BMW now working with NVIDIA to advance AI in logistics
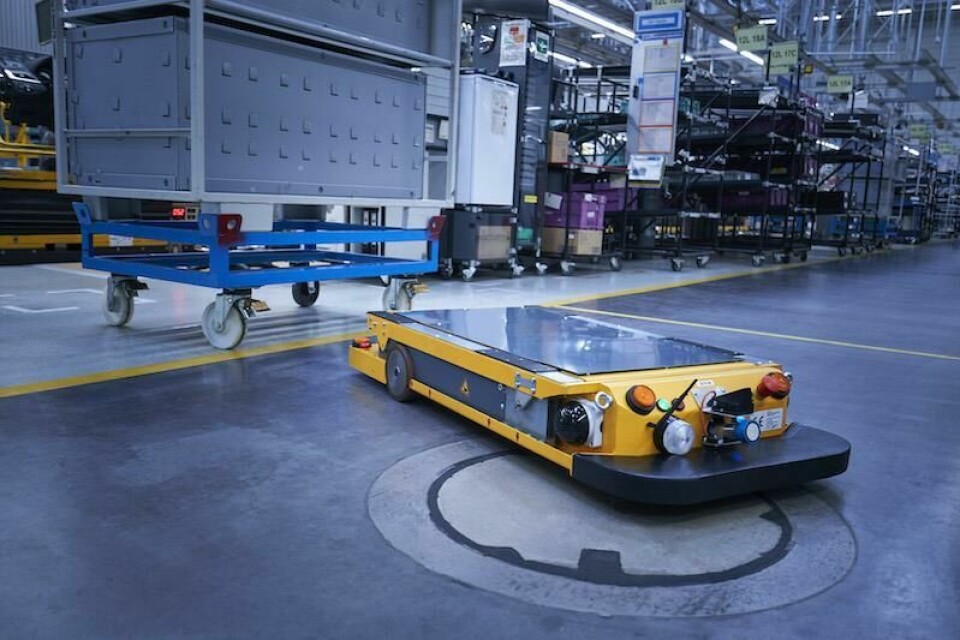
BMW is prioritising intelligent logistics robots in its stated objective of using higher performance computer technology across vehicle making operations.
Building on the advances it has made over the last four years with digital technology in logistics, the German company is now working with US software company NVIDIA.
Last week the two companies announced a pilot project in which BMW has equipped smart transport robots (STRs) with artificial intelligence (AI), developed on NVIDIA’s Isaac robotics software platform, which optimises material flow and planning processes.
According to BMW the robots can now identify obstacles such as forklift trucks, tugger trains and people more quickly and select alternative routes. They can also learn from the environment and apply different responses to people and objects.
The STRs are one of five AI-enabled robot solutions the carmaker is developing with NVIDIA using the Issac software platform to improve logistics processes. These include both navigation robots to transport material autonomously and robots used to select and organise parts. As first outlined in 2018, the other four are handling robots: SplitBot, PlaceBot, PickBot and SortBot (see box).
The robots are being trialled at a number of German plants and at the carmaker’s logistics laboratory in Munich, Germany. AI components are also being tested at NVIDIA’s facility in California.
“The use of high-end AI and visualisation technologies to redesign our logistics is revolutionary,” said Jürgen Maidl, head of logistics, BMW Group Production Network. “Our collaboration with NVIDIA is allowing us to develop state-of-the-art Industry 4.0 technologies. With this high-end technology, we can further optimise our logistics innovations and processes.”
Optimising inbound logistics processes is a priority for BMW. Its plants receive parts from more than 4,500 supplier sites, involving 230,000 unique part numbers.
BMW is also using AI in logistics planning. Using 3D scans the robots can recognise different objects – such as containers, building structures or machines – and use this information to create a virtual layout plan through high-resolution 3D scans of entire buildings and factories. The technology allows the engineers to remove individual objects from the 3D scan using 3D planning software and then change them individually. This makes it easier to simulate and comprehend layout changes within the production halls, said the company.
Last year the carmaker announced it had begun using a digital cloud platform built on software supplied by Microsoft to increase manufacturing and supporting logistics productivity. The Open Manufacturing Platform (OMP) is designed to accelerate the use of internet-of-things (IoT) technology in the supply chain and factory. BMW said it would be shared among OEMs, tier suppliers and logistics providers to bring efficiency across manufacturing and supply up to final assembly.