JLR’s strategic shift towards a carbon-free future
JLR is on a transformative journey to drastically reduce its Scope 3 freight carbon emissions. Under the leadership of freight operations director Levent Yuksel, the company is redefining its logistics services to align with its carbon net-zero ambitions, setting a new standard for supply chain sustainability in the automotive industry.
As part of JLR’s Reimagine Strategy to become carbon net zero by 2039, Levent Yuksel is setting himself, his team and their partners ambitious but achievable goals. He says he will always strive to improve the carmaker’s sustainability in freight operations.
“It’s proving difficult, but I’m not giving up,” says Yuksel. He is determined to slash carbon emissions, and it is not just a professional goal, but a deeply personal one.
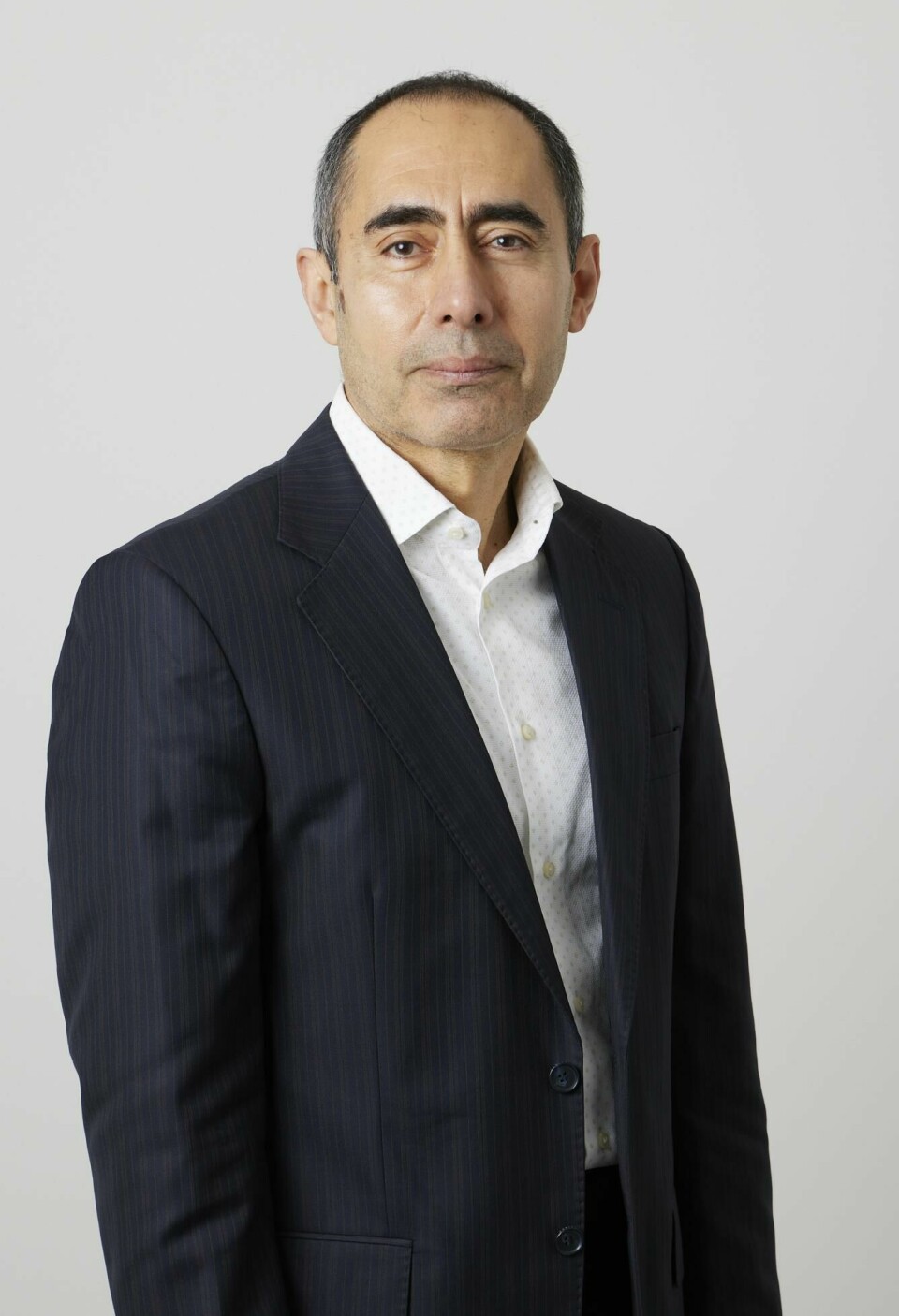
Yuksel joined JLR (formerly Jaguar Land Rover) as plant group manager more than a decade ago before becoming its freight operations lead. In that role he is focused on cutting emissions from freight operations and improve the carmaker’s Scope 3 emissions – the emissions that the carmaker is indirectly responsible for up and down the supply chain.
His ambition, as part of the Reimagine Strategy, is to reduce emissions by up to 30% by 2030 within upstream and downstream transport and distribution, which he says corresponds to between 3-5% of total Scope 3 emissions.
“It’s taking into account inbound and outbound freight, the parts collected and brought to the plants and also the finished vehicles distributed globally,” he says. “Around 95% of that activity is subcontracted and run by third parties, and when this is so vast and with so many parties involved, it is quite challenging to bring everybody onboard with our sustainability goals.”
While the UK government’s objective is to be carbon net neutral by 2050, JLR’s is much more stringent and for Yuksel it is about bringing everybody on the same journey. “It’s not an easy task, but we believe in being on this journey,” he affirms.
Practical targets
While the carmaker’s targets set the bar high, they are realistic, according to Levent. For example, he wants to reduce JLR’s inbound road freight emissions by 84%, rather than 100%, as that would mean having to ensure the energy source of electric vehicles (EVs) would need to be 100% green electricity. “In that sense we take a pragmatic approach of what is the most practical and applicable goal,” he says, “but we want to pave the way and be a role model by showing the best example.”
With its targets set, the carmaker also needs to ensure it is on the right trajectory to meet them. “We are looking at how we want to achieve it, but we are still making it real with clear action plans and alignment with our partners. It is still a work in progress in terms of how we go on that journey, but we think we are making positive inroads.”
“We need to know where, how and what we emit. Then, where do these hotspots occur and how can we look at attacking and improving them”
Levent Yuksel, JLR
Industry partners
To achieve its goals JLR first needs to identify where the ‘emission hotspots’ are – both regionally and within different parts of the automotive supply chain. Yuksel and his team are working with internal departments, and external organisations and partners to identify, understand and measure these hotspots.
Alongside JLR’s circularity department and its own supply chains, Yuksel’s freight operations team is also working with the likes of the Society of Motor Manufacturers & Traders (SMMT), the Association of European Vehicle Logistics (ECG) and the Smart Freight Centre. The carmaker has also applied ECG standardisation recommendations for measuring and reporting emissions. The standards on emissions calculation and reporting in finished vehicle logistics is the product of work done by the ECG’s Sustainability Working Group.
“We need to know where, how and what we emit. Then, where do these hotspots occur and how can we look at attacking and improving them,” Yuksel says. “We are also subcontracting to third or fourth tier providers and we try to understand their operating methodology and carrier base.”
Yuksel is focusing on certain high-emitting routes, as well as regions with stricter regulations around emissions. He explains that JLR wants to spend money on initiatives that encourage decarbonisation rather than paying penalties or taxes.
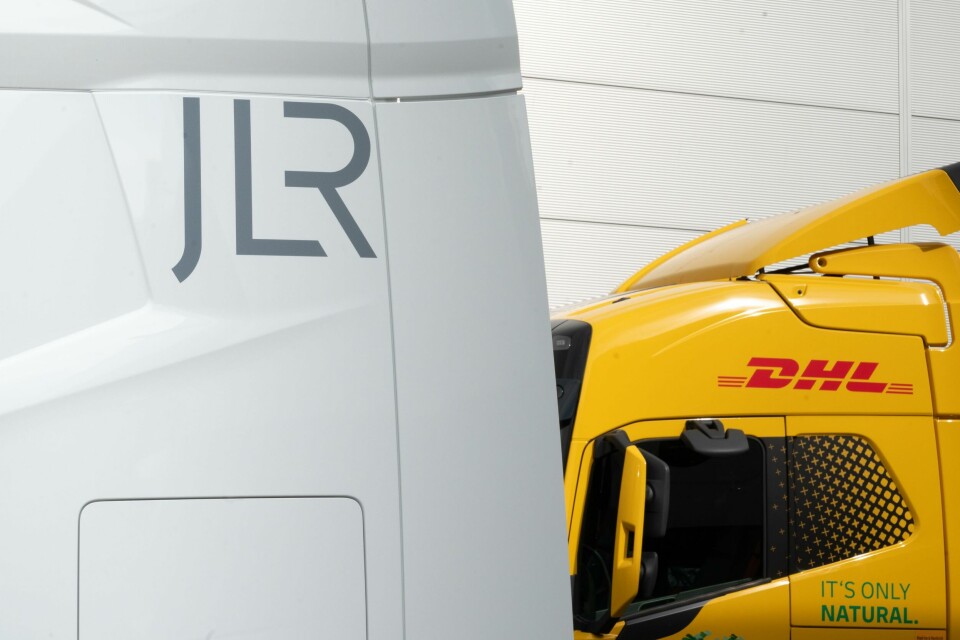
Leading by example
With so many moving parts involved, it’s clear that collaboration will be the key to achieving these goals. Yuksel believes the key to getting others involved is to lead the charge.
“It’s always easy to ask somebody else to do something without showing the effort yourself,” he says. “What we are trying to establish here is that we are not just putting the burden on our partners, but we are showing that we are in this and we are taking on the challenge as well, so it is a joint approach. We want to pave the way by showing the best example and being a role model.”
JLR made the decision to decarbonise its own fleet by the end of April this year, and Yuksel says they are on track to achieve this. The carmaker’s UK road freight vehicle fleet will be replaced with 227 bio-fuel and electric HGVs in partnership with DHL, and is expected to reduce annual CO2e (carbon equivalent) emissions on UK roads by a considerable 8,433 tonnes. The fleet will also use larger 15.6-metre trailers instead of the current 13.6-metre trailers, cutting weekly travel by over 5,600km, reducing annual CO2e emissions by a further 254 tonnes. Once fully operational, this will reduce JLR’s UK-centric road freight emissions by 84%, saving 8,433 tonnes of carbon annually. Yuksel adds that within the DHL scope is a dedicated fleet solely operating for JLR, as well as a fleet DHL subcontracts to other operators in the industry on behalf of JLR.
European network
Yuksel says that JLR is keen to establish itself as a role model in the UK and then expand this to the rest of continental Europe. Almost half of JLR’s supply base is there, so the distances travelled for inbound parts and finished vehicle deliveries are long, and emissions are important culturally and legislatively in the European landscape.
“We would like to expand this [freight decarbonisation] activity to our roots in the European network. We have our plant in Nitra [Slovakia] and for the inbound activities we agreed to operate with an electric truck partner in Slovakia as a starter case, which we also replicate in the UK,” explains Yuksel. “The aim is to expand the circle of influence gradually across the whole network with the alignment of our service providers.”
“We want more intermodal activity, so we need to look at how many of the routes we can move to rail or inland waterways, and move to other alternative solutions”
Levent Yuksel, JLR
Internally, JLR has launched many initiatives and trials, including the Fewer Fuller Greener initiative, which Yuksel describes as achieving more by doing and using less. That is by improving load fills, the effectiveness of loads and making them greener. “This is a holistic approach to our network optimisation activity by utilising the best methodologies for each route,” he explains.
This approach also means assessing the use of cross-docks, decoupling centres or hubs, with the potential effectiveness and emissions of each calculated through digital simulations.
“We want more intermodal activity, so we need to look at how many of the routes we can move to rail or inland waterways, and move to other alternative solutions,” says Yuksel. “It’s always a dynamic environment that enables us to continuously question methodologies.
We are not fundamentally changing everything, but the devil is in the details.”

Pros and cons and costs
Of course, implementing sustainable solutions isn’t cheap, as Yuksel concedes. “We have to prioritise activities because we want to reduce emissions. But it also has to be an efficient operation, so it shouldn’t have an ‘over-and-above-cost’ impact on us, and that’s not always hand in hand,” he says. Sustainable solutions require infrastructure, such as refuelling or charging infrastructures, and some alternative fuels come at a higher cost.
Yuksel says that cost was a factor in weighing up the pros and cons of using either hydrotreated vegetable oil (HVO) or compressed natural gas (CNG) on JLR’s converted core fleet.
“There is this additional cost to pay for the CNG equipment because you need to make modifications to the tractor unit, but HVO doesn’t call for that capital investment as it can be adaptable for a diesel tractor unit. We need to put these elements into the equation,” he explains. “We also need to consider if we have the charging and refuelling facilities because we don’t want our equipment to be stalled somewhere because they can’t refuel or recharge.”
Yuksel, like many in the industry, says the best incentive that could help business cases would be financial enablers from governments.
“We need more enablers to be put in place to help not only us, but all of the industry,” he says. “Again, our key mentality is to spend the money in environmentally friendly solutions rather than spending the money paying taxes or penalties, and make it a better business case.”
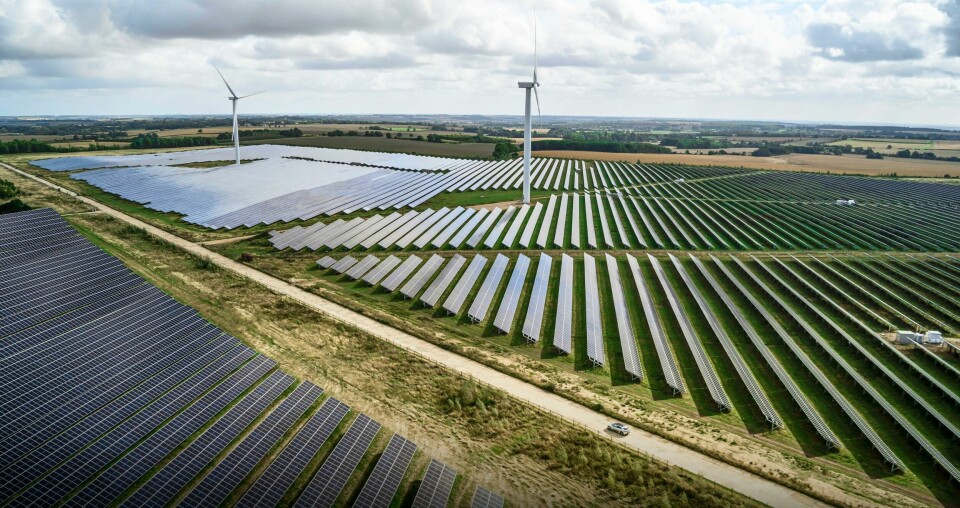
Trial and error for change
Intermodality is something that Yuksel and his team are still working towards, but he has experienced problems with switching modes to reduce emissions. He had considered a trial that would see JLR’s freight operations partner with other customers to use block train rail for bulk goods moving from the European continent into the UK Midlands and northwest region. However, infrastructure, paperwork and customs issues meant the scheme didn’t take off.
Yuksel says it wasn’t a lost cause though: “We learned a lot, we reflected on it and we are still looking for alternative ways of moving into rail more.” In fact, he says trial and error is how change takes place.
“Every attempt is a learning curve and an experience, which we appreciate and value. There is always a learning in every failure and positivity behind every hardship,” he says.
“Sustainability is for all of us, it’s not limited to JLR or a certain state or country. It’s for all of us.”