Bringing battery production in Europe up to speed
As carmakers in Europe scramble to localise pure electric vehicle (EV) production they have one major obstacle to overcome – Europe has no legacy of lithium-ion battery production. China has long dominated the mining, refining and production of battery cells, a situation that European carmakers were happy to go along with until very recently.
Coverage from Automotive Logistics and Supply Chain Europe 2023
-
Audi’s ambitious strategy for a cleaner future
-
Bringing battery production in Europe up to speed
-
Digital clouds on the horizon for finished vehicle logistics
-
Renault and Bosch reap the benefits of digital investments
-
Supply chain needs its own movement in the C-suite
-
Carmakers and tier ones need better supply chain alignment
Battery experts at this year’s Automotive Logistics and Supply Chain Europe conference laid out their plans for localising production, including the import of gigafactory equipment needed to produce those batteries.
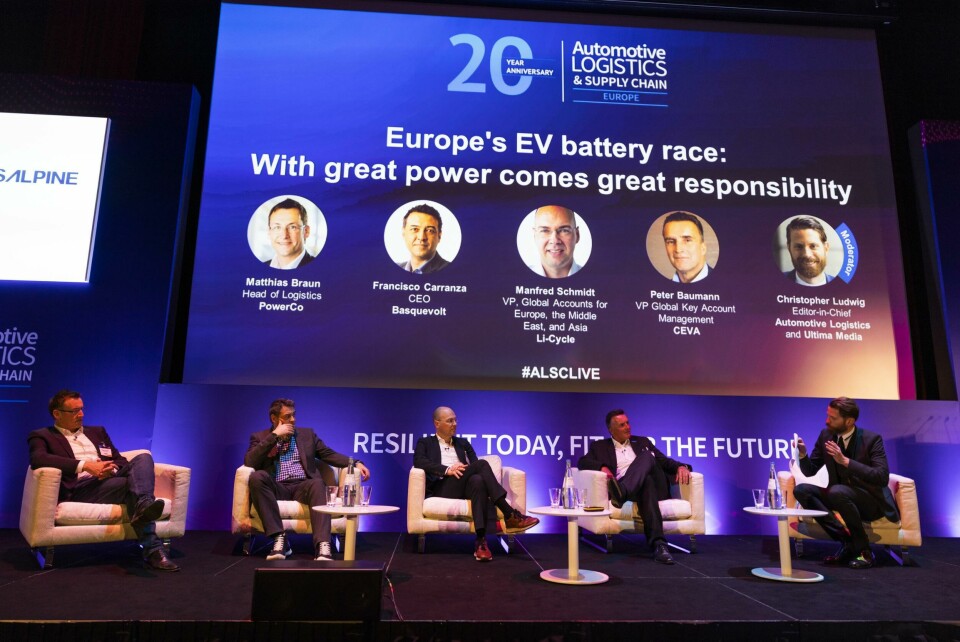
Localising battery supply for EV production in Europe is essential if the carmakers are to survive in a global market that is going electric. Francisco Carranza, CEO of Basquevolt, said there were almost no suppliers of materials, equipment or technology in Europe for a product that was very difficult to make and did not travel safely over long distances. Carranza said the European automotive sector had to find a way to trace the whole ecosystem or plans for battery production in Europe simply would not work.
“We need to start localising suppliers more and more, and getting supply chain and logistics as close as possible to certain hubs,” he said.
That is certainly true for the solidstate batteries Basquevolt is aiming to make in Europe. The supply chain for that does not exist but it needs to be built very quickly. At the same time, battery technology is evolving, which is adding to the supply chain complexity.
“Lithium metal is something that doesn’t travel,” said Carranza. “You cannot produce that 1,000km away from your line. You need to put it close by because it oxidises very fast and needs to travel under argon. There is a huge complexity in how to manage this type of component.”
Preparations at PowerCo
Matthias Braun, head of logistics at PowerCo, VW Group’s own battery company, outlined that 40% of the value in a vehicle was the battery but that 95% of battery suppliers were based in China and wider Asia. PowerCo is already working on its own gigafactory in Salzgitter, Germany, and has recently announced a second gigafactory to be based in Sagunto, near Valencia in Spain. Another is planned for Canada.
Local battery production comes with its own logistics complexity requiring greater supply-chain transparency from beginning to end. That means a need for greater collaboration with suppliers down to the tier-n level, including those involved in the mining and chemical industries.
Braun pointed out that the key success factor in regaining control of the crisis caused by the semiconductor shortage is in gaining control of the whole process. That approach now has to be taken with the establishment of a battery supply chain.
“It is crucial to understand [this new] supply chain,” said Braun. “I don’t know anything about mining logistics, raw materials and refining. I need to understand how the chemical industry and logistics requirements are set up. That is a listen, understand and learn [process].”
For Braun, the localisation of battery and EV production has many challenges but represents a unique chance to redefine logistics in Europe.
“What we now urgently need to do is establish an end-to-end way of thinking. This doesn’t start and end in our production facility, nor even in the normal automotive logistics way,” said Braun. “It is necessary to do something new and better, a once-in-a-lifetime chance for a new way of logistics thinking.”
PowerCo wants its own officially managed network of gigafactories with a supporting and localised network of suppliers, and the support of logistics partners worldwide, according to Braun. “Maximum transparency across the entire logistics supply chain is key, then we have a good chance,” he said.
Help from abroad
In the short term, European manufacturers are dependent on expertise from overseas to get their own battery industry off the ground.
“One of the main difficulties we face now is we don’t have any European companies capable of doing what we need, so we need to go to American or Asian suppliers and persuade them to open operations locally in Europe,” said Carranza.
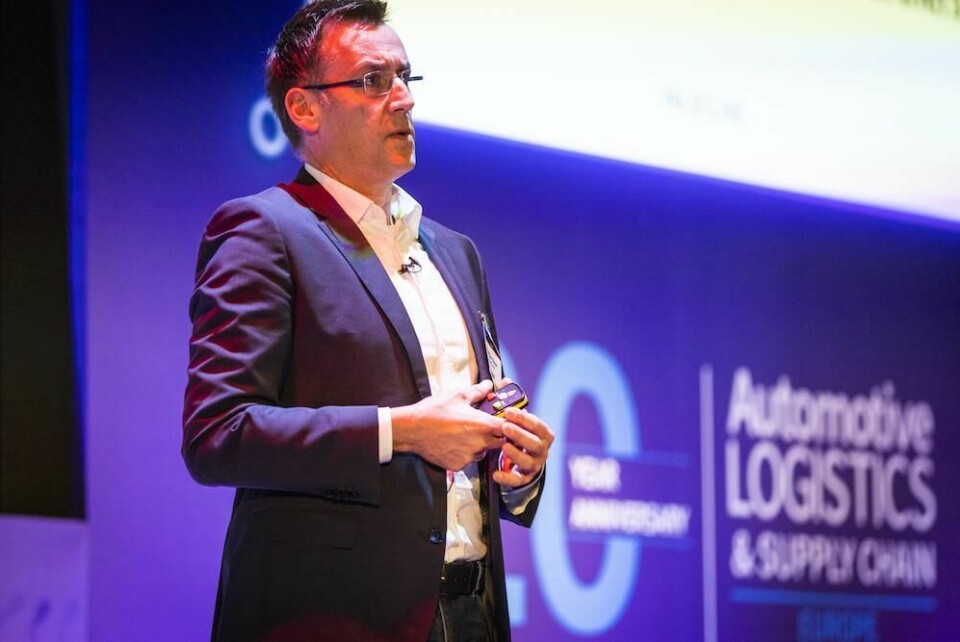
That is not an easy task given the lack of incentive, and given the incentives that each region has to stay put, such as the Inflation Reduction Act in the US, which contains incentives for the adoption of clean energy and the electrification of vehicles, and aims to clean up the supply chain and logistics supporting production.
“People think twice about why they would come to Europe,” Carranza continued. “This is a very difficult market and it is not an attractive place to invest at the moment.”
Braun said the European automotive industry had to change its whole mindset and learn from China how things are done.
“Once that is clear we can make the transition [but] without that it will be too slow,” he said. “We are not the centre of the world [anymore], we are learning.”
Equipment experts
That need to borrow also goes for the equipment and technology needed in the gigafactories to make the batteries.
Bringing that across is something Ceva Logistics has already been involved in, according to Peter Baumann, vice-president of global key account management, at the logistics provider.
“We have already moved a complete gigafactory from one region to another and that was a special project,” said Baumann. “We were something of a frontrunner when it came down to airfreight certification and doing dangerous goods with Iata [the International Air Transport Association].
PowerCo is also bringing equipment over from China and the first containers are arriving in April this year.
“We have a team in China talking to equipment suppliers and we are building a team in Europe to make the transport happen, which is extremely challenging because we will have machines in different containers,” said Braun, adding that it had to be coordinated with the construction of the gigafactory in progress. ”It is a specific logistics topic but it is getting real and it is good to see what is happening,” he said.
Local recycling
Bringing over that expertise to build also goes for the recycling side of the battery circular economy, something as essential to be collocated in Europe’s burgeoning EV sector as the battery production facilities.
Li-Cycle, which specialises in lithium battery recycling and has a facility in Canada, is now looking to localise a recycling facility in Europe and it will be building its own equipment to do so according to Manfred Schmidt, vice-president of global accounts for EMEA.
Li-Cycle is building its own equipment at a converted train building facility in Canada because it could not buy the equipment from anywhere else. Core components are now being flown to the new facility it is building in Magdeburg, Germany but other equipment is being built in Spain and therefore localised in Europe.
“Luckily we don’t rely on supply from Asia on that and are completely independent, which is a benefit,” said Schmidt.