Volkswagen Group Logistics: Come together, right now
All carmakers are [sta_anchor id=”1”]grappling with how to plan and respond to the technological, social and economic changes that are expected to affect their products and businesses. Manufacturers must simultaneously manage rising demand for both traditional and alternative fuels, while exploring new models for mobility that might, in future, change the way consumers buy and use vehicles altogether.
Meanwhile, connected devices and the potential of the so-called ‘industrial internet of things’ could herald major changes in many manufacturing and distribution processes.
Choosing the right investments and focus is difficult for any OEM, especially as new players and disruptors enter the market. For the Volkswagen Group, the challenge is in some ways multiplied, as it must confront how to manage change across 12 brands with different market positions and functions, from economy cars to luxury marques and commercial vehicles.
On top of that, it must also continue to contend with the fallout from its diesel emissions scandal, whether from customers, shareholders or regulators.On the other hand, it is the ‘group effect’ that may offer the world’s largest carmaker one of its great advantages: a compounding of innovation and new approaches that can come from individual brands and then be shared with others. That approach is as true for new technology in products as it is for changes in plants.
The Volkswagen Group’s ‘Together – Strategy 2025’ is the company’s plan to unlock this potential and accelerate development across the myriad directions of the new economy. It also turns out to have significant implications for supply chain and logistics.
The group’s chief executive, Matthias Müller, said the plan would transform Volkswagen “from an automaker into a globally leading mobility provider”. Steps towards that have included establishing a Berlin-based mobility division, MOIA, to become a leading provider of mobility services, focusing on ride hailing and connected commuting. Already, new relationships are starting to form between the company and new types of suppliers and third parties. The investment of $300m into ride-hailing service Gett is just one example.
For the Volkswagen Truck & Bus division, which includes Volkswagen, MAN and Scania brands, this connectivity has significant implications. Trucks are already being deployed in a number of autonomous driving and platooning projects underway in Europe and Asia in which a driver leads in one truck with several driverless trucks following behind. The company’s trucks are also equipped with new in-vehicle telematics and logistics systems that are intended for wider use across brands and to play a larger role in facilitating freight sharing between logistics companies and shippers.
This mobility focus will only intensify with the group’s development of autonomous vehicles. Volkswagen anticipates having a production-ready, level-five autonomous vehicle (the highest level, requiring no driver) by 2021.
‘Together’ will also reshape many parts of the group’s production and supply network in the coming years with the production of electric vehicles and batteries. Müller has revealed that the group will treble investment in electric vehicle and battery development over the next five years, spending €9 billion ($10 billion) compared to €3 billion in the past five. By the end of 2018, the group plans to offer more than 10 new electrified models, adding over 30 more battery electric vehicles by 2025.
The Volkswagen brand has already added an electric version of the Golf at a factory in Dresden, which it converted last year. The Volkswagen ID, the first model in the group’s electric modular toolkit, or MEB, which will be the basis for many of these models, will roll off the line in Zwickau by 2019. A laboratory for battery pack research will open in Salzgitter, south of its headquarters in Wolfsburg.
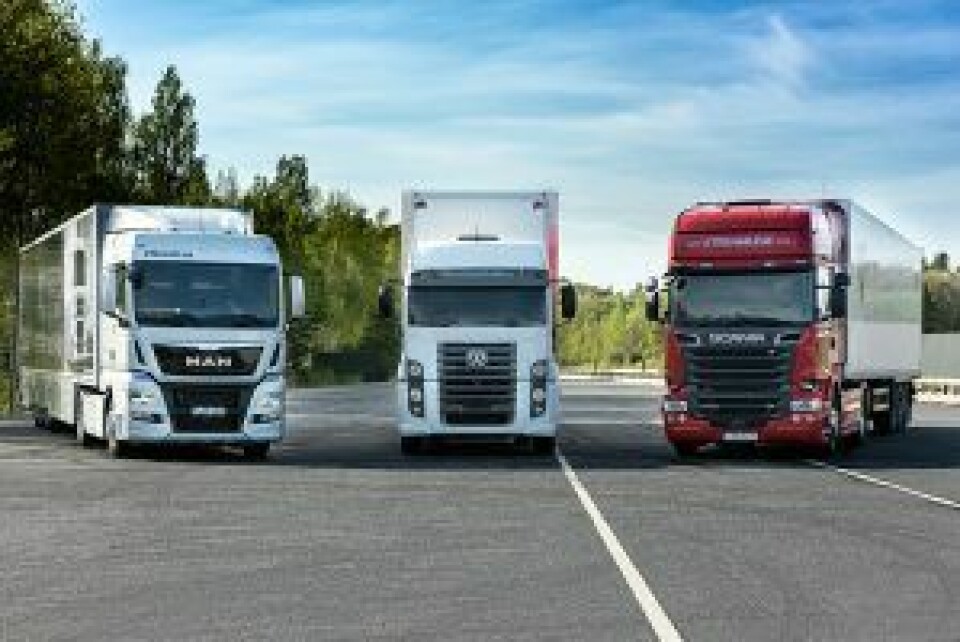
The Volkswagen Group, including its commercial vehicle division, is doing more parts sharing across the supply chain
‘Together – Strategy 2025’ also seeks deeper integration of the supply chain. Audi and Porsche, traditional competitors in the premium segments, are sharing more common engineering, parts and modules. In the commercial vehicle division, brands share components and systems including gearboxes and axles, as well as in-cab telematics.
Perhaps most importantly, there is a push to ‘open up’ the group, encouraging new ideas and innovations from brands and regions, suppliers, startups and from other manufacturers. In spring, the group signed a common development and purchasing agreement with commercial vehicle producer Navistar in North America, as well as with Tata Motors in India for low-cost cars. In China, the carmaker has just confirmed a new joint venture between Volkswagen and Chinese OEM JAC, which will build affordable EVs under a new brand in the country.
All of these strategies are important for the group’s supply chain and logistics, and notably for Volkswagen Konzernlogistik (group logistics), the carmaker’s central supply chain management organisation, based in Wolfsburg, which will be closely involved with any production and supply network changes, as well as bringing out new products and digital processes. According to Astrid Lühring, head of material logistics, digital and sustainable logistics form a core part of the group’s long-term strategy.
“Material logistics is also to be realigned in accordance with the ‘Together – Strategy 2025’ strategy in order to play a part in actively shaping transformation within the automotive industry,” she says. “Future trends open up entirely new horizons – with visions going as far as a supply chain which is almost completely [sta_anchor id=”2”]digitalised, networked and autonomous.”
Global stewardship, local leadership
The sheer size and scale of the Volkswagen Group supply chain – which globally includes 68 vehicle assembly plants, 52 internal component plants and around 8,500 tier one suppliers – make it a target for cost savings and productivity improvements.

At the same time, the risks to assets and capital that any disruption to this network would cause necessitate caution when implementing changes or new processes. An approach is therefore needed that considers local benefits, as well as the wider impacts on the supply chain across the group.
That is why Konzernlogistik acts as the chief steward of network planning, delivery and distribution across Volkswagen’s 12 brands. It is the central steering organisation for cross-company programme planning – including forecasting demand and capacity across plants – for inbound logistics, crossdocks, returnable packaging, ocean containers and finished vehicles. While it has the most direct influence in Europe, group logistics also has an important role in setting global standards and purchasing terms, and can also influence transport network design in other regions.
Since 2004, Konzernlogistik has been led by Thomas Zernechel, head of group logistics; Astrid Lühring has led material logistics since 2015; while Markus Lange has led vehicle logistics for the group since later the same year.
The Wolfsburg-based team oversees a huge network. In 2016, group logistics was responsible for around 74.5m cubic metres of production material across Europe; a further 1.4m cubic metres were shipped outside Europe, including complete knockdown kits (CKDs) and modules.
In operating terms, the transport flows are as large as they are varied, multimodal and international, including thousands of trucks and rail wagons moving through the system at any one time, as well as inland barge for some flows. Last year, the group also shipped around 250,000 TEUs of material by container ship, mainly from Europe to the rest of the world. For some time-critical parts, Volkswagen Group has been sending more containers by long-distance rail to China, mainly to the FAW-VW joint venture plants in north-east China, says Lühring.
For outbound logistics, group logistics handled 5.2m vehicles in 2016 (out of 10.3m global deliveries across the company), including 2.5m vehicles that moved by ocean across more than 8,700 shipments.
Konzernlogistik has responsibility across a huge network, however it does not centrally control and operate all of the group’s carriers and supplier flows. While it manages network design and engineering, including determining infrastructure requirements and standards, many transport operations are managed locally. For example, local plant logistics teams, in coordination with Markenlogistik (brand logistics), organise full truckloads direct from suppliers, as well as milkrun collections for a specific plant or brand.
Logistics purchasing is also a multi-party collaboration. Managers at plants or brands choose providers for specialised services, such as just-in-sequence providers or in-plant logistics. However, group logistics sets the tariffs and facilitates tenders, while the central purchasing department handles contracting. “Long-term cooperation with service providers and suppliers is the best way of ensuring stable processes,” says Lühring. “Together with the purchasing department, we select[sta_anchor id=”3”] partners that are innovative, reliable and competitive.”
When Astrid Lühring took over the top role in group material logistics in 2015, it was the continuation of a career with Volkswagen that has seen her touch many parts of the inbound and production supply chain.
She started as a trainee at Volkswagen in 1986 before pursuing university studies. Afterwards, she got her start at the carmaker’s plant in Emden in 1993, working in various areas. From 2001 to 2003, she took over as head of pre-series logistics at the carmaker’s joint venture in China with SAIC in Shanghai, before leading various production logistics departments back at group headquarters.
From 2009-2015, she was head of CKD logistics for the group, a role that was notable for its complex mix of parts packing and consolidation operations, as well as multimodal transport of containers.
Today, reporting to Thomas Zernechel, head of group logistics, her responsibilities include the planning, management and optimisation of transport and packaging between plant, suppliers and logistics providers across Europe.
Her team also plans and purchases ocean container imports and exports for supplies to all regions where the Volkswagen Group is active in production.
So happy together
What’s important at the group level, especially for material logistics, is establishing common practices, as well as consolidating parts and packaging. For example, group logistics has now implemented three crossdocks in Europe, known as ‘KCCs’, to combine suppliers across brands and dispatch in full truckloads to plants. These have replaced brand-specific crossdock and consolidation centres in Europe.
Last year, group logistics opened a new, enlarged facility in Malacky, near Bratislava, Slovakia, close to a large group plant. KCC Bratislava collects material from around 540 suppliers, mainly in Slovakia, Hungary, Romania and Bulgaria, consolidating the material for shipments to 28 plants in Europe across Volkswagen passenger and commercial vehicles, Audi, Skoda, Seat, Porsche and Lamborghini.
“[KCC Bratislava] is the connecting point where transport synergies are evident, with short collection distances from regions with a lower supplier density,” says Lühring. “As a result, the new KCC has reduced truck trips between it and European plants by almost 10% [compared to the former facility.]”
Another KCC in Heilbronn, south-west Germany, close to Audi’s plant in Neckarsulm, combines parts from suppliers and plants for delivery to factories on the Iberian Peninsula, including Volkswagen sites in Portugal and Spain, and Seat facilities close to Barcelona, which also build Audi models.
The third KCC is in Baunatal, close to Kassel in central Germany, where the group also has a major transmission and emission control centre plant, and its central global service parts warehouses. KCC Baunatal serves group plants mainly in Poland, including Polkowice – a group engine plant – and vehicle and component plants in Poznan. The crossdock also supplies the Autoeuropa plant close to Setubal, Portugal, which builds Volkswagen and Seat vehicles.
Managing the cross-brand returnable container and packaging fleet in Europe is another core area for group material logistics. Within it, Konzern Behältermanagement (group load carrier management) owns universal small and large standard load carriers used across the group, which number close to 19m in Europe. It owns a further 2m or so specialised racks used across plants and platforms, for example for the MQB modular transversal toolkit.
“In the case of special containers, we define the key data, coordinate and order the development of containers in the group brands,” Lühring says.
Behältermanagement acts as a service to ensure the best availability of load carriers for plants and suppliers. Suppliers order the load carriers they need, and then a secure software system automatically calculates the best transport option for moving empties between plants and suppliers.
“Among other things, we apply an allocation algorithm, which ensures a cost-optimal distribution of our empty load carriers from plants to our suppliers,” says Lühring. “A tracking system also prevents incorrect shipments.”
As with freight transport, group-wide functions for load carriers are complemented by brand and local management. Each plant tends to own a separate load carrier pool, such as dedicated racks for equipment that might only be used between a specific plant and its supplier.

Ocean containers, including for complete knockdown (CKD) kits, also benefit from group and brand management. In some locations, brands run their own packaging operations, while group logistics sets standards for CKD packaging dimensions, as well as managing shared packing centres. Container shipping, meanwhile, is purchased across all brands.
Group logistics also maintains a shared process for the management of the production and shipping schedules to help coordinate intercontinental supply flows.
“In addition, we use integrated interface technology that improves transparency for all the parties involved in[sta_anchor id=”4”] the supply chain,” adds Lühring.
Nurturing digital innovation
The collaborative way in which Konzernlogistik manages logistics and packaging across brands reflects its wider approach to digitalisation in the supply chain. Lühring says that the group’s objective for logistics is digitalising the “entire supply chain including all process partners”. It is in this group-wide approach that she expects to achieve better networking and transparency, environmental improvements and more ergonomic labour processes.
To get projects to a group level, however, innovations often start with brands, with concepts and technology tried first at specific plants or logistics centres. Konzernlogistik then assesses if these ideas apply more widely.
“All the brands have people who are responsible for testing ideas in pilot projects,” says Lühring. “The group’s central innovations management system bundles these activities for the various brands, ensures that they are networked and provides support for the rollout of successful projects.”

Multiple brands have led the way in areas such as materials handling automation and picking. Lühring gives an example of a pilot project at the Volkswagen brands plant in Wolfsburg for RFID wristbands, in which workers scan parts for verification in picking areas. Skoda was the first to use a smart scanner glove in picking, while Audi and Porsche, among other brands, are using AGVs to move most commissioned goods to workers in the parts supermarket.
“In this context, the group has one decisive advantage [over competitors],” she says. “The variety of our brands allows us to give one brand a pioneering role for the trial of new solutions. If a project is found to be highly promising, it can then be applied to other brands.”
Finding the right projects across brands to support is not easy, but one way the group rallies together such new ideas has been through an annual logistics innovation day. The event showcases projects and new technology, with logistics executives from group divisions, brands, logistics providers and other external companies, such as digital startups. Afterwards, the group logistics team and its local counterparts evaluate the different ideas and determine where to make investments or run trials.
“We exchange information on the latest trends, best practice examples and future visions with each other and external companies,” says Lühring.
In some cases, group logistics gets involved more directly with specific projects. In Mexico, for instance, it worked with Audi to introduce an RFID system to tag and track every load carrier for its factory in San José Chiapa, with an ongoing rollout at its suppliers in Mexico as well.
“We see further potential in the digitalisation [of packaging tracking], which will make the entire process even more transparent and comprehensible for all concerned,” she says.
The central group logistics team also tries actively to identify gaps in visibility or inefficient processes. For example, it is converting a number of paper-based, manual processes so they can be done via smartphone or tablet. Lühring points to a recent project to use tablets for spot checks of logistics forwarders to ensure they are compliant with various transport legal requirements.
A capacity management system, meanwhile, is being extended to monitor parts inventory and production capacity not only from tier ones, but also lower tier suppliers. “Our vision is to eventually cover the entire supply of parts. But because of this tremendous complexity, the first step will be to focus on high-risk parts across the supply chain,” says Lühring.
While Konzernlogistik has international scope, including sending materials and vehicles around the world and setting global standards, its remit for network design has traditionally been strongest in Europe.
Brand operations often have separate origins and histories around the world, whether the 50-year Volkswagen plant in Puebla, Mexico, or various joint ventures in China.
There has also been limited scope for network engineering, including container pooling and common packaging across group brands in other regions. For regional flows, that is partly because of a lack of density. However, different truck dimensions between Europe and other regions have limited the scope to extend the existing pool of load carriers.

Lately, though, the group has moved deeper into regional coordination. The best example has been in North America, where the North America Region (NAR) network was a joint project between Konzernlogistik, Volkswagen plants, the new Audi factory in Mexico and Audi Markenlogistik.
Together, an inbound network was designed with shared crossdocks to collect material across designated geographic supply zones in the US, Mexico and Canada, with joint third-party logistics providers appointed to manage each zone.
A regional group logistics office was also established, based in Puebla, with teams that work with the regional divisions on facilitating shared flows, common standards and potential returnable container flows, all of which the group hopes to develop across group plants and suppliers in North America.
Importantly, says Astrid Lühring, NAR is not a “copy and paste” from Europe, but has developed according to the specific requirements of plants and brands.
“The collaboration of the plants and organisation in NAR was a successful step for identifying and sharing synergies,” she says. “The idea is not to copy the European concepts but rather to combine global success stories for the optimum local solution.
“For example, in cooperation between group logistics and Audi and Volkswagen plants, we were able to realise new processes within the transport network and to benefit even more strongly from synergy effects than was previously the case,” she continues.
The success of this combination has encouraged the group to look at other global opportunities. Though Lühring is not ready to provide the specifics, she says activities are already in place in Brazil and in China to identify improvements and potentially bring more of the networks together.
An information discovery
One of the most important IT projects at the group logistics level is the current rollout of a cloud-based web module called Discovery, which automates and standardises notifications between Volkswagen, suppliers and logistics carriers.
The project began three years ago as an investigation into the daily supply chain by the group’s logistics process partner management team, according to Lühring. The study identified gaps in the exchange of information, including inconsistent data formats across suppliers, forwarders and packaging companies.
For example, each company tends to have its own system, some of which don’t communicate properly with each other. Many manual processes, whether phone calls or emails, have thus been required to confirm when a shipment is dispatched from a supplier, arrives at a crossdock or port, and is received by Volkswagen.
Konzernlogistik, together with IT specialist Euro-Log, developed Discovery to address this. Through the platform, carriers receive notifications from suppliers based on a plant’s delivery schedule, including part numbers, quantity and delivery date; the logistics provider in turn uses the platform to send a pickup notification to the supplier. Further steps along the chain are also fed into the system, including transport declarations and legal documents, delivery of material and empty container notifications.
“The advantages [of Discovery] include having better predictability for suppliers, carriers, crossdocks and recipients. The improved data allows for better transport planning, network of optimisation and billing. We can also more easily account for carbon emissions and other environmental specifications in the supply chain” - Astrid Lühring, Volkswagen Group
Standardising the data is leading to a more stable, reliable chain of information, while the automatic transmissions result in significantly fewer reporting errors compared to manual notifications, Lühring says.
“The advantages include having better predictability for suppliers, carriers, crossdocks and recipients,” she says. “The improved data also allows for better transport planning, network optimisation and billing.
“We can also more easily account for carbon emissions and other environmental specifications in the supply chain.”
As a cloud-based system, Discovery is easier and less costly than legacy IT systems to integrate across the supply chain, adds Lühring. The platform will initially be applied across the group’s 5,000 suppliers in Europe, with a global rollout to follow.
However, integration into the platform will be done in a phased manner. By early 2018, all European tier suppliers will use Discovery. Shortly thereafter, it will also be added to the systems of express and parcel shipments, followed by direct and specialised deliveries. Eventually, all suppliers and logistics-related providers will use it.
“This is a good solution from a long-term point of view,” says Lühring. “As scaling of the platform is easy, it will allow the group to more easily integrate new suppliers and carriers.”
The system has already garnered an award from AKJ, a German automotive industry body focused on production and logistics.

Open, diverse, connected, together
As laid out in its ‘Together – Strategy 2025’, the challenges ahead of the Volkswagen Group are formidable, as it pushes for technological change across its business and products, and continues to recover from the diesel scandal. Decisions made now will be key to the company’s future.
Attention will be on supply chain and logistics operations as much as anywhere. For example, after hitting an objective of reducing environmental impacts from vehicle production and logistics by 25% between 2010 and 2018, the Volkswagen brand has recently announced it will target a further 20% reduction from 2010 levels by 2025.
Meanwhile, some demands within ‘Together – Strategy 2025’ go well beyond emissions or cost reduction targets. Perhaps most important is the call for a fundamental process and culture change in how the group makes decisions and manages its operations.
Speaking at the group’s recent Annual General Meeting in May, Matthias Müller told shareholders that new technologies and structures would only be part of the answer to the industry’s many changes. “Above all, a new era calls for new ways of thinking: more agile and courageous, more entrepreneurial and pragmatic,” he said.
In particular, Müller emphasised the need to reduce bureaucracy and hierarchies, whether in pruning group-wide regulations (which now number 800 pages) or in redistributing responsibility and oversight across brands and regions as much as possible. Müller also spoke about a workforce and management cadre that must be more international, “more female” and more open to different cultural preferences and approaches.
Such demands apply to group logistics as they do other department. But it is interesting to note that it may already be a good example; and even an exemplary case study in harnessing cross-brand resources while leaving room for local expertise.
Astrid Lühring acknowledges that Konzernlogistik is changing with the group, particularly in adapting its organisation to keep up with digitalisation and electrification. But that progress has not come simply by centralising operations or buying the latest technology; rather, it has come by championing the best ideas, no matter what their provenance, and magnifying them across the group.
“Group logistics is working on new trends together with strategists and innovation managers from the various brands’ logistics departments,” says Lühring.

“We also cooperate closely with companies from the logistics and IT sectors and search for smart concepts for the efficient logistics systems of the future together.”
The willingness to share ideas with those beyond the logistics departments at the group is critical. For example, Lühring says Konzernlogistik has been working directly with engineers and researchers at Volkswagen Truck & Bus that are developing fleet systems in commercial trucks. As it turns out, both the logistics and engineering teams are very interested in reducing empty truckloads.
The key point of common interest is the commercial vehicle division’s new open digital telematics platform, RIO, which is being rolled out in newly built trucks this spring. The cloud-based, on-board platform is intended to link together all participants in a supply chain, independent of vehicle brand or the telematics system used, to show truck locations and availability.
For example, the system can provide information between logistics providers and shippers on real-time demands for freight that can be paired with empty trucks free to pick up new loads – something that will be valuable to Volkswagen’s own logistics operations.
“Using smart algorithms, RIO can link and analyse a variety of different data sources to provide users with recommendations for specific action on a real-time basis,” says Lühring. “This will allow [logistics managers] to make considerable progress with connectivity and transparency.”
Konzernlogistik is also working with the commercial vehicle division on green logistics and sustainability. Among other things, it is partnering with the brands to further develop alternative fuels for trucking, including compressed and liquefied natural gas (CNG and LNG). Earlier this year, for example, Skoda put four new CNG trucks into use at its main plant in Mladá Boleslav, in the Czech Republic, for both internal transport and to collect material from suppliers.
“Above all, a new era calls for new ways of thinking: more agile and courageous, more entrepreneurial and pragmatic”- Matthias Müller, Volkswagen Group
“In line with the group strategy ‘Together – Strategy 2025’, we are intensively pursuing the application possibilities of LNG-powered trucks with Volkswagen Truck & Bus,” says Lühring.
Volkswagen Group has also partnered with energy suppliers to increase the number of CNG filling stations across Germany.
Autonomous driving will make collaboration between Volkswagen’s logistics management and its truck-manufacturing arm even more important. While Lühring says it is too soon to discuss details, she reveals that group logistics has engaged with engineers at the division for projects concerning self-driving trucks. For platooning, MAN is currently involved in trials with logistics provider DB Schenker for convoys on German motorways; Scania is involved in a platooning trial in Singapore.
The autonomous revolution, together with other kinds of connected technology, is further pushing the group to partner with companies outside the traditional automotive supply chain. Volkswagen Group has allocated funding and trials for a number of startups working in disruptive areas like artificial intelligence, virtual reality and 3D printing.
Individual brands are also investing in such companies. Porsche has recently established several digital hubs, including one in Silicon Valley to explore opportunities. Last year, MAN invested $8.5m in FR8 Revolution, a Silicon Valley-based startup that has been developing an online platform for planning and purchasing freight cargo in the US.
Such partnerships, both internal and external to the group, as well as an openness to ideas and technologies, are essential to Volkswagen’s long-term strategy. For logistics and supply chain, at least, such changes are clearly starting to come together.