Production & logistics part 3: Operations, packaging and IT
How have supply chain operations for logistics changed over the past 20 years?
How have supply chain operations for logistics changed over the past 20 years?
Twenty years ago, just-in-time and just-in-sequence manufacturing and logistics processes were already common practice in car factories. Those principles haven’t changed; however, executives agree that maintaining lean operations is made more difficult by higher part numbers, long-distance supply chains and the pressure to save space in plants for manufacturing rather than logistics tasks.
Alexander Koesling, head of supply chain management at Mercedes-Benz, points to an ongoing focus on transport mix and frequencies to make sure that logistics flows are stable and sustainable, including a mix of truckload and multimodal transport. Ford’s Dirk Willmann, director of MP&L for Europe, says that if transport plans do not change frequently to reflect changes in volume or engineering, logistics flows will quickly become imbalanced, while plants run out of room on the assembly line without changing material flow strategies.
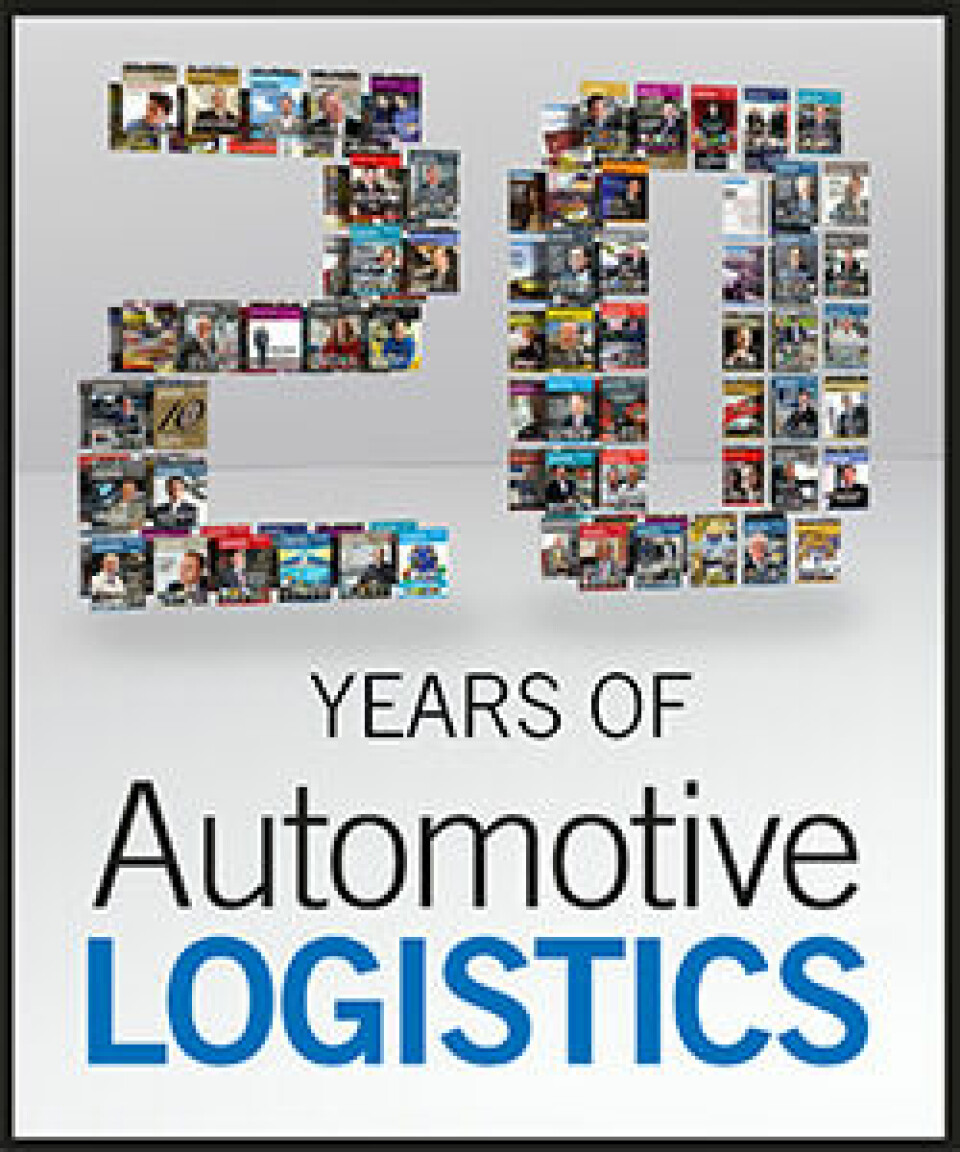
Click here to access more Automotive Logistics 20th anniversary features
At Honda North America, Dana McBrien, associate chief advisor, emphasises that different levels of manufacturing variability have required different strategies for managing parts from supplier locations to plants more carefully. For vehicles with low-to-medium variability in models, Honda “synchronises” parts from suppliers to the site, timing production and delivery in close sequence. But in cases where there are multiple models on the same line, more features and export destinations, the supply chain must be “synthesised”, with different parts consolidation centre and line-feed approaches. Magna Steyr’s director of purchasing and logistics, Michael Druml, meanwhile, points to long-distance, just-in-sequence deliveries as an important development in managing the lengthening supply chain with lean processes.
But while manufacturers have adjusted their logistics and material flow to handle part complexity, some acknowledge that it has not always been easy to determine the right balance between picking, parts supermarkets and kitting, all of which requires space and labour elsewhere in the plant. Thomas Zernechel, head of VW group logistics, emphasises, for example, that wherever there is sufficient space on assembly lines, Volkswagen Group is looking to use traditional kanban supply rather than relying too much on picking and kitting.
Have you seen a significant increase in returnable packaging compared to one-way material?
Executives have observed a rise in the use of returnable packaging, driven by increased standardisation of load carriers and more modular packaging concepts. In most cases, manufacturers use returnable equipment within regions, relying on disposable cardboard and dunnage for long-distance shipments to avoid empty return shipping. However, in some cases, including for Ford and Mercedes-Benz, companies are exploring the use of returnable bins as part of shared, rented pools, or some hybrid types of returnable and one-way packaging.
Standard, returnable containers have been around longer than 20 years, including small-load carriers (KLTs), large-load carriers (GLTs), Odette, Galia and foldable large containers (FLCs), among others. For some, including General Motors and Magna Steyr, using returnables has significantly increased. At Honda North America, McBrien says the growth of some part types, notably electronic parts, has required safer transport methods and moved towards returnable. Financial and environmental benefits are also a plus.
Koesling says Mercedes-Benz follows a standardised approach that keeps ergonomic, handling, financial and environmental benefits in mind, which has increased the number of parts moving in returnable packaging. Ford has also long had an approach of pooling KLTs across its plants and suppliers in Europe, according to Willmann.
Others, including a tier supplier in Germany, say that the past two decades have brought minimal change to an already high use of returnable packaging. At Kia, Kevin Kinsey, head of procurement, suggests that the change over the past 20 years has not been so much about more returnable or pooled equipment, but rather advances in customised returnable designs to allow for better protection and increase the amount of parts per pack – the so-called packaging ‘cube’.
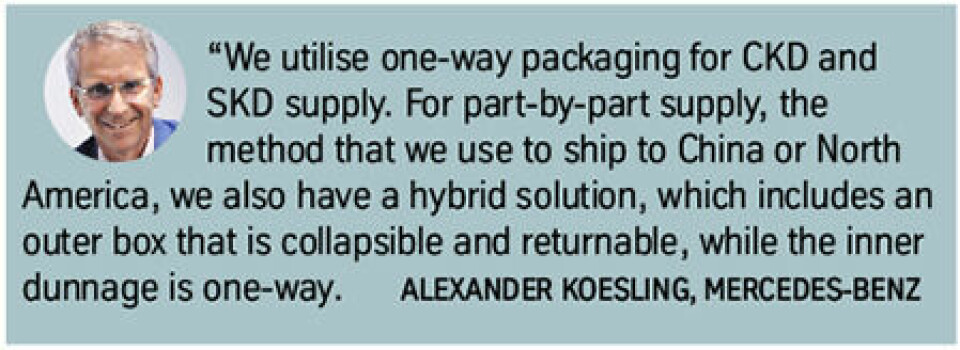
Volkswagen Group’s fleet of returnable containers across its brand plants in Europe has grown to around 21m units, while the carmaker is also exploring ways to increase returnable sharing in other regions, such as North America. However, Thomas Zernechel suggests that the bigger development for the group’s logistics has been an improved management system for controlling the fleet, including an algorithm-based software tool.
In China, Ma Zengrong, vice-chairman and head of the China Automotive Logistics Association (CALA) says that a lack of overall standardisation and relatively few environmental standards up to now have made returnable packaging less of an imperative for carmakers, although there is now growing interest in pooling equipment.
While most western carmakers use a reasonably high proportion of returnable equipment and packaging pools for regional supply chains, some are moving towards long-distance or even intercontinental solutions. Willmann says that Ford recently switched from disposable packaging to ISO bins for a number of intercontinental parts shipments, including between Spain and South Africa. Ford rents the equipment as part of a wider pool, and so avoids empty returns, while gaining better pack density and stacking.
Volkswagen Group, Mercedes-Benz and other brands that ship parts and semi- or complete-knockdown (SKD or CKD) kits overseas maintain that they primarily use disposable equipment, though there are opportunities to use returnables.
Have you seen a change in the amount of standardised versus bespoke packaging?
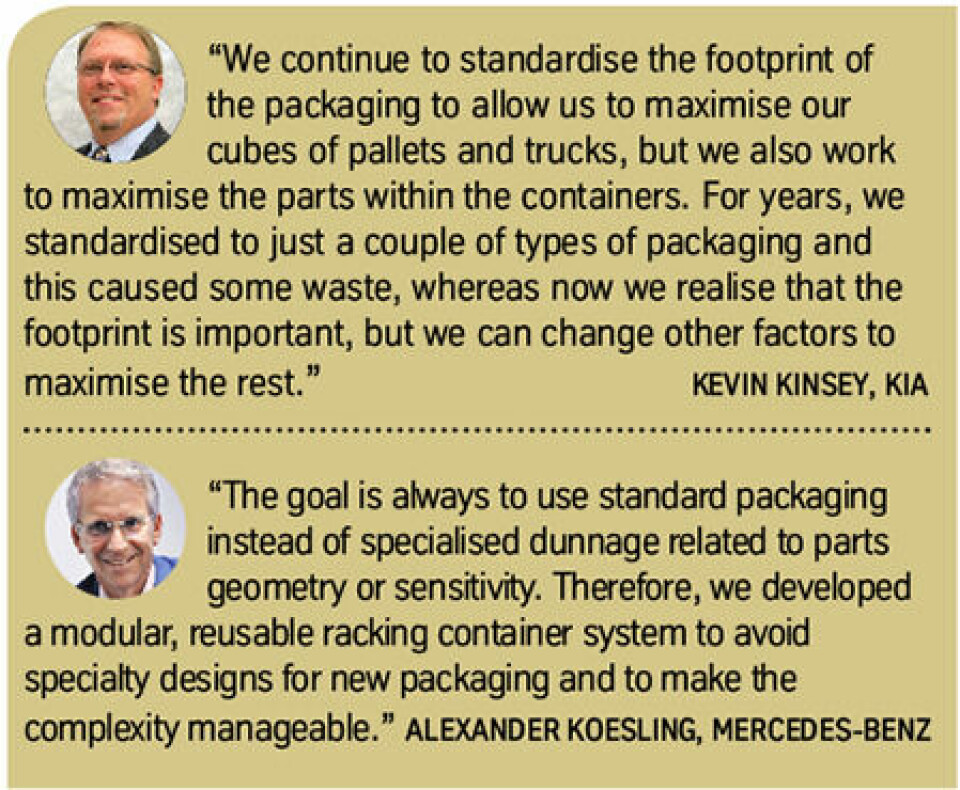
The proliferation of part numbers has also required better packaging equipment design to handle the variety. This requirement would seem to run counter to the push by most OEMs and tier suppliers to use more standardised equipment in their supply chains. However, modular designs have helped many in the sector to increase both standardisation and specialised packaging.
Michael Druml says that the industry has seen increases in small-lot containerisation – with more parts transferred into KLTs, often at parts receiving centres at plants – to improve line-side delivery. At the same time, the demand for specialised packaging has grown with the increase in part varieties. At Honda, Dana McBrien points to many efforts to increase the use of standard packs, but says the growth in parts has required more unique packs or internal dunnage.
Thomas Zernechel says that up to 2010, Volkswagen Group saw a large increase in bespoke packaging. Since then, packaging planners in group logistics have helped to reduce specialised equipment, which today makes up around 11% across its European packaging fleet. At Mercedes-Benz, Koesling calls the cooperation between the supply chain team and R&D to design packaging “indispensable”, with focus both on increasing fill levels of racks and standardisation.
Such cooperation has helped to increase the use of modular packaging design at carmakers. At Kia, Kevin Kinsey says the focus has now switched from overall standardisation to having set container base sizes, with bespoke design within to fit in more parts.
What changes do you foresee for packaging?

Executives see opportunities for automotive packaging in continued standardisation and improved design, as well as better visibility. As Kevin Kinsey puts it, most of the potential improvements already exist in one form or another today, whether in RFID tagging to improve real-time tracking, or in environmentally friendly design and materials.
Zernechel says that Volkswagen is looking to digitalisation to improve container tracking; Audi has worked with group logistics to tag and track its containers for its plant in San José Chiapa, Mexico. At Honda, McBrien envisions improved tracking and data analytics to improve both the positioning of packaging in pools and container design. Other carmakers and tier suppliers are looking to connectivity to improve tracking and monitoring, including sensors that show locations and also give information on temperature, humidity and potential damage. BMW’s ‘connected supply chain’ initiative, for example, envisions using ‘smart packaging’ to capture significant data throughout the logistics chain.
Other executives think the industry has further to go in improving standard designs and pack density across packaging equipment. McBrien at Honda thinks this will be important to maintain model-to-model interchangeability across plants and life cycles. Mercedes-Benz’s Koesling is also aiming for higher standardisation to avoid expensive single-use designs, while he anticipates improved pack density could have a big influence
on cost, especially for long-distance transport.
One large German tier supplier also points to the potential of decreasing the “empty space” inherent in some packaging designs by applying more modular, reusable inlets, as well as taking advantage of smarter stacking methods.
More sustainable packaging and materials will be important in terms of weights and increasing the life of packaging. Volkswagen is already working with other manufacturers and the VDA (German Automotive Association) on concepts for more bio-based materials in packaging design, which will weigh less and have higher pack capacity.
Thomas Zernechel also thinks that the use of virtual reality and animations will help manufacturers to work more closely with parts engineering and R&D to create better designs and test new materials.
In China, Ma Zengrong anticipates considerable gains in packaging standardisation and returnables from their relatively low levels in the country. He also sees more potential in shared systems of pooled packaging across the industry.
Though packaging pooling is far from new in western markets, Dirk Willmann at Ford also sees potential to go further, from sharing KLTs to extending pooling and renting to ISO bins, FLCs or Odette containers, with specialist third parties managing the equipment across different companies and industries.
What have been the biggest changes in the way your company uses IT and software over the past 20 years?
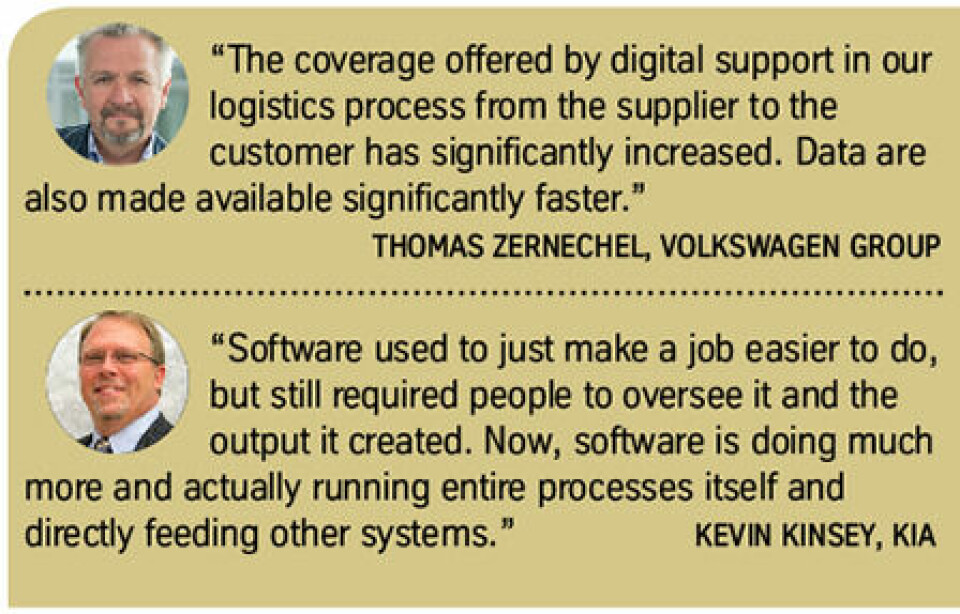
Clearly advances in internet connectivity, electronic data exchange and faster computer processing power have helped manufacturers and logistics providers use IT and software systems to improve speed of planning, communication and visibility. In some cases, systems have been able to replace human involvement almost entirely, such as in order planning and route optimisation. Koesling says that automatic distribution planning and control were not possible with the IT systems of 20 years ago at Mercedes-Benz, while today more data can be processed faster.
Michael Druml highlights the increase in data transmission across the supply chain from suppliers to the production line as an important leap in transparency. Dirk Willmann adds that Ford and its LLPs have greatly improved visibility, including a new system that combines telematics tracking with information from Ford’s enterprise planning systems to show transport progress and the impact of disruption in close to real time.
The use of big data and analytics is also cited by numerous executives as an area of increasing importance. Audi, for example, has recently applied a data analytics approach for its plant logistics in Neckarsulm so that it can predict which vehicles will be produced and released to its vehicle yard and give trucking carriers advance notice, rather than only notifying them once a car is built and quality checked. The project has included using operational and historical data to predict how production might change or be affected in the supply chain, says Johannes Marschall.
Nevertheless, according to the executive at a major premium carmaker, gathering such data and processing it into meaningful output remains at the very early stages for it and most manufacturers.
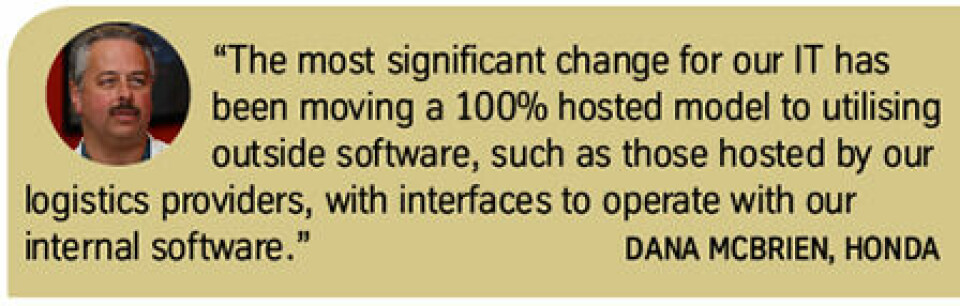
With rapid IT and software developments, many manufacturers have also faced the challenge of integrating new systems into their own enterprise systems, some of which can be decades old.
The need for systems to be open and adaptable has become much more important. Several executives highlight the importance of open interfaces today that allow production, shipping, supplier and other data to move between different systems and companies, often via the cloud. As the executive of one premium carmaker puts it, many companies had previously been hiding and coveting their data, whereas now they need to “open the black box”.
Executives agree that logistics departments should play a primary role in developing or acquiring the necessary IT to support operations, and to help streamline communication. Michael Druml says that logistics organisations must also increasingly work to bring together various systems through a single interface.
For Volkswagen Group, Zernechel says that the trend is for the company to host its main enterprise data in its own system “backbone”, but for smaller applications to be in the cloud, including micro-services tailored to specific areas. An example is its cloud-based interface, Discovery, which will be used by all suppliers and logistics providers to share and track shipping information across multiple systems.
What will be the biggest impacts on your logistics from IT and software applications in the future?
Executives see big data and predictive analytics playing a much bigger role in their supply chain and logistics. By better using network and market data, companies hope to anticipate demand, changes and disruptions, facilitating improvements in forecasting, logistics engineering, sequencing of part flows in plants and even customs clearance.
At Magna, Michael Druml expects big data processes will help all supply chain stakeholders make better decisions. Zernechel points to the use of “risks maps” that will provide more reliable forecasts across networks and help drive investment decisions. At Mercedes-Benz, Alexander Koesling thinks big data technologies will help improve simulations and forecasting, including digital planning of logistics, packaging and material flow. Connectivity through the ‘internet of things’, with real-time tracking of goods, will form the basis of data collection for predictive analytics, he adds.
Willmann says that Ford already has a project underway in which it is putting together its Global Data Insights and Analytics (GDIA) team with members of operations to explore how to use data most effectively. At Volkswagen, Zernechel anticipates entire “logistics assistance systems” that could fully automate parts replenishment or make decisions automatically in the event of transport bottlenecks.
Have you seen rises in logistics automation in your supply chain? Where do you expect this to increase in future?

Although automotive assembly is highly automated, many logistics processes have been slower to go to robots. Up to now, transport and loading have been mostly manual, as have parts handling operations like picking, kitting and sequencing. Both GM’s Pezzo and Kia’s Kinsey say they have seen less logistics automation than they would have expected by now. At Honda, Dana McBrien says the carmaker’s logistics automation has not been significant aside from a few recent materials handling applications. In warehouse and sorting centres, many companies also prefer the flexibility of human labour over installing machines, especially in dealing with seasonal peaks and troughs.
Nevertheless, the last 20 years have led to more automation of some processes, especially in-plant and materials handling, such as inventory retrieval systems and AGVs, as well as to worker-assisted systems for picking guidance, such as pick-by-light or pick-by-voice.
Across various Volkswagen brands, driverless transport systems, automated unloading of goods and self-organising picking lists are now standard. Audi, for example, has been increasing its use of ‘smart’ AGVs with cameras and sensors to navigate rather than following induction loops. The premium brand has also introduced AGVs at its vehicle garage in Ingolstadt to assist in moving and loading finished vehicles.

Others point to the use of automated small part container systems as a significant step in parts handling automation, in which parts that arrive in bulk or larger containers are automatically resorted into smaller containers for line-side delivery. Mercedes-Benz, for example, has recently combined both driverless transport and small-load carrier automation in an ongoing pilot, called FLOW (flexible logistics optimised warehouse), which could become part of series production of the new S-Class in Sindelfingen, Germany. According to Koesling, this driverless picking system provides the supply of materials to the production line as and when they are needed. Small-load carriers are transported autonomously around the shop floor via a guidance system with magnets embedded in the hall floor, that can be automatically allocated to any storage shelf.

While Ford also uses AGVs, Willmann notes that most logistics automation remains piecemeal and relatively disconnected. He envisions significant progress once a more integrated automation system is in place, including smart packaging in transport, as well as cooperative robots working with humans for kitting and line-side delivery. Both he and Thomas Zernechel think the eventual automation of parts picking will be important to reducing costs and errors.
Executives also expect increased use of automated storage and retrieval, drones for inventory counting and RFID to reduce errors across material flows. In the more distant future, the automation of trucks and vehicle themselves could further transform the supply chain.
This article is one of a series of pieces celebrating Automotive Logistics’ 20th anniversary issue that together take an extended look at the way top executives feel automotive production and logistics have changed in the last two decades – and where they see them heading in the future.
The full series includes:
Production & logistics part 1: Where are we now?
Production & logistics part 2: Questioning the future
Production & logistics part 3: Operations, packaging and IT
Production & logistics part 4: Logistics organisations and skills