When disruption won’t quit, the 2025 Finished Vehicle Logistics conference shared how to stay balanced and agile
The Finished Vehicle Logistics North America 2025 conference revealed how leading OEMs are redesigning logistics to thrive amid trade shocks, EV disruption and capacity constraints. From agile planning to modular networks and EV-ready lanes, Automotive Logistics unpacks the sector’s shift from fragile to future-ready.
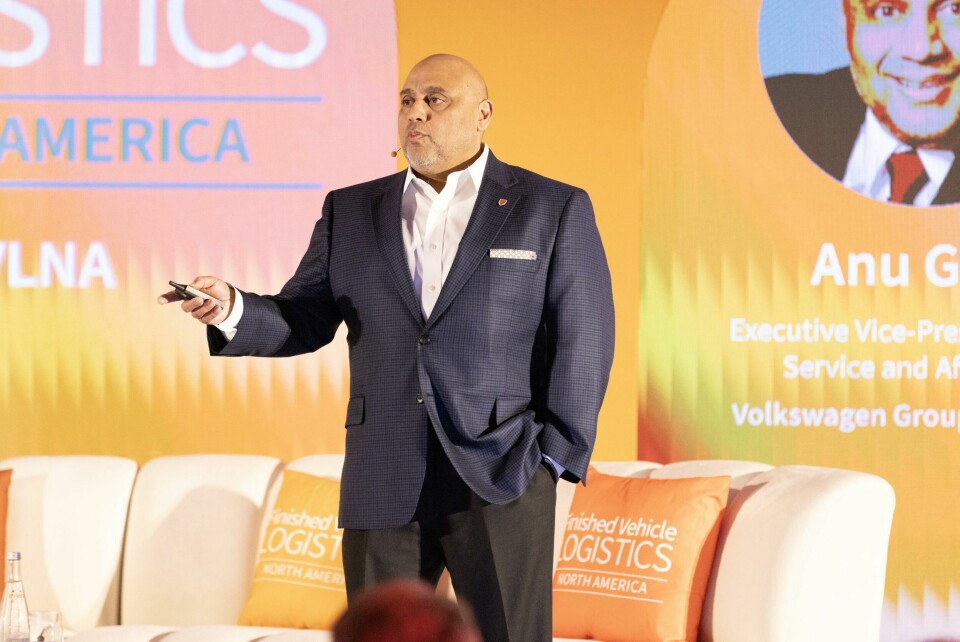
Highlighting the critical need for resilience and strategic agility in logistics, Goel emphasised the importance of flexible systems in navigating ongoing macroeconomic uncertainty.
“If we don’t build optionality into our networks, we’ll be caught unprepared.” That stark warning from Anu Goel, executive vice-president, group after sales and services at Volkswagen Group of America, captured the driving tone of the Finished Vehicle Logistics North America 2025 conference. In a time defined by rolling disruption – from tariffs and trade unpredictability to the growing pains of electrification – the automotive logistics sector is being forced to rethink how it functions. And quickly.
Although the event’s theme – “Creating a faster, agile, more competitive vehicle supply chain” – was set months in advance, recent tariff escalations and ongoing trade uncertainty gave it renewed focus. Though, while references to tariff uncertainty surfaced both on and off stage, discussions throughout the event were grounded in immediate operational challenges – ranging from lead times impacted by network constraints to evolving EV distribution needs and rail congestion that continues to test system limits. Key priorities also took centre stage: enhancing quality control, strengthening rail resilience, and leveraging partnerships, technology and data-led strategies to drive smarter decisions that can sustain throughput under pressure and remain responsive to change.
From fragility to flexibility
While disruption has become a familiar refrain, the industry’s current fragility is anything but. General Motors’ (GM) director of finished vehicle logistics, Amy Paulsen, pointed out that her team hasn’t had a “normal” year of operations since pre-Covid. Volatility isn’t the exception – from labour strikes and weather events to railcar shortages and policy swings. It’s baked into the system. Paulsen described during a panel: “There’s internal and external issues that make quality super important at GM. The external being tariffs, geopolitical things that we can’t control, railcar shortages out of Mexico… and then there’s the internal.”
“We’re looking at our end-to-end quality process,” Paulsen explained. “That includes how technology is deployed, how fit-for-purpose those tools really are, and what revisions we need to better support that process. It’s about ensuring our teams on the ground are deeply engaged – through site visits, test loads and IT testing – but also aligning strategically to create a consistent quality standard across the network.”
At the heart of the FVL North America 2025 conversations was the acknowledgment that legacy logistics models built on predictability are now out of sync with reality. OEMs like GM, Nissan and VW described how they’re redesigning networks to handle flux, not stability. Todd Myers, director of finished vehicle logistics at Nissan Group of North America, explained the company is adapting its finished vehicle logistics to reflect fluctuating demand and product mix. “We’re looking at ways to optimise our yard layout and load strategies to adapt to vessel bunching and network inconsistencies,” he said, noting that proactive communication with carriers and adjusting schedules in real time have become essential tools. “We’ve started taking a more agile approach to minimise bubbles in the pipeline and adjust quickly when plans shift.”
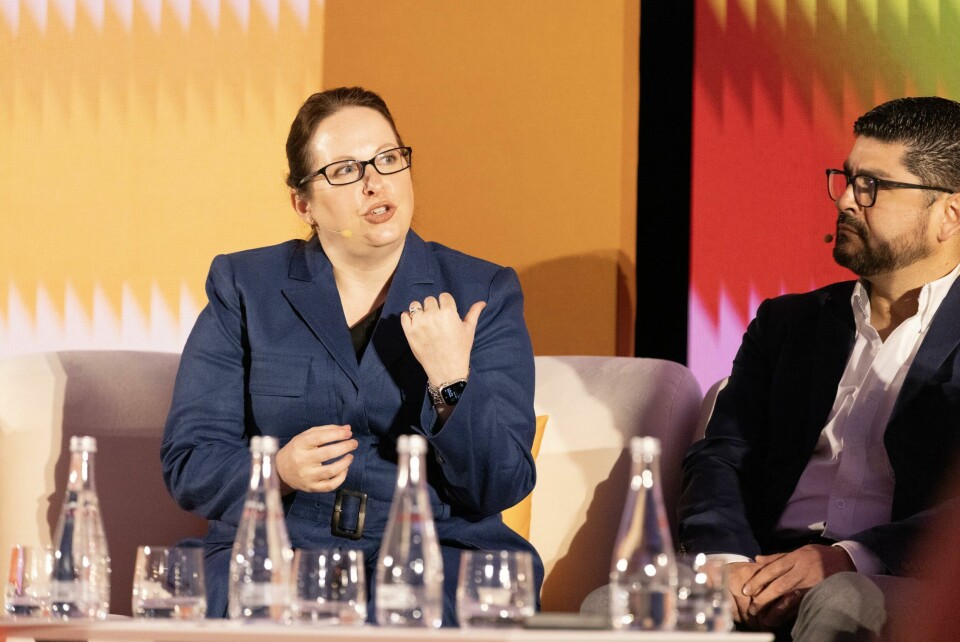
Emphasis was placed on logistics’ new normal and the importance of end-to-end quality control in navigating ongoing volatility.
This redesign of networks is also translating into scenario planning tools, modular network mapping and even shared strategies for flexing between rail, truck and short-sea shipping when bottlenecks hit. In an Automotive Logistics’ article “Address transport capacity shortfalls,” this concept of dynamic switching was highlighted as a blueprint for future-ready logistics.
At the heart of this strategic agility, Goel of VW Group of America brought a sharp focus to how OEMs must operate amid persistent uncertainty. As he shared during his keynote and Red Sofa interview, Goel explained that the real challenge isn’t disruption itself, but navigating the complexity of fragmented systems, particularly across US-Mexico flows.
For VW, this has meant building alternate supply and logistics routes across borders, deepening visibility across plants and vehicle distribution centres (VDCs), and maintaining close coordination with partners to flex operations when tariffs, weather or regulation interfere. Goel emphasised the need to embed resilience through system design – not just contingency planning. “If our logistics only works under perfect conditions, they don’t work at all.”
Electrification as a logistics stress test
OEMs highlighted how the electrification of the vehicle mix is prompting substantial change across logistics operations – impacting how vehicles are stored, loaded, secured and powered in transit. Tony Stinsa, director of inbound and finished vehicle logistics at International said: “An electric Class 8 truck is not just a heavier version of a diesel one – it’s a whole different beast.”
He pointed to the cumulative challenges this presents, from ensuring compliant securement of heavier units to needing equipment that can accommodate different centre-of-gravity profiles. Additionally, with EV rollouts growing faster than supporting infrastructure, OEMs and carriers alike are confronting the absence of scalable charging solutions along transport routes. Stinsa cited cases where vehicles require added dwell at VDCs or are rerouted away from more direct paths due to lack of charging access – compromising both efficiency and reliability. For logistics networks, this means planning with greater specificity, developing EV-ready lanes and preparing for interim solutions such as mobile charging units and dynamic staging zones.
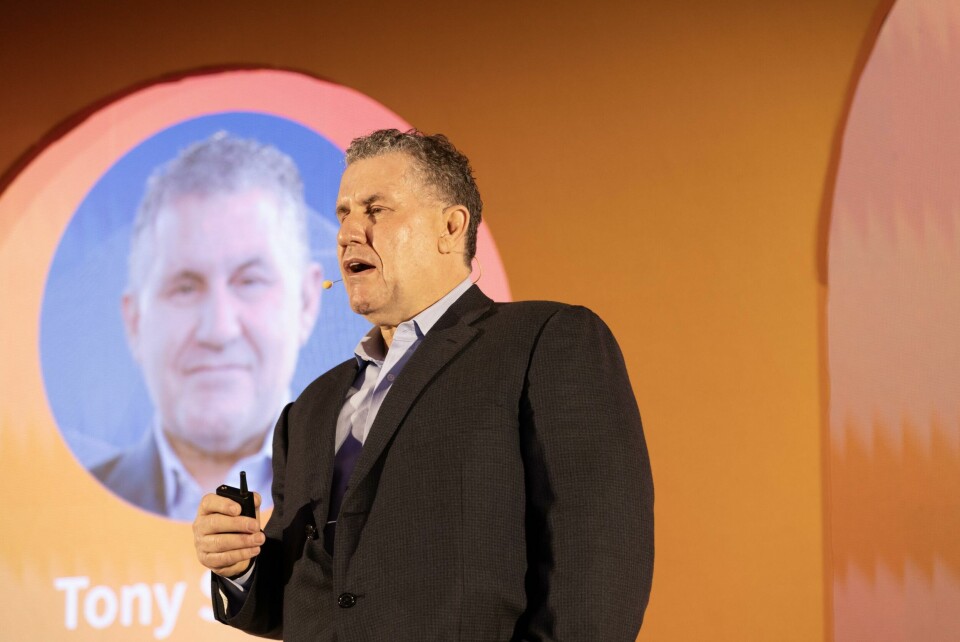
Detailing how electrification is reshaping logistics operations – from loading practices and securement methods to the urgent need for scalable charging infrastructure along transport routes.
GM’s finished vehicle operations manager for ports and logistics EV, Tom Shannon, expanded on this, describing how GM is integrating EV-specific strategies into its overall network optimisation. “We’re looking at our yards and asking: are we set up for the future? Not just capacity, but capability,” he said. This includes rethinking layout design, charger placement and processing flows to ensure throughput isn’t constrained by limited infrastructure. “As volumes increase, we need to be as efficient at delivering an EV as we are with an ICE vehicle. That’s the benchmark.”
Stinsa’s Red Sofa interview laid out the infrastructure reality: without scalable charging access along multimodal routes and at storage hubs, the logistics chain for EVs will fracture.
From quality crisis to quality culture
“If logistics is the last mile to revenue,” said GM’s logistics manager for quality claims, Brian Watanabe, “then damage is the final deduction.” In sessions focused on quality, OEMs made clear that while performance on incidents per thousand vehicles is improving, maintaining quality across an increasingly stretched network requires a shift in culture.
Melissa Tremp of GM and Ryan Kooistra of Rivian shared how their teams are leveraging real-time data and collaborative audit practices to reduce damage rates and improve issue resolution. Both pointed to more structured processes for capturing and acting on logistics quality data. For instance, GM has been using monthly supplier scorecards and integrated telematics data to detect performance trends, while Rivian is working closely with benchmarking groups like the Automotive Logistics Executive Committee to identify common risk factors earlier and align on mitigation strategies.
GM’s Paulsen further reinforced this priority, highlighting how GM is embedding quality focus into daily operations. “It’s not just about measuring damage,” she said. “It’s about building in the tools and visibility to prevent it from happening in the first place.” Paulsen emphasised GM’s use of weekly performance data, tech-enabled audit trails and a more centralised claims adjudication system that shortens the cycle time between issue detection and resolution. “We’re bringing the right people together at the right time with the right information,” she noted, explaining how GM is using digital systems to connect field teams, logistics planners and carriers more closely than ever before.
Paulsen also pointed out in her Red Sofa conversation that GM is embedding startup-style “learning sprints” across its finished vehicle logistics functions. “We’re staying close to our failures so we can improve quicker.”
Data is key for visibility
There was perhaps no more consistent theme across the event than visibility – specifically, visibility that enables action. Ben Shain, senior manager for vehicle logistics at Nissan North America described how VIN-level tracking is allowing his team to manage handoffs across providers, proactively resolve bottlenecks, and validate performance. “We have full visibility from port to plant,” Shain explained. “We can see when a delay is happening, understand why, and act on it without waiting for a manual update.” He also noted that this level of transparency enables a more consistent customer experience, especially in high-volume, time-sensitive distribution environments.
Yet, as Shain noted in his Red Sofa interview, data isn’t useful if it’s not intelligible. He’s pushing for visibility tools that contextualise data and help teams respond, not just observe.
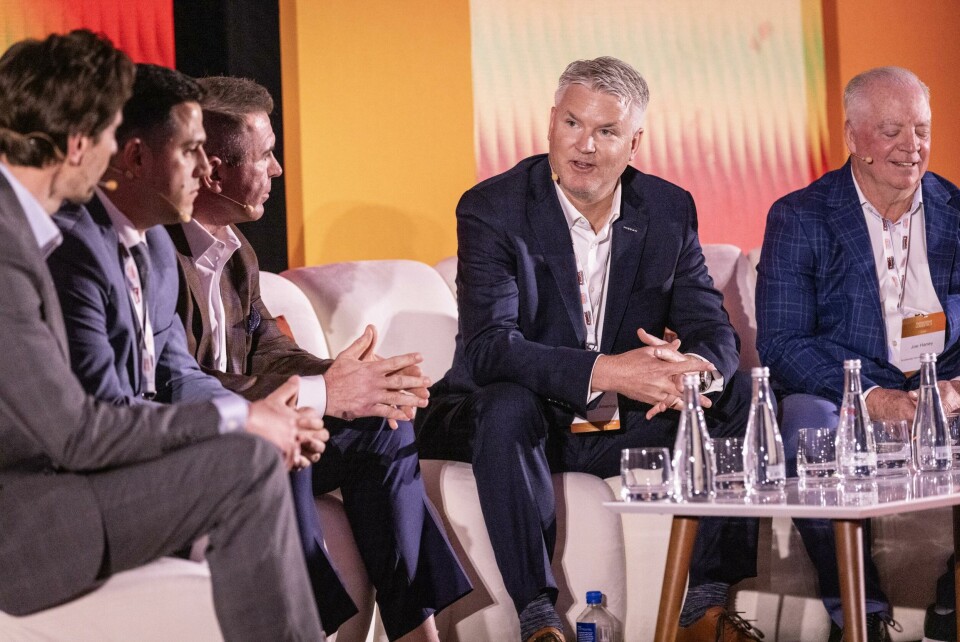
Ben Shain, senior manager for vehicle logistics at Nissan North America, emphasised the importance of actionable visibility, highlighting how VIN-level tracking enables proactive management of logistics bottlenecks and enhances customer experience.
Companies like Cognosos and Blue Yonder echoed this shift onstage – from passive dashboards to predictive command centres. Using AI to analyse dwell times, lane performance and ETA variance, these systems are starting to serve as proactive engines for network decision-making.
A turning point for the sector
The FVL North America 2025 conference underscored a clear shift in mindset among industry leaders: the focus has moved from acknowledging disruption to implementing practical, coordinated responses. Across multiple sessions, speakers outlined how data systems, routing strategies and collaborative models are being re-engineered in real time to meet evolving demands.
The role of finished vehicle logistics is expanding – from a downstream function to an integral part of strategic planning. Throughout the event, it became evident that logistics operations are no longer viewed as a reactive cost centre but as a platform for competitive differentiation, particularly through agility, transparency and infrastructure resilience.