Revving up supply chains: A digital leap for resilience and transparency
In the wake of recent global disruptions, Europe’s leading carmakers and tier-one suppliers are harnessing advanced digital technologies to fortify their supply chains. These innovations aim to increase transparency, cultivate trust and mitigate losses, ensuring a more secure and efficient future for the automotive industry. Simon Warburton reports
Just as the world heaves a sigh of relief and puts the darkness of the global pandemic behind it, along come a new set of crises to severely buffet OEMs and suppliers.
The semiconductor shortage exposed just-in-time risks, while a new set of geopolitical realities such as turmoil in the Middle East and its knock-on effects for shipping in the Red Sea, are compelling suppliers to urgently address digital transparency as a means not to completely eliminate risk, but try to iron out inevitable bumps in the road.
Secure data exchange
Mercedes-Benz – architect of its own operating system, MB.OS – says it is investing €60 billion ($65 billion) to 2026 in an “electric and software driven future.”
“We decided to make our critical infrastructure in-house to rapidly integrate and own the data,” confirms a spokesperson for Mercedes-Benz. “We partner where there is a customer benefit but not strategic loss for the company. Of course, we do this with experts in the software industry and offer a flexible interface to third-party content providers, so our customers receive content easily and intuitively.”
Mercedes-Benz says this is also true for rapidly developing and scaling technology, where the integration gives it the ability to adapt quickly to trends in the global tech economy. That enables it to increase speed of adoption and share costs.
Noting its vehicles generally contain several thousand parts and components, Mercedes-Benz, which is involved in the Cofinity-X partner network, says its supply chain comprises around 40,000 direct suppliers and multiple sub-suppliers.
Along with Mercedes-Benz, the Cofinity-X data exchange platform, which was set up in early 2023, involves carmakers BMW and Volkswagen along with tier one suppliers BASF, Henkel, SAP, Schaeffler, Siemens, T-Systems and ZF.
“Cofinity-X aims to operate an open marketplace for applications, and provide products and services to enable the efficient and secure exchange of data between all participants of the ecosystem, initially focusing on the European market,” says the Mercedes-Benz spokesperson.
The platform is strengthening endtoend data chains to trace material flows throughout the entire value chain.
“Through the Cofinity-X joint venture, we are bringing to life the Catena-X vision of an open ecosystem for secure and standardised data exchange along the entire value chain,” the spokesperson adds.
Catena-X defines a standard on data sovereignty enabling users to safeguard information and ensure it is used only in accordance with strictly defined rules.
“The basis for the operation will be the trusted Gaia-X [digital governance] principles, ensuring full data sovereignty for data sharing parties in an open, trusted, collaborative and secure environment,” adds Mercedes-Benz.
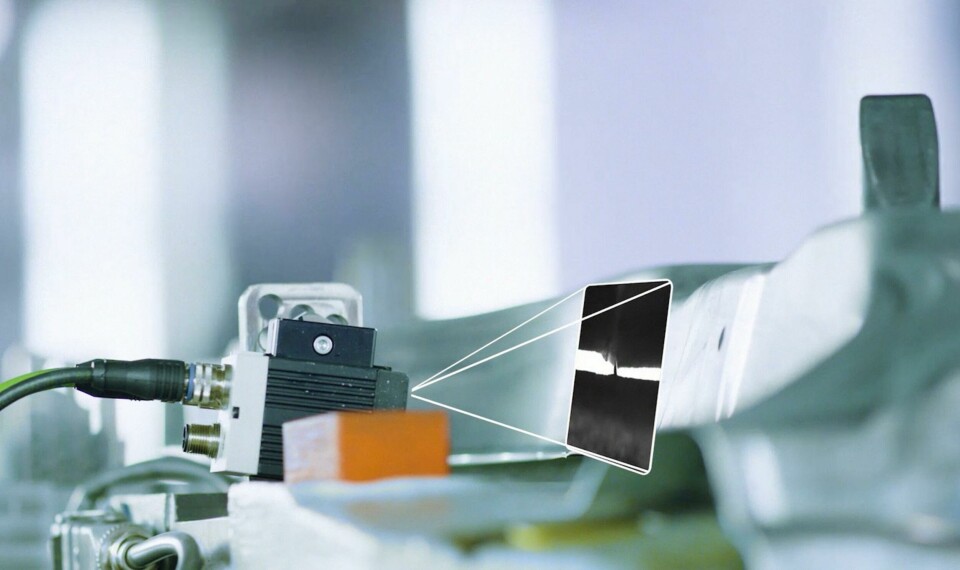
Solving problems at scale
BMW also points to Catena-X as a means of achieving a trusted supply chain that is interoperable and globally scalable. According to the carmaker, former initiatives lacked a way to solve concrete business problems, or did not have a clear separation of powers for all members. Interfaces were not identical and therefore not attractive or interoperable, so potential participants were concerned about data control. BMW started various initiatives to drive supply chain collaboration, but the focus now is to leverage all of them via Catena-X.
Among the first use cases to be rolled out by partners are traceability, quality, business partner management and product carbon exchange. BMW says it is focusing on business problems and regulatory hurdles first, and wants to allow open collaboration by building up multi-tier data chains with different partners along the automotive value chain.
“As one of 28 pioneer companies in the industry consortia, BMW strongly sees itself as a role model for radical collaboration,” says its vice-president of processes, digitalisation, governance, Oliver Ganser.
BMW insists Catena-X is not only about technology, but also a “collaborative and self-sovereign network approach, mutual values, policies and standards.”
Data sharing is mutually beneficial to all partners and something that is of great value to BMW’s suppliers, according to Ganser. For example, the carmaker shares live quality information and changes in demand, but also relevant sustainability information and tools for achieving end-to-end process excellence.
“Trust is a key component for the success of Catena-X,” says Ganser. “Be it trust in the vision of Catena-X, trusted identities, trust in the exchange of data or the solutions which process data. What sets Catena-X apart from others is the balanced distribution of power and clear benefits and business value for all participants in the ecosystem.”
Ganser believes that the automotive industry as a whole has to foster a better understanding of what data is sensitive, business critical or even decision-relevant.
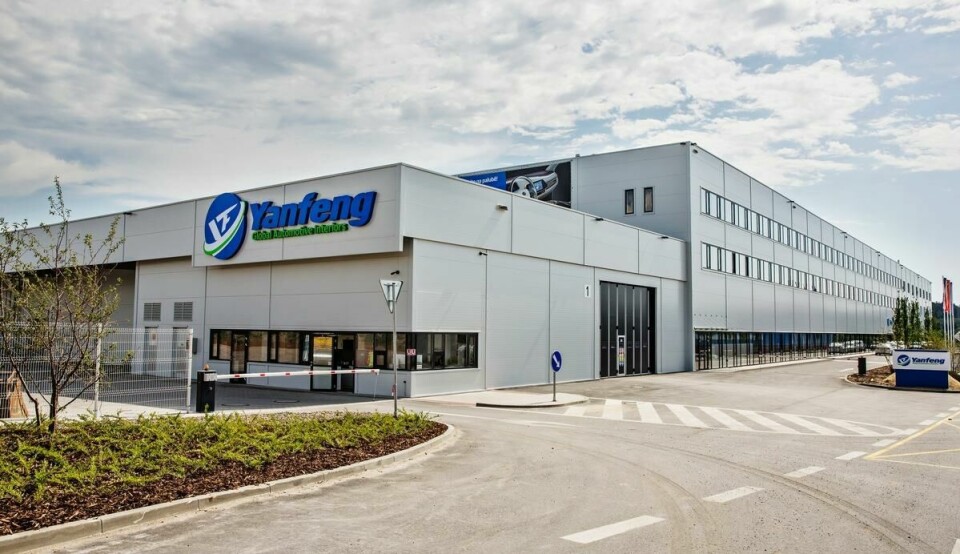
Transport utilisation at Yanfeng
For tier one components supplier Yanfeng, adopting AI technology is delivering remarkable efficiencies as it looks to sweat its transport logistics operation.
“We have successfully implemented a new logistics concept in most of our European plants, that is based on AI,” says its vice-president of global sustainability Gunnar Büchter, who is also responsible for procurement in Europe and North America. “Together with the start-up – s2 data & algorithms, from Graz, Austria – the planning of material requirements at our plants was optimised to achieve better utilisation of trucks and therefore reduce the total amount of transport.”
Büchter says that previously transport was booked weekly on fixed delivery days and often only two-thirds of the truck capacity was used. During a pilot project in 2022, material requirements planning in one of Yanfeng’s German plants was optimised to achieve better utilisation of transport equipment and cut the number and frequency of the trucks.
“The existing manual planning for the routes that usually are planned as a full truck or full container was replaced by a cloud-based software solution,” he continues. “The complexity of transport planning was defined to allow simulations and optimising of transport equipment by using mathematical algorithms.”
Büchter notes that because of optimised transport planning, transport utilisation has increased from an average of 70.9% to 92.2% of available load capacity.
He adds that in “a balancing act between transport and storage/capital tie-up costs,” weekly algorithmic planning means on average, only four instead of five transports are required per week.
The concept has now been transferred to all of Yanfeng’s other plants in Europe (more than 70% so far) and is being initiated in North America.
Common assessment standard
The supplier is also involved with the Responsible Supply Chain Initiative (RSCI), which allows it to identify, control and eliminate risks along its supply chain. The concept started in 2021 with VDA governance, as a coalition of companies and organisations collaborated on a common assessment standard.
To address trust challenges in responsible data sharing with customers and suppliers Yanfeng has set up what it says is a robust data-management system and data-governance policy and procedure.
Collaborative platforms play a vital role for Yanfeng in crisis management by facilitating real-time communication, coordination and sharing information.
“For this we already had integrated a tool using technology based on AI from start-up, Prewave,” says Büchter. “Their supply chain risk management and compliance platform offers a solution for managing supply chain risks, covering every phase of the risk lifecycle.”
The tool gathers all publicly available information from more than 250,000 direct and indirect sources in more than 50 languages from 150 countries.
“You get an alert if something happens. This enables us to proactively identify sustainability risks along our entire supply chain, such as pollution, corruption or human rights violations in real-time,” says Büchter.
Sustainability and cost
For US-based logistics software and transport management system (TMS) specialist, Agillence, hurdles to jump to achieve greater transparency include cost, resistance to change and digitalisation gaps between suppliers.
Sustainability and cost pressures are some of the major factors influencing Europe suppliers for adopting collaborative technology, as Agillence vice-president of customer strategy and solutions, Srini Paruchuri explains.
“Results are very clear during pandemic times for those who adopted collaborative technologies,” Paruchuri said. “They were able to contain costs and also maintain reasonable production levels without much disruption.”
Priorities for collaborating and investing in technology include digitalisation, supply chain visibility, sustainability and environmental compliance, regulatory compliance and resilience, as well as risk management, according to Paruchuri.
Agillence’s Automotive TMS offers detailed planning and visibility at the part level across multi-tier supplier networks. The technology’s centralised logistics data repository aids collaboration and the optimisation of the inbound network, factoring in routing, ordering, palletisation and details of truck stowage, says Paruchuri.
Trust in data sharing is key and Paruchuri highlights some of the main issues as privacy concerns, lack of data transparency, quality and reliability, as well as regulatory compliance. Data sovereignty can be protected with right data localisation, encryption and anonymisation, access control and auditing.
As for collaborative platforms, these enable real-time communication and co-ordination of response efforts in case of disruption such as Covid and natural disasters. “Uniform standards certainly help to have efficient interoperability, cooperation at global network level and reduced costs,” says Paruchuri.
When it comes to scaling up collaborative digital platforms for wider adoption, Parchuri notes that a number of factors have to be taken into consideration, including integration, interoperability and standards, as well as security and data privacy, and regulatory concerns. Adopters also have to think about costs vs benefits.
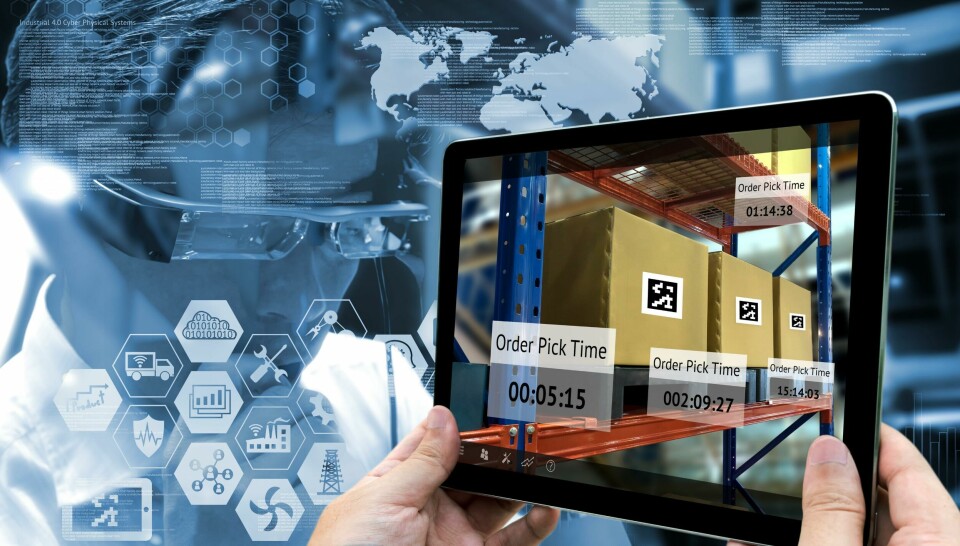
Digital transparency at ZF
End-to-end transparency using digital platforms is key to tier one supplier ZF, which cites the current crisis in the Red Sea as an example of how the impact of geopolitical events can be mitigated by such technology.
“The important point is to have transparency when you discuss internal risks,” says ZF’s head of corporate supply chain management, Andreas Koetz.
Are OEMs insisting suppliers apply digital transparency on both sides of the business relationship?
“Yes, of course,” says Koetz. “Not only the customer side, we have it on both sides. Our intention is to bring the connection to the supply base [with] demand for electronic data interchange (EDI).”
One of ZF’s key challenges is how to achieve digital transparency. For example, if companies have differing enterprise, resource and planning (ERP) systems, then there will be different data systems and data tools.
As an example, Koetz cites ZF’s acquisitions of US suppliers, TRW and Wabco, which had different kinds of base systems.
“So that means with ERP as a base, the data lakes are the second layer. The third layer is the apps, which look like apps or a Power BI,” says Koetz. Power BI is a Microsoft data visualisation tool. “In daily business, that was the biggest challenge, not only for us as a company, but for the whole industry to harmonise to get this data.”
ZF has installed a digital manufacturing platform for internal monitoring and for transfers of main data from its machining to a data lake to ensure preventative maintenance.
Koetz notes collaboration between customers is becoming more common, enabling inventory levels to be monitored and allowing for more transparency. The current quality of data connectivity is ten times better, according to Koetz.
The scaling up of digital platforms comes up against differing levels of standardisation, while ZF has added some analytical tools for forecasting systems and simulation of risk management.
The German supplier is also starting to use AI in logistics as Koetz notes: “We are learning with AI. Is it efficient and does it make sense, yes or no? We have to do that, project by project.”
Software for sustainability
German tier one supplier Bosch is also looking for greater supply chain transparency through the adoption of digital tools to improve parts delivery efficiency, avoid disruption and monitor sustainable and ethical sourcing.
“At Bosch, our supply chain consists of more than 30,000 direct suppliers and some hundreds of thousands of tier-n suppliers,” says Arne Flemming, head of supply chain management at Bosch Group. “Hence, to be efficient and effective, our transparency approaches are risk-based in combination with a high level of automation and digitisation.”
Supplier connections are supported by Bosch’s partner SupplyOn, which handles digital sub-supply chain queries and cross-functional supply chain mapping. That covers aspects such as human rights, environmental requirements and technical conditions with a high degree of accuracy.
Bosch has adopted a combination of established and new technologies, such as generative AI. At the same time, it increasingly connects its databases with partners such as the Carbon Disclosure Project (CDP) and external service providers to gain speed. Bosch also supports standardisation initiatives as comparability of certificates helps reduce the complexity of the task.
“With respect to supply chain resilience, ensuring deliveries to our customers is our main driver,” says Flemming. “Among other measures, Bosch has been managing and steering its transport worldwide since 2014 via a global transport management centre, including strategic route planning and daily optimisation, to maximise use of the transport means and transparency of the goods in transit.
“We’re targeting to steer 80% of all transports worldwide until 2027 via this transport management centre and boost truck utilisation for overland transports to 80%.”
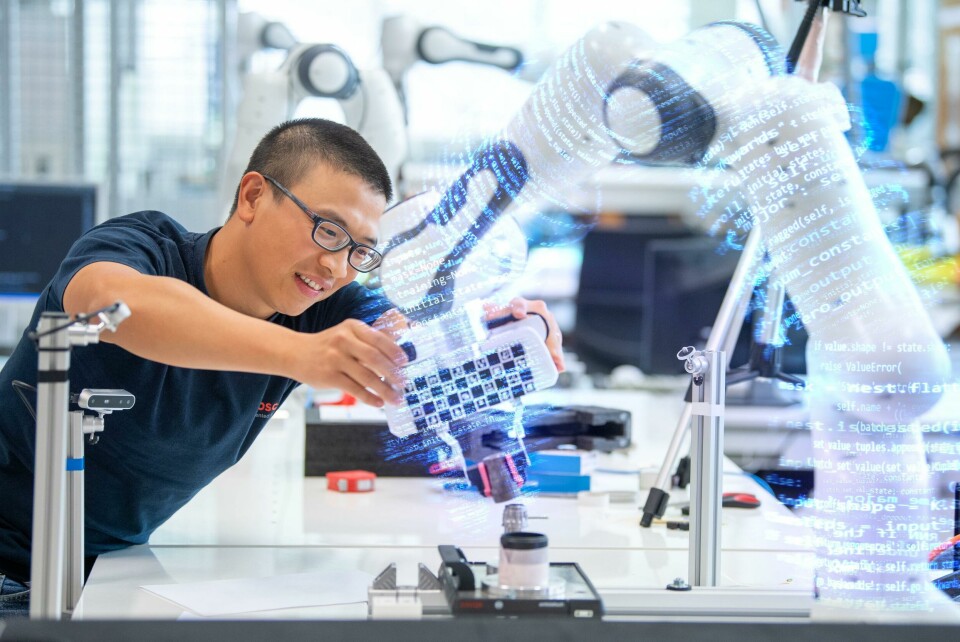
Elephant in the room
A few years ago, internet of things was all the rage. Then, along came blockchain with its transformative ability to deliver accurate tracking using electronic ledgers, allowing multiple parties to have visibility of shipping movements and finance.
Now the elephant in the room is AI, which could turn everything upside down. Risk can never be completely eliminated, of course. Predictive analytics can only go so far and there will always be unforeseen surprises. The Covid pandemic showed just how unprepared the world was for a totally leftfield threat, which turned the planet’s health systems and economies into a tailspin from which they are only now recovering.
The Covid years accelerated at a far greater pace the move to a holistic overview of inventory and its global movements using digital tools. AI has the potential to upend even new technologies, but those who adopt it have to be prepared that it could take them in very different directions.