and not enough people or companies look at the true total cost of solutions.”
Upfront cost analysis clearly makes sense, as 80% of returnable packaging costs are related to returning packaging through the supply chain. However, this perspective is preventing companies from achieving some very beneficial standardisation.
“I don’t see standardisation occurring for one commodity. The communication isn’t strong enough, and a standard hasn’t been identified yet,” Grewal says. “The automotive industry needs to collaborate on a standard, and then use that standard.”
Nabrotzky suggests such standardisation is an ongoing evolution but one that requires several steps, focused on physical packaging and data formats, among other factors, before the ultimate goal of shared data is achieved.
“Everyone in the supply chain agrees that we need to use technology to digitise data and obtain the item-level granularity necessary to see process improvements,” he says. “As technologies continue to improve and become more cost-effective, data will continue to enable good decision-making. And, in turn, automotive entrepreneurs will be able to create more solutions for standardisation issues well into the future.”
“We have some customers looking at the total costs of the supply chain, but way too many customers are still looking at the upfront costs of the actual packaging… Not enough people or companies look at the true total cost of solutions” - Andy Schumacher, Schaefer Systems International