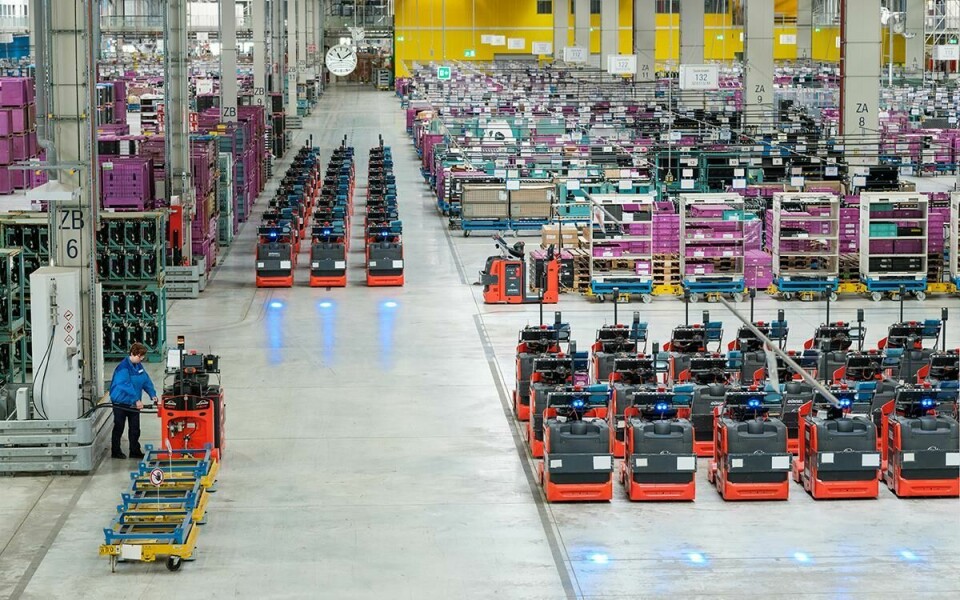
A sustainable supply chain inbound and out at BMW
BMW Group is aiming to make the logistics supporting the production and delivery of its vehicles emission-free and has set up a Green Transport Logistics project team. Maike Rotmann, head of distribution systems and sustainability, and Wolfgang Rudorfer, head of transport planning and steering, explain more
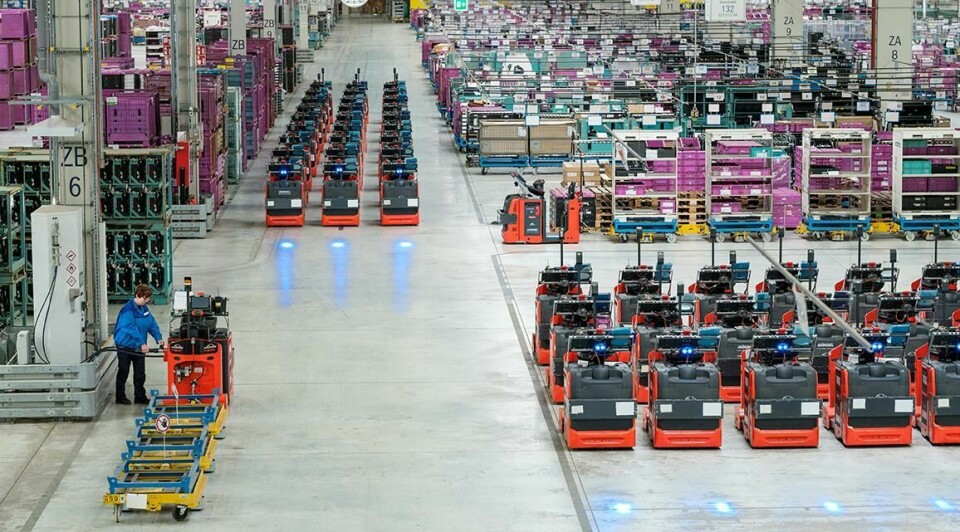
Two years ago, BMW announced aims to reduce carbon emissions across the lifecycle of its vehicles by at least 40% by 2030 compared to 2019. Those aims include cutting emissions from vehicles themselves and by the end of this decade it intends that at least half of its global sales will be fully electric, with 2m electric vehicles (EVs) on the road by 2025.
It goals also include removing emissions from the manufacturing process and the company already reports being carbon neutral at all of its manufacturing locations.
In addition, BMW is also cutting carbon from the logistics used to supply the parts to those plants and from the delivery process used to get the assembled vehicles to the customer.
More specifically, BMW has plans to reduce carbon emissions within supply chain by 20% by 2030. That means, among other things, a much closer collaboration with logistics and transport providers, a focus on digital tools for data gathering on carbon emissions in the supply chain and a much greater emphasis on sustainability in the purchasing of services.
Automotive Logistics spoke to Maike Rotmann, head of distribution systems and sustainability, and Wolfgang Rudorfer, head of transport planning and steering, about the strategies being put in place as part of its Green Transport Logistics project to make BMW’s inbound and outbound logistics an example of sustainability for the automotive industry.
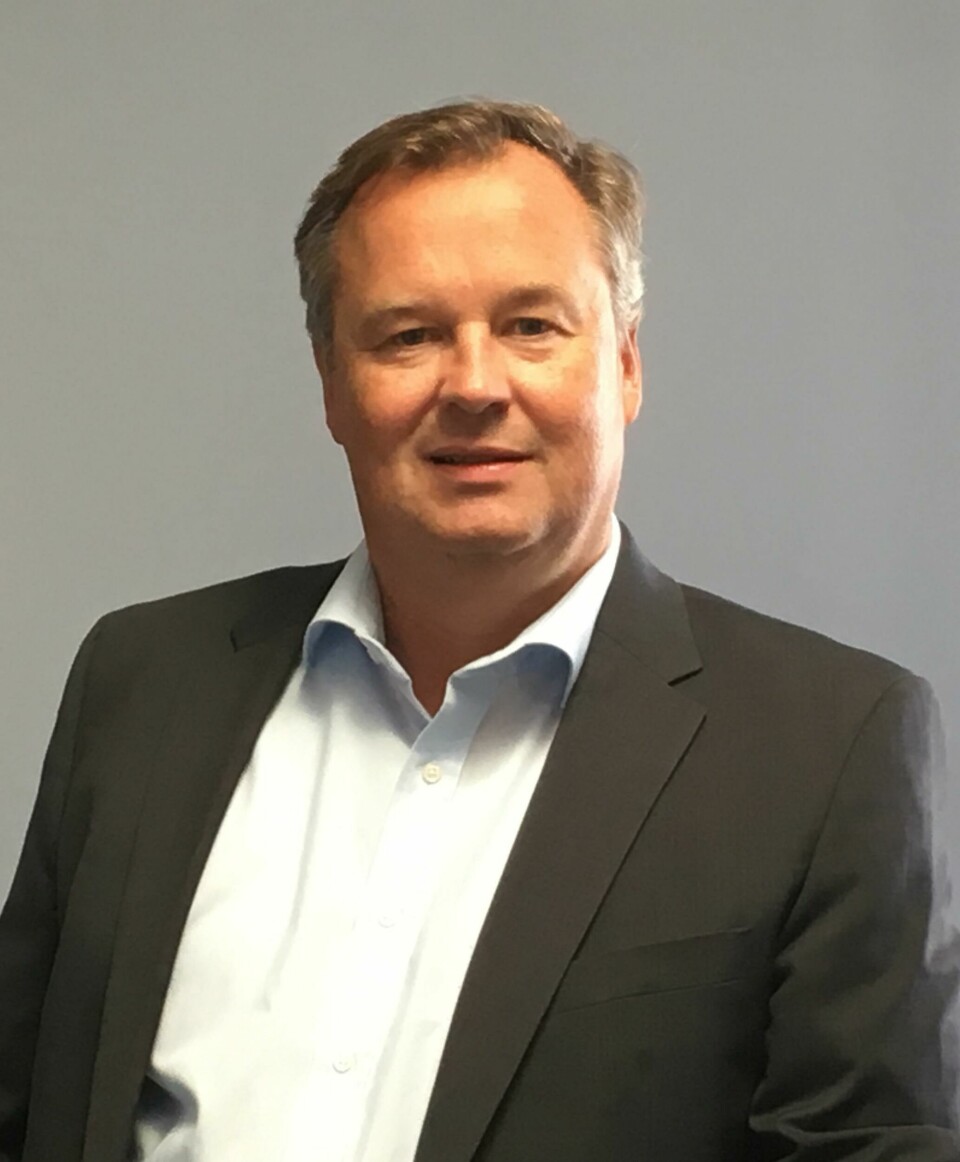
What role does sustainability play in your respective day-to-day roles at BMW?
Wolfgang Rudorfer: We are collecting the numbers and reporting sustainability in our integrated BMW Group Report, which [since 2020] brings together the Sustainability Report [formerly the Sustainability Value Report] and the Annual Report in one paper.
It was not new to my department when I joined and I really enjoyed having discussions with colleagues. They already had a lot of ideas in which direction the sustainability topics can move.
I also found that with the transport service providers [TSPs], both in Europe and the US, they weren’t laughing or asking why we wanted to become more sustainable in transport. Everyone was on the same page, which was a little surprising but something I was very happy about. I think every topic has its time and the past few years have influenced not only society but also the transport industry in terms of finding ways to get more sustainable.
How would you break that down into some of the specific targets that you have in logistics, perhaps over the shorter and medium term?
Maike Rotmann: BMW has three different focus points: supply chain, production and the carbon goals for when our cars are already in use. We are part of the supply chain, which is close to the production department, and our CO2 footprint is part of the supply chain – Scope 3 as we call it. The first goal that we’ve set is to reduce our carbon footprint, for [the period between] 2019 to 2030, by 20% within the whole supply chain. Those goals are quite ambitious but we are focusing on achieving them with our service providers and with our colleagues from the purchasing department.
Could you describe some of the latest developments – the new things that you are working on to realise those sustainability goals?
Wolfgang Rudorfer: We’re working very closely together with our TSPs across land, sea and airfreight. We’ve kicked off some projects where we tried out LNG or electric trucks, for example. But we are not only looking at LNG or electric vehicles, we are open for any technology that can help us to gain more sustainability. As those technologies are at different levels of maturity, we have to check which technology we can use with each supply chain. This is only possible if we work together with our TSPs who buy or invest in those technologies, and then we can try them out.
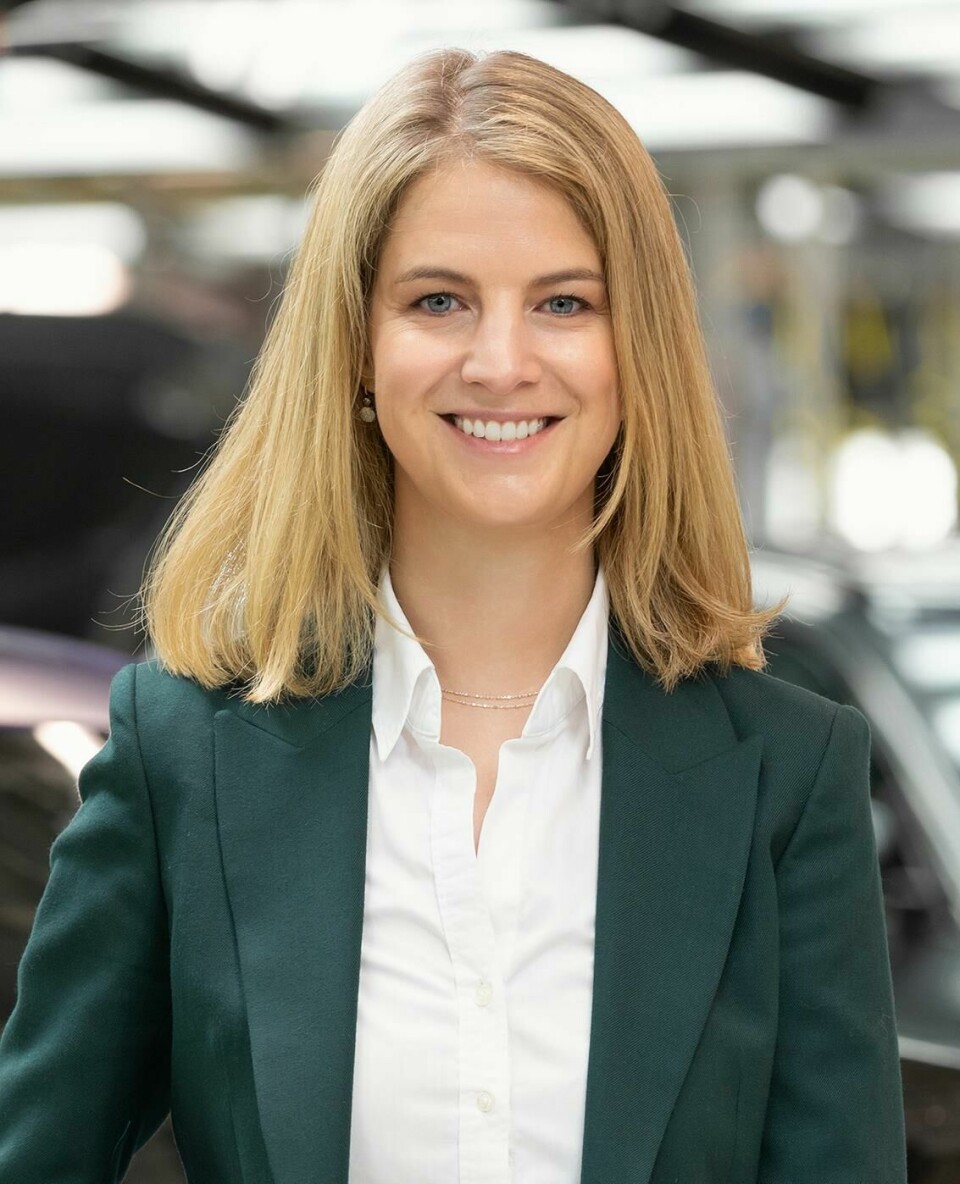
[More specifically,] we are using Bio-LNG [trucks] in the UK, and LNG-Trucks between Bavaria, Leipzig [in Germany] and Austria. We are also talking to TSPs who are using HVO [hydrogenated vehicle oil from cooking] and also looking at hydrogen. The technology that we are doing most with for now is LNG. This technology is basically the one that has a more widespread infrastructure in Europe.
Does that influence from whom you’re purchasing services and where you’re purchasing them?
Wolfgang Rudorfer: In terms of parts, we are calculating CO2 emissions in a similar way as we do with the other costs and so sustainability is one decision point [effecting] sourcing. In terms of purchasing transport services or making contracts with TSPs, again sustainability is one topic integrated into our purchasing decisions.
Are there similar projects in terms of the alternative fuels and technologies used in outbound logistics?
Maike Rotmann: On the outbound side it is less the supplier but more a question of plant allocation – which plant produces for which market. In regards of sustainability, it’s the best thing if you don’t drive any kilometres at all. But of course, we have to look at costs and quality as well. Still, avoiding every gram of CO2 is the right way to start. If we have to transport any parts or vehicles, we have to do it in the most sustainable way possible, which means reducing distances and using the most sustainable transport options, for example, LNG or battery electric trucks, or using biofuels.
Then it comes down to operational efficiency. If we have to drive anywhere it is best to avoid empty trucks, which is not only a question of sustainability but also a question of costs; they go hand in hand.
How much has sustainability changed the way the wider supply chain purchasing and manufacturing groups work together?
Maike Rotmann: It’s changed a lot. In the past, company decisions were mostly driven by costs and by time: what was the most cost-efficient or fastest scenario. Now another question is, which one is the most sustainable? This has become important more recently, not only on the company side but also on every tender. So, if we are tendering any transport, we always compare from these different sides: cost, efficiency, time and sustainability.
Is there any scope for sustainability goals being met by combining some technology or thinking between inbound and outbound?
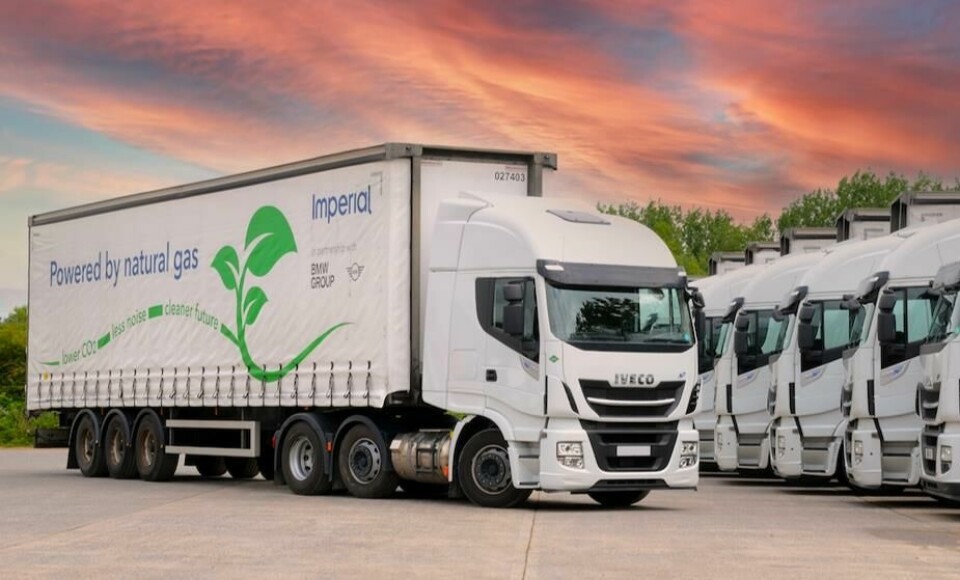
Maike Rotmann: We have great ideas when it comes to infrastructure for charging and for fuelling when we plan for a new plant – charging e-trucks, for example. That’s something we can use from the inbound and the outbound side. But when it comes to a ship, for example, it gets complicated. We have ro-ro ships for vehicles and it’s not possible to transport parts with them.
In Switzerland we introduced some truck transport this year that runs on HVO. We also have battery electric trucks here in Munich that we are using on the inbound side. Next year in the UK we will have LNG trucks for outbound that will run around the [Mini] plant and to the ports.
When you look at the inbound side, transport can be very time critical. It can really depend on half-an-hour or an hour if the truck is on time or not. You don’t find that necessarily on the outbound side where [the window can be] a day or within a week, depending on where you are. But if you are half an hour late or not at the dealer it is less likely to have such a serious impact.
Maike Rotmann: On the outbound side, what we’re also looking at in Munich is the use of battery trucks. We have some shuttle trucks that are travelling around 50km and we could use a battery electric truck easily, because it is over a short distance.
What about investment in new digital tools that you might be using to more accurately track parts or finished vehicles?
Maike Rotmann: You can only manage what you can measure. That’s the same for sustainability. The challenge we are facing right now is that we need to be able to have full transparency of our carbon footprint, but we have restrictions on how to report that, so we need to fully rely on the data that we have. Right now, we’re calculating after a standardised method. We are not measuring our CO2 footprint, we are calculating it based on that standardised method.
You’ve probably heard of DIN EN 16258 [the European standard calculation and declaration of energy consumption and GHG emissions for transport services]. That standardised method is what we are using because we have to be transparent, and we have to be able to answer every question that is asked when we publish our data every year.
Wolfgang Rudorfer: We’re improving the transport logistics calculation method by using a cloud data hub so that we no longer have to collect the data manually but get it in an automated process. It means we can be more accurate and save time for our employees.
The most important thing from my perspective is that we are counting at all. Starting to count, starting to make calculations on which suppliers lead to more or less CO2 reduction, that is, from my perspective, an important aspect on making decisions.
Maike Rotmann: What would be helpful in the future is if we had a chance to get all the real-time data of every type of transport that we are using. That is going to be a huge challenge in the future.
Let me describe it with an example. When we talk about trucks in the US, for instance, we know that it’s a truck but we don’t know exactly if it’s an engine with Euro 5 or Euro 6 [emissions] standard. We talk to a lot with service providers, and we talk to colleagues from other industries, and we’re all facing the same challenges when it comes to CO2 data.
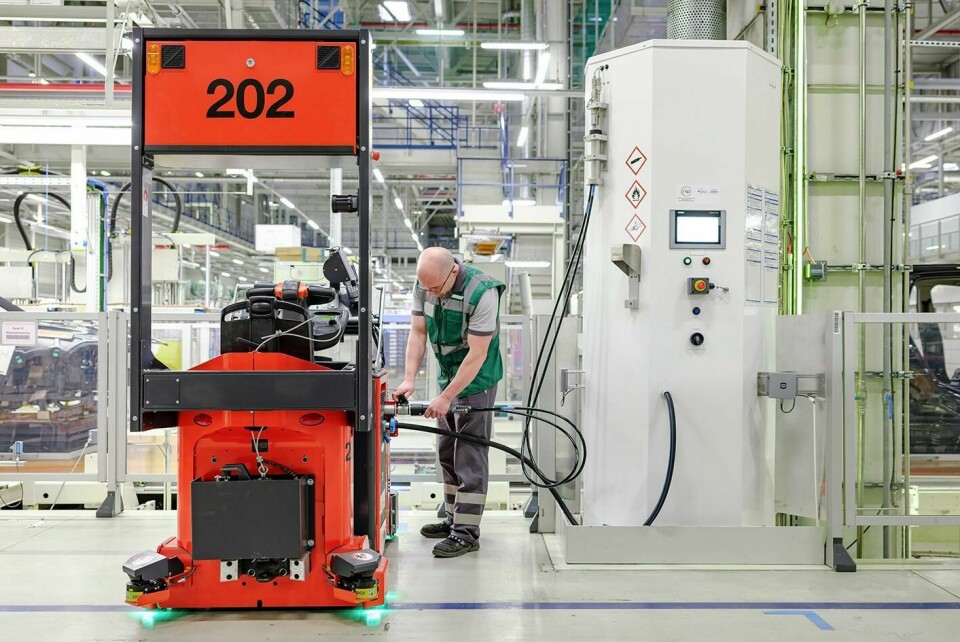
Is an important part of the digital system process to really capture that data in the network and make it more predictive in some ways as well?
Maike Rotmann: One thing that is absolutely necessary is that we are able to process the data we get and have it in dashboards. We need to be able to include it in all of the planning and steering applications that we already have.
Last year BMW forecast that the average amount of CO2 emitted per unit in the production and delivery of an electric vehicle was going to actually increase to 14 tonnes from the 10 tonnes used in delivering combustion engine car. That is if no special measures were taken to compensate and reduce the emissions in the supply chain. What can you do to bring the overall emissions from that unit down as more cars become electrified?
Wolfgang Rudorfer: Yes, basically the electrification of cars leads to new components [such as the lithium battery]. We are trying to focus here not only on [alternative fuels in transport] but also on optimising the production network. We are analysing and planning the sourcing of the components so that it leads to less CO2 emissions.
The question of CO2 emissions is also part of our product projects, in which we develop our cars but also the production process and the sourcing process. And in these concept phases we are also focusing on the CO2 emissions and are trying to design the supply chains so that our whole CO2 footprint is being reduced. By doing this, then we have the calculation of how much CO2 runs into one plant and by dividing through the numbers of cars produced, we are also focusing on the reduction of CO2 per car.
Maike Rotmann: Also, it’s not just us working on the topic of sustainability. We are lucky to have service providers that have excellent ideas and they ask us if we would like to try an idea, and how we would like to support them. It is really a network of passionate people wanting to change processes from how they were done in the past [and potentially] be able to roll them out into different transport networks.
We also try to improve our current transport network, for instance, by shifting transport modes. We moved to rail shipments on the Silk Road last year and that has a big impact because it’s not only cost and time efficient, it’s sustainable.
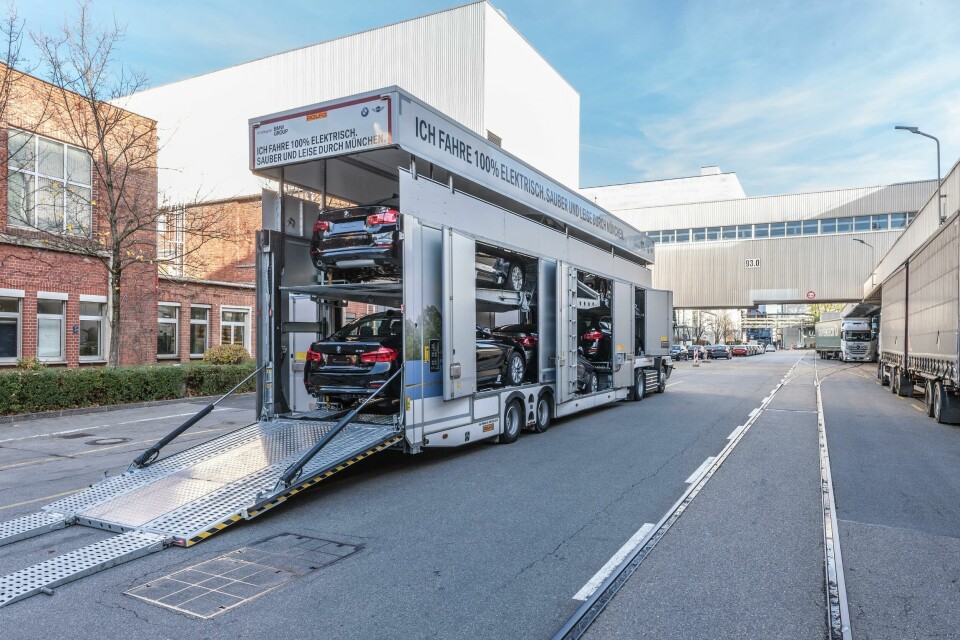
Wolfgang Rudorfer: We are also already running two trains every day from northern Germany to Bavaria to supply our plants with parts, and there we changed to green energy with the trains as well. The pre-carriage from our packaging plants to the North Sea harbours is done by train as well.
Maike Rotmann: On the outbound side, already 50% of our vehicles leave our plants via train. In the next years we are looking to improve how many parts of the train railway network are electrified, and that’s maybe one of the next questions or challenges that we’re facing – infrastructural projects within Europe.
Same in the US, we have to find partners in the countries or seek government support to help us achieve those goals. It’s not just on us or on the service providers, we need the infrastructure to be able to implement those technologies with political support.
How important will rail and other sustainable modes of transport be in meeting BMW’s 2030 sustainability target?
Maike Rotmann: Very important. These decisions are already made when you plan your network. So, when you think about which ports you will use in the future, from where to where do you have to transport, you can already set all the premises that you need for using rail as an alternative.
Wolfgang Rudorfer: It’s also important to remember that rail is basically something for long distances. On short distances we have to look at different technologies, as you always need a consolidation for train freight. It has to meet the demands of sustainability, economics, lead times and delivery performance.
How closely are you having to work with your service providers to identify these different opportunities within this complexity of regulations and infrastructure? Does this require a different approach with your TSPs to collaborate on your ideas?
Wolfgang Rudorfer: Yes, in the past few years the collaboration with the TSPs has intensified and this is a good situation for both inbound and outbound. Everybody can learn from a TSP, no matter if it’s for parts or for cars, and we have intensified this collaboration a lot.
Is the approach to contracting within logistics changing to accommodate the new demands on the supply chain and look much more long-term? It would be difficult for any of these providers to make the changes we’re talking about if they’re having to renew a yearly contract and tender to the lowest price.
Wolfgang Rudorfer: Yes, but the positive thing is that we are not the only ones. The whole industry is going into this. I think the big advantage for the TSPs is they don’t have to be afraid if they are investing in something for BMW and one of our competitors doesn’t need it. Everybody is working on this topic and I think this is something that gives more safety to the decisions made in other companies. This is something that helps the topic of sustainability move forward.