Insourcing and localising supply chains help BMW stay flexible
Insourcing and localising are two of the ways that BMW Spartanburg is staying flexible and lean while growing, according to Oliver Bilstein, vice-president of logistics and production control, BMW Manufacturing.
Speaking at Automotive Logistics and Supply Chain Global 2023 in Dearborn, Bilstein said Spartanburg is insourcing some aspects of production and logistics to help stay lean as part of the OEM’s $1.7 billion investment in the plant.
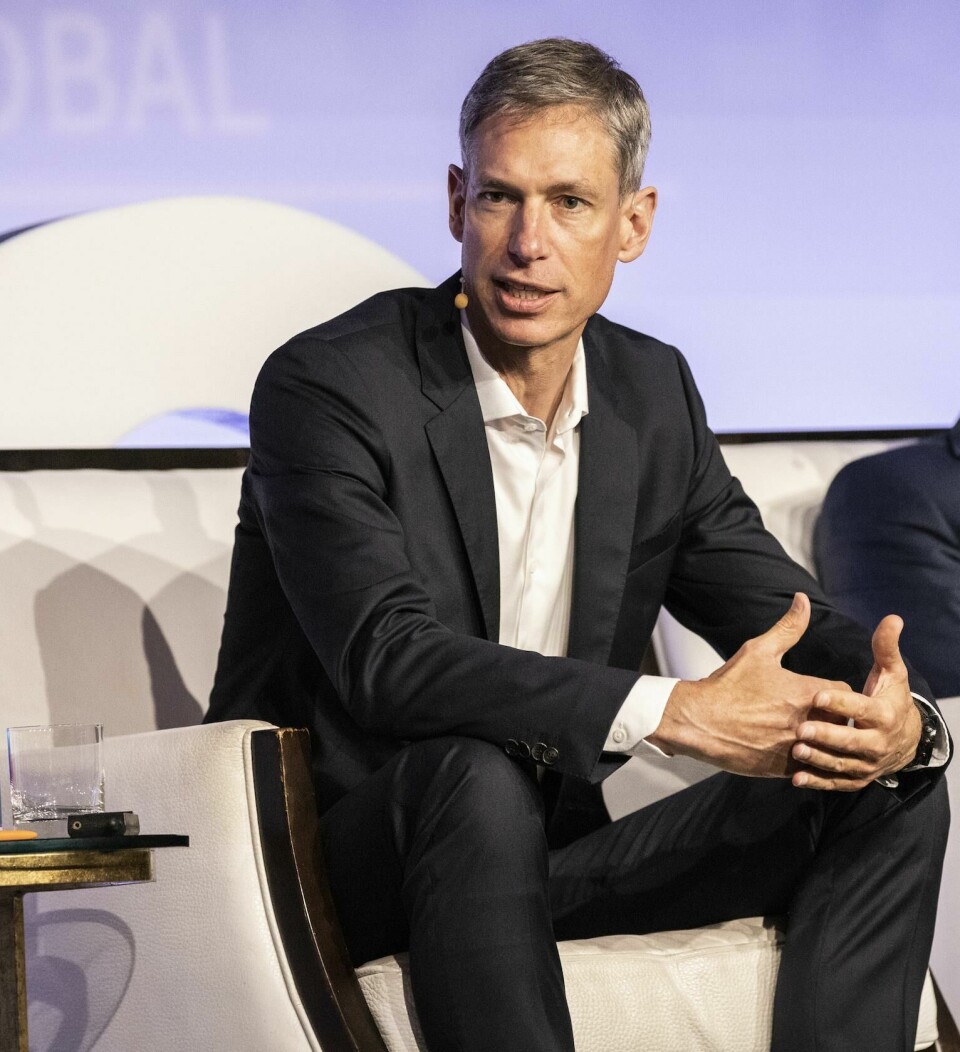
“Resilience is the big buzzword here, and we took some strategic decisions to keep flexible. We took the decision to insource, with our new press shop due to start production at the beginning of next year,” Bilstein said. “Last year, we started our new crossdock which we also insourced.”
In the carmaker’s transition to EVs, the Spartanburg plant also made the decision to have local supply chains where possible. “We have our cell supplier directly in South Carolina, about three hours away from our plant. These cells are transported to our battery assembly plant which is located 15 minutes away from our plant, it’s all very close together,” he said. “That provides a lot of flexibility in terms of demand and other challenges. These 15-minute distances allow us to avoid additional stock at our line, so we’re delivering just-in-sequence to the line.”
Bilstein previously spoke in detail to Automotive Logistics about how the Spartanburg plant is ‘performing while transforming’ in a special series.
He told delegates at ALSC Global 2023 that flexibility is the best route to stability as there is no way to “turn back the block to where everything was stable” before Covid.
“Together with our partners, we have to be flexible, to react to whatever kind of events are thrown at us,” he said. “We still keep our principle that we only fix our building sequence 10 days before we actually drop the car, which gives us a lot of time to make a plan B if we need to and sort issues, and then hopefully have the right parts and the right quantity at the time.”
Bilstein added that the biggest challenge in staying flexible and resilient is getting logistics providers and suppliers on board to help mitigate risk through new technologies such as AI. “They have to come to the party and match our investment,” he said. “We expect them to advance on three levels: firstly on lean, as we are looking for a more efficient and effective supply chain; secondly on green methods, as we all have to reduce our carbon footprint; and then on digitalisation, as we’re looking for more transparency and data to predict the future.”