Mercedes-Benz breaks ground on battery recycling plant in Kuppenheim
Mercedes-Benz Group has broken ground on a 7,000 sq.m lithium battery recycling plant in Germany, with annual capacity to handle 2,500 tonnes of battery material from hybrid and pure battery electric vehicles (BEVs). That material will be fed back into to produce more than 50,000 battery modules for new Mercedes-Benz models, said the carmaker.
Mercedes-Benz said it was investing a double-digit, million-euro amount in the construction of the plant, which will operate on a carbon-neutral basis. The plant will use a photovoltaic system and 100% externally purchased green power. It will also be funded by the German Federal Ministry of Economics and Climate Protection as part of a scientific research project.
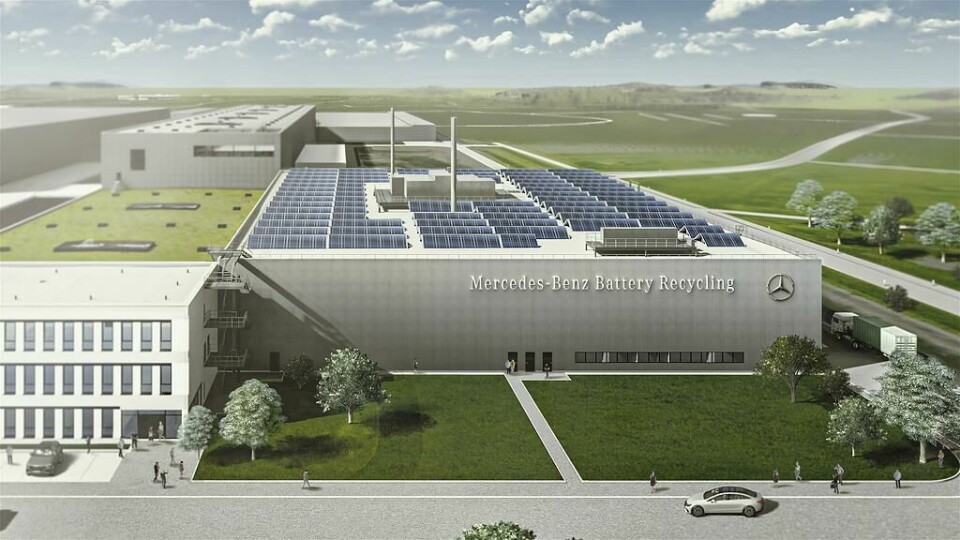
The move promises to cut future reliance on the supply of battery materials from overseas locations as well as making the process of battery production more sustainable. Carmakers are susceptible to disruptions in the supply of minerals and materials used in the building of lithium-ion batteries because of the concentration of suppliers in specific global regions, some with questionable human rights records, and the associated time and increasing cost in shipping those materials.
Circular economy on energy
Dismantling of the batteries at Kuppenheim is set to begin at the end of this year. Later the facility will also shred, dry and process the battery materials using a hydrometallurgy process developed with technology expert Primobius, a joint venture between German mechanical engineering company SMS and the Australian project developer Neometals. The carmaker has also worked with scientific partners at the Karlsruhe Institute of Technology and the Technical University of Berlin.
Together the partners will recover battery-grade cobalt, nickel and lithium for reuse in the production of batteries, and will in future also recover graphite. Mercedes-Benz said it expects a material recovery rate of around 96%.
Working with its partners, Mercedes-Benz said it had covered the full process of battery recycling including the development of a logistics strategy, the sustainable recycling of valuable raw materials, and the reintegration of recyclates into the production of new batteries.
“This foundation symbolises the decisive step towards closing the material cycle for batteries from Mercedes-Benz,” Jörg Burzer, head of production and supply chain management at Mercedes-Benz Group. “With a recycling rate of more than 96%, a ‘mine of tomorrow’ is being created here in Kuppenheim. The innovative technology approach enables us to incorporate the valuable raw materials into new Mercedes-EQ vehicles.”
Mercedes-Benz said it was now looking at each vehicle model to see how components and materials can be recycled suitability in the context of a circular economy. That strategy covers the entire supply chain from mining to recycling
This approach covers the entire supply chain from mining to recycling, according to the carmaker, including looking at the working conditions of employees at. Mercedes-Benz said it was offering reconditioned batteries as replacement parts for all EVs.
Batteries that can no longer be used in vehicles can continue to be used in its second-life storage system for supply to Factory 56, the €730m factory at Sindelfingen in which Mercedes-Benz makes the S-Class and is working toward zero-emission production.