VW Group looks for partnerships to build a resilient North American supply chain
As it expands operations in North America, Volkswagen Group is intensifying its collaboration strategy, both internally between departments and with its logistics providers. By doing so it is finding greater sustainable intermodal efficiencies on the inbound delivery of parts.
As was made clear by Christoph Hartmann, head of digitalisation for material logistics at VW Group Logistics at this week’s Automotive Logistics and Supply Chain Mexico conference, the company is likely to be reaching out to logistics partners in 2024 for support in establishing a common less-than-truckload (LTL) network in the US and Mexico.
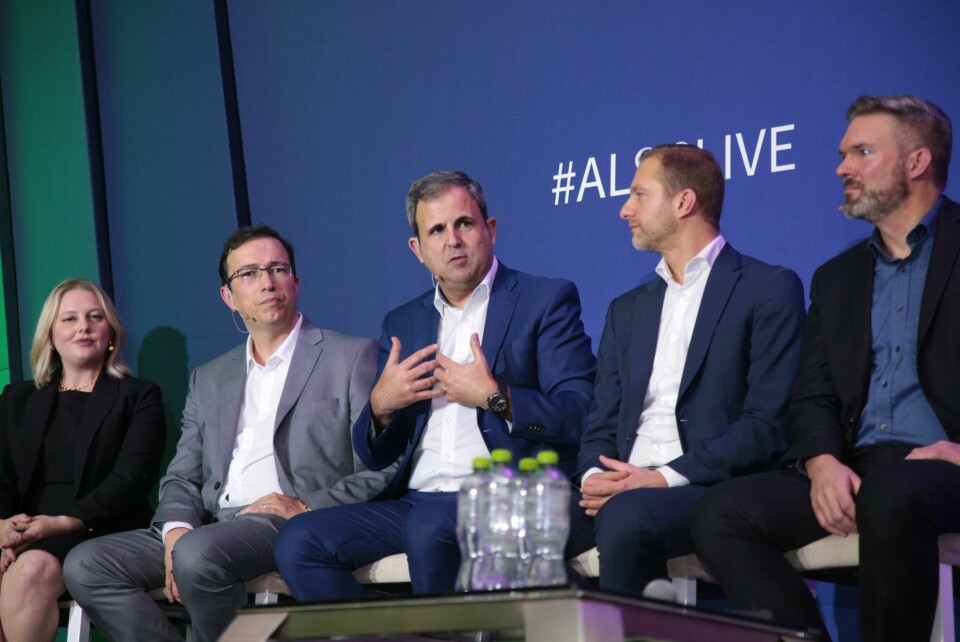
The crises that have disrupted the supply chain network over the last few years and the normalisation of volatility, uncertainty, complexity and ambiguity (VUCA) has taught VW Group some valuable lessons. There were new demands made of supply chain planners to steer through the crises and overcome global obstructions in getting material where it needed to be on time. Collaborating more closely with logistics partners and using digital tools to gain greater transparency along the inbound supply chain and overcome barriers is a result that VW Group has put at the centre of its global logistics strategy for the future.
“We did our homework on transparency [through] digitalisation and are way better in terms of making online data available,” said Hartmann.
In Europe the company is using digital twin technology for visibility on truck freight, to get more accurate information of where loaded trucks are, who is driving them and what they have been loaded with, an approach that is helping the VW Group better manage any disruption en route, according to Hartmann.
Expansion in North America
This is now a strategy the carmaker is bringing to North America in response to its expanding footprint in the region and it is looking for greater collaboration to achieve it.
“Collaboration is the point in North America,” said Hartmann. “This year we became aware of the rising footprint of our operations in the region and the new operations that are upcoming. It’s a new approach.”
Hartmann’s colleagues at this year’s ALSC Mexico conference outlined some of the expansion that has been, and is, taking place in North America.
Paulo Monteiro, head of logistics for Volkswagen Group of America’s operations at the Chattanooga plant in the US state of Tennessee pointed to the extension of the plant to accommodate additional battery production as the carmaker vertically integrates its supply chain for battery EV (BEV) production. Learning from the disruption of recent years, Monteiro oversees 120 logistics specialists at the plant and said the team is resilient and able to face the challenges that everyone in the automotive industry has become familiar with. Monteiro also oversees 1,000 employees working for VW of America’s third-party logistics providers (3PLs) indicating the closer links the carmaker is achieving.
VW Group of America is moving a significant amount of tonnage, according to Monteiro, equal to about 7.3m cu.m on a yearly basis, with annual overseas parts deliveries equal to about 3,000 sea containers [TEUs and FEUs]. It also moves 2.2m large load carriers (or GLTs) and 3.5m small load carriers (KLTs) which requires close scrutiny.
“It just needs one KLT not to be delivered at the correct time and we could have a stoppage,” he said. “Our business is very critical to ensure that the production has a proper flow.”
Battery cell supply from Canada
The expansion in North America also includes the building of a gigafactory in St Thomas, Canada, under VW Group’s integrated PowerCo battery division. When the St Thomas gigafactory goes into full ramp-up in 2027 the company has calculated that 200 trucks, containers or railcars will be delivering material into the plant per day. That material will be coming from North America and overseas. According to Sören Stade, head of logistics, Project St. Thomas, at PowerCo, the company hopes to persuade suppliers to move to the supplier park; also being developed next to the gigafactory.
Up to 150 outbound rail cars or trucks per day will be taking battery cells out, mainly to Chattanooga, while recycling materials will be moved mainly by truck from 2027.
Currently the VW Group gets 95% of the battery cells it needs for BEV production from Asia.
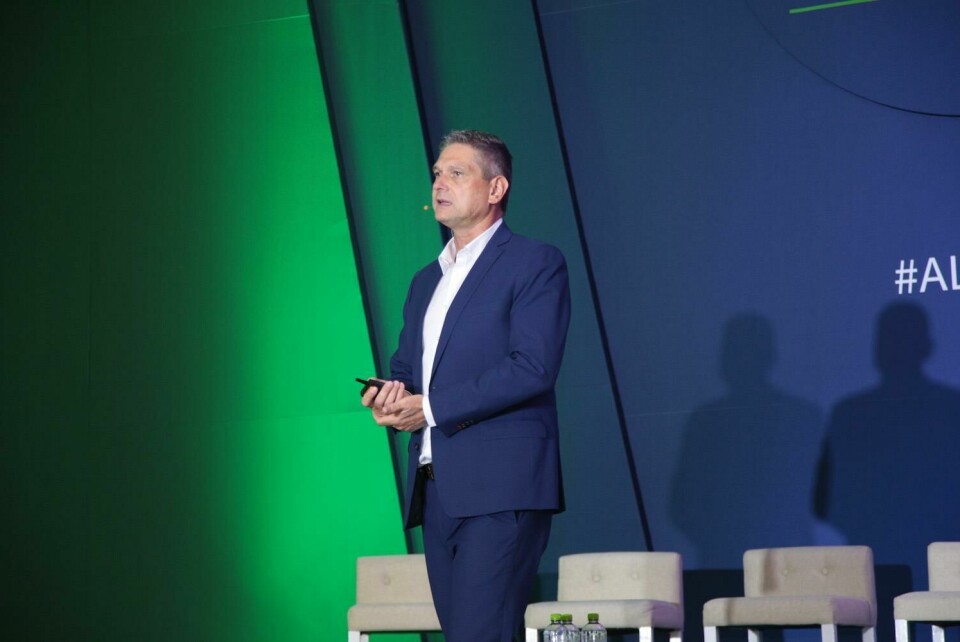
“We really need to take ownership of this technology in our industry and this is what VW decided strategically, to go into vertical integration of the supply chain,” explained Stade. “By doing this we will also bring down the cost of the battery cells for our vehicles significantly.”
That is important given around 40% of the total value of the VW Group’s BEVs is the battery system. “If we really want to be in charge of the value chain then we need to be in charge of battery cell production,” said Stade.
That decision to vertically integrate has widened VW Group’s supply chain activity.
“We are integrating vertically into the supply chain, not only producing the cells but we also look deep into the supply chain, up to securing output from certain mines for the active material for those cells.”
Stade said that battery cell production will be a highly automated process and will depend on AGVs, automated storage and retrieval systems, and automated conveyor systems. “We have to standardise facilities and rely on digitalisation for visibility in the supply chain,” said Stade.
Inbound to Mexico
VW is also well established in Mexico, with assembly and component production in Puebla and an engine plant in Silao. Annual vehicle production in Mexico, which stands at 400,000 units, is heavily dependent on inbound parts from North America, equal to 11.2m cu.m annually, with 300,000 cu.m coming from overseas.
Peter Koltai, senior director production control, logistics, Volkswagen de México, said between the production locations in Puebla and Silao the carmaker was annually handling more than 4m GLTs and 6m KLTs.
The VW Group is also well established in Mexico for the production of commercial vehicles with Volkswagen Truck and Bus and Navistar part of the group. Volkswagen Truck and Bus makes 3,800 units a year, which requires 140,000 cu.m of inbound material delivered on 2,000 journeys in 1,000 containers. More than 90% of goods come from outisde of the country, mainly Brazil, while 10% comes from the NA region, mainly Mexico.
”One of our future challenges is going to be to select and develop suppliers that are able to produce all parts locally,” said Halley Vieira, plant manager in the Production and Logistics department at the division.
Navistar, meanwhile, produces approximately 90,000 vehicles across its facilities and another 12,000 engines. ”To produce these we are shipping 12.3m cu.m of material. We have another 130,000 cu.m coming from the rest of the world and that is approximately 1,400 containers,” said Haley Wilson, logistics director at Navistar.
Future network planning
The expansion of this activity in the US, Mexico and Canada, and the lessons learned about managing disruption since the Covid pandemic, including the greater reliance on digital tools and closer collaboration with logistics partners, will now inform VW Group’s network planning in the region.
With regard to its plans for an inbound LTL network, VW Group Logistics has gathered experts from its plants and given them the freedom to think across brand silos in a shared approach to a tangible problem and gain some quick and useful results.
”We put all our supplier and production locations on the table and took down all the routes and transport lines between them and asked what we could come up with. The team worked hard to find ideas, also surprising each other about how we looked at transport and logistics,” said Hartmann.
The company is now looking at an intermodal project that will see greater use of rail to overcome a shortage of truck capacity, caused in part by the driver shortage in the US. The carmaker is looking at a door-to-door service that will move 53 foot containers that can swap between road and rail.
”This is something that to a vast amount could help overcome the crisis affecting trucks and driver availability. That is also sustainable even when using diesel.”
Another important area that VW Group is targeting is container pooling both in terms of replacing cardboard packaging with returnable containers and establishing shared networks to return the empty returnables.
“Lots of this is still in discussion,” said Hartmann, addressing the logistics and technology providers at ALSC Mexico, “but 2024 might be the point where we reach out to the market and hopefully you are there and interested in talking to us.”