Rail: the next chip crisis, or new chip solution?
Vehicle rail logistics and semiconductors couldn’t be more different. But carmakers like GM have faced similar challenges in securing capacity and allocation. For purchasing boss Jeff Morrison and his supply chain team, there are also similar solutions.
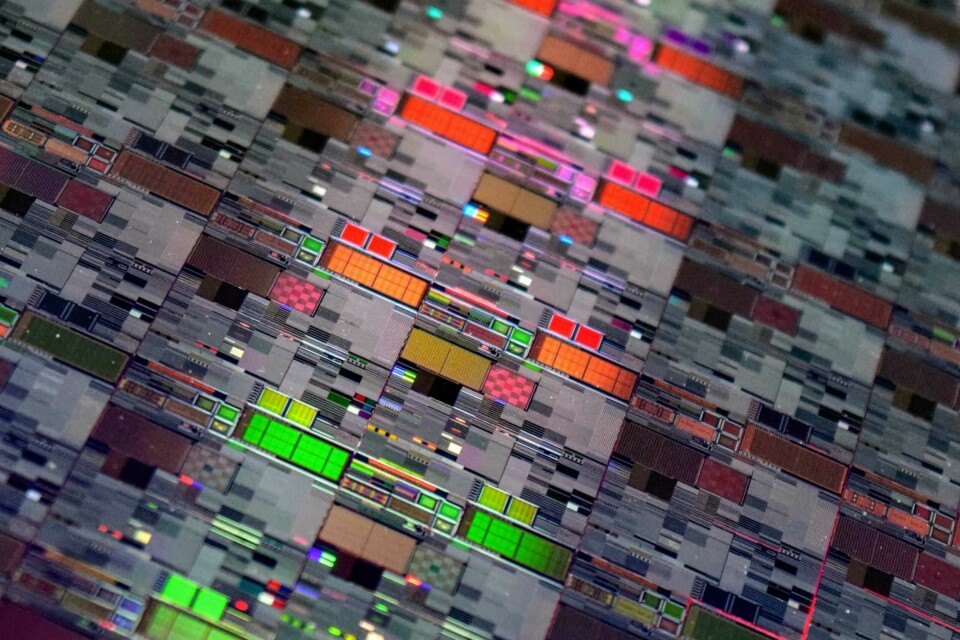
Investing in the long term: Interview series with GM’s Jeff Morrison, VP global purchasing and supply chain
With shortages in finished vehicle logistics capacity, notably for rail services, more automotive OEM leaders have been describing the situation as the ‘new chip crisis’. CEOs and board members of major carmakers are increasingly engaged in understanding and addressing the issue, which is leaving cars stranded and unable to reach customers. In an exclusive interview with Automotive Logistics, General Motors’ global purchasing and supply chain vice-president Jeff Morrison put the issue is in his top five issues globally – and he said that it is the same for GM’s CEO, Mary Barra.
There are several root causes of the challenge. Over the past three years, GM has significantly increased exports from South Korea to North America, led by the success of the Chevrolet Trax and Trailblazer. That rise has coincided with increases from other OEMs out of Asia, while ro-ro capacity has not kept pace with vehicle demand. In response, shipping lines have consolidated Asian shipments to the west coast rather than sailing through the Panama Canal to the east coast, leaving OEMs to work with North American railways on a so-called ‘land bridge’ – moving vehicles across the country via rail. This increase in demand for railcars is putting pressure on railways to return equipment to ports in time for shipments. The network is further complicated by rising production and export volumes across North America.
“We’ve got other OEMs who have also come in taking [railcar] demand and disrupting these flows. And we’ve disrupted the flows ourselves,” Morrison admits.
Labour shortages across railways companies are another factor, with estimates that the industry could have 20% fewer engineers, maintenance and crew members than before the pandemic. Morrison furthermore points to a trend among railway companies to combine rail services for finished vehicles with other railcars moving material and general cargo rather than using dedicated services, part of so-called ‘precision scheduling’. Whilst rail companies have pointed to efficiency gains in such combinations, GM and other OEMs have cited significant decreases in velocity.
A lack of investment in bilevel railcars across the North American network has been compounded by “inequity” in the allocation of those railcars to OEMs, he adds. Across the region, railcar company TTX manages the pool of equipment.
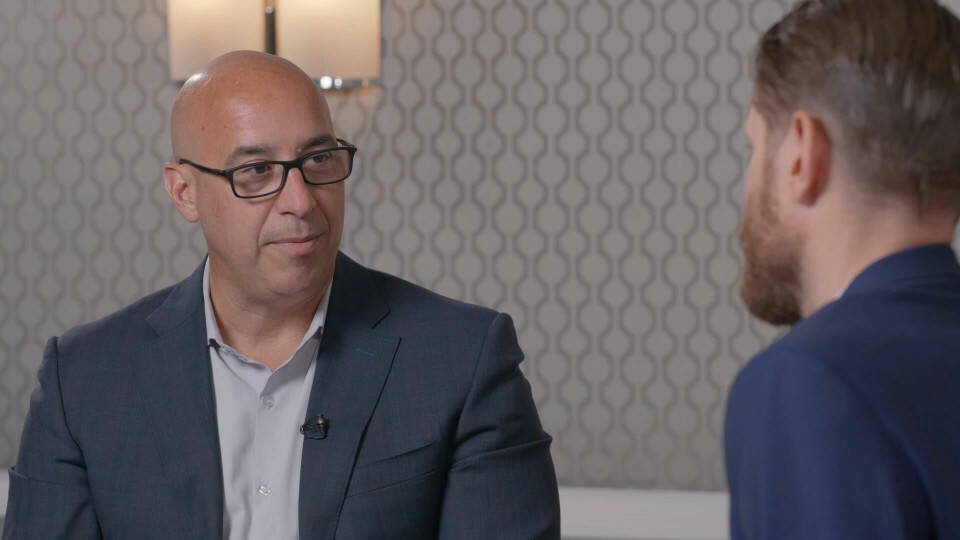
Lessons from semiconductors for rail logistics
The analogy between rail challenges and the crisis in semiconductors might seem strange considering their widely varying technologies. However, capacity for key logistics services such as rail is proving nearly as important as the supply of other critical components, threatening delivery to dealers and customers, and in some cases impacting plant production schedules.
There are other similarities. Suppliers have provided both semiconductors and North American rail to OEMs through allocation models – chips often through electronics and module suppliers, and rail through TTX. Both sectors have limited suppliers upstream, whether in specialised fab wafer and packaging houses for chips, or railcar manufacturers. Both require long lead times to increase supply, and huge capital investments to expand capacity. Finally, while both are critical to the automotive supply chain, the automotive industry’s market share is below 10% for railway providers, a similar level to semiconductors. That’s a big number – but other sectors might easily take priority.
However, the chip shortage has also demonstrated the potential that is possible when OEMs like GM put an urgency on change. Morrison and his team established more direct relationships and supply corridors with chip suppliers, for example. They also tried to solve problems from within, re-engineering electrical architectures and circuit boards to reduce the number and variety of chips required.
Morrison and his logistics team are ready to do the same for critical services, too. Although there is market and technology uncertainty, the company has a transparent plan on its production and product development, and Morrison is confident about what GM needs. He wants to work with suppliers and providers to make sure they have the confidence to make key investments. And where they don’t invest, GM is ready to step in.
“If we compare [vehicle logistics] to everything else that we are doing in my space, we can absolutely take a longer term, more strategic approach in every aspect of our supply chain setup,” he says. “If we need to do things from a haulaway standpoint, railcar standpoint or even ocean vessel standpoint that secures a longer horizon, more stable partnership and flow, then we’re absolutely prepared to do so.”