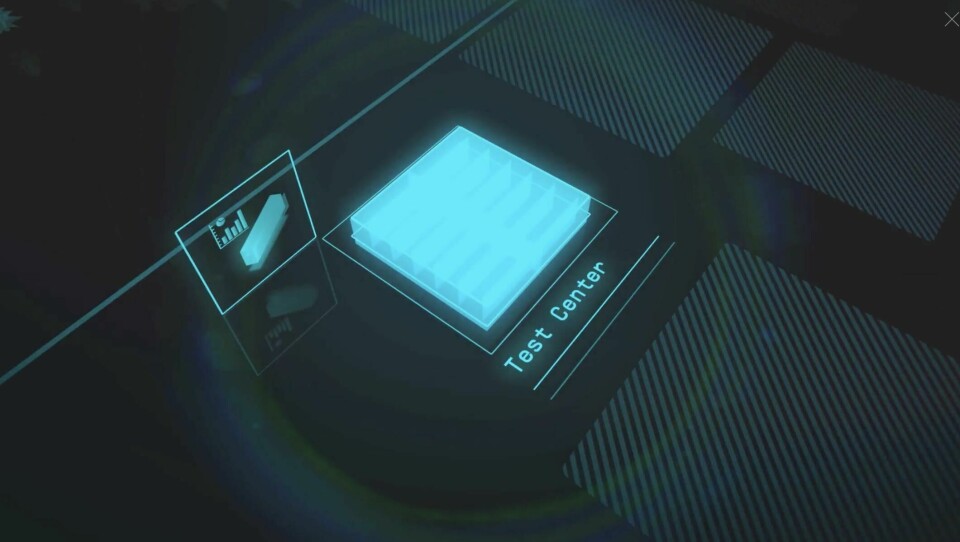
Building a blueprint for battery logistics at PowerCo
As PowerCo sets up battery cell production for VW Group, its logistics organisation, led by Matthias Braun, has set out a vision and framework that will take the best from automotive and chemical sectors, and forge a new benchmark in supply chain transparency and connectivity
PowerCo, the electric vehicle battery subsidiary of the VW Group, was born out of huge supply chain ambitions. Founded as an independent European entity in summer 2022 in Salzgitter, Germany, when the company officially broke ground on its first battery cell plant, PowerCo aims to build a network of battery cell gigafactories in Europe and beyond, bundling all battery activities and competencies across the group. It is Volkswagen Group’s answer to localising batteries and securing the value chain.
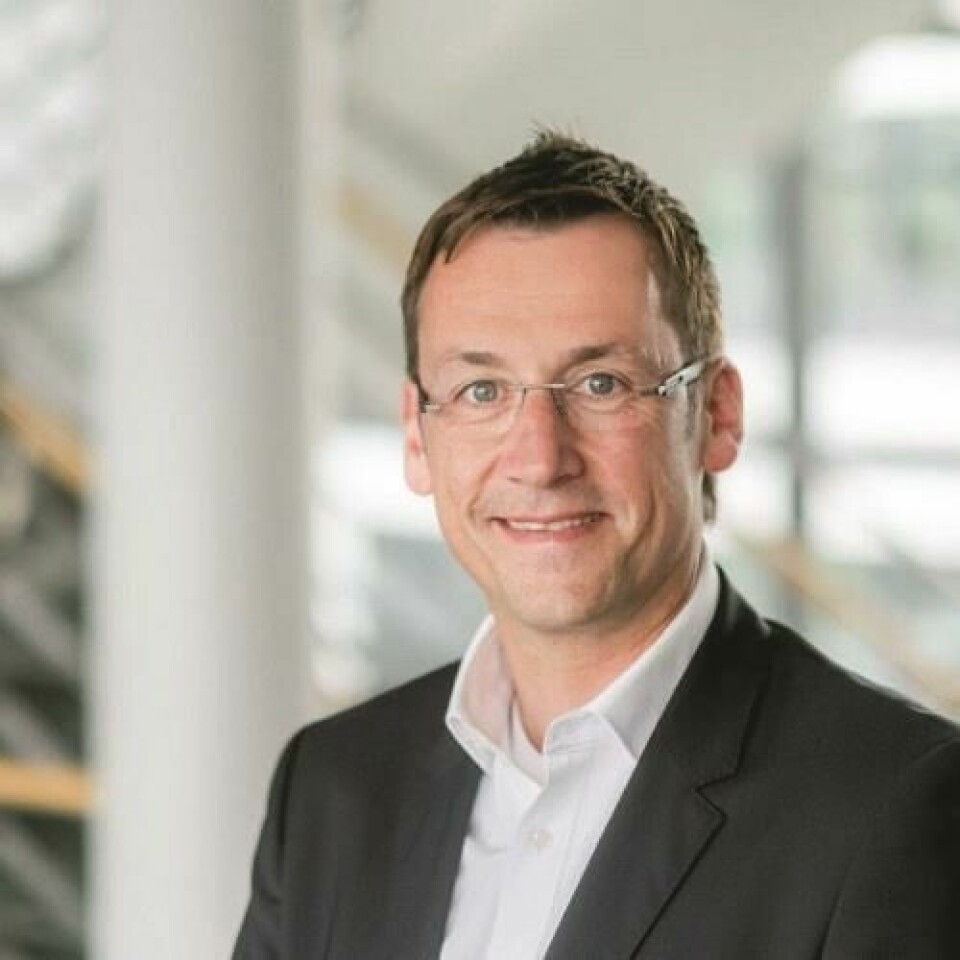
PowerCo has plans to invest €20 billion by 2030, and those plans are quickly becoming reality. An R&D centre for battery cells with a pilot production line has been in operation since 2019 at Salzgitter, with a laboratory for battery cell opening in 2021. Construction of the first gigafactory is now also underway. At ‘SalzGiga’, PowerCo is repurposing existing group powertrain and component production with serial production of battery cells planned to start in 2025. The company has already purchased land for its second gigafactory in Sagunto, near Valencia, Spain, and is in the process of identifying further sites globally.
The Salzgitter plant will serve as a blueprint for battery cell operations for other locations, including for logistics. Supply chain experts have been developing a framework strategy to manage the logistics complexity of battery cell production, including new locations, energy and supply requirements, port and rail access, and transport regulations. PowerCo is factoring in logistics costs, risks, systems and efficiency not only at the beginning of product planning, but in shaping its entire business model.
That makes it one of the most unique logistics projects in the automotive industry, and an opportunity that Matthias Braun, responsible for battery cell logistics at the company, must master. “Our operations in Salzgitter will set a benchmark for everything that we do elsewhere, and so it is a great opportunity and responsibility to ensure that our logistics and supply chain operations help us to have a smooth ramp up and are also future oriented,” he says.
A vision-mission with logistics at the core
Braun’s career has been leading up to this opportunity, including more than 20 years in a range of logistics planning, operations and digitalisation roles across the group for plants and brands, including several with the Volkswagen Group Logistics (Konzernlogistik) entity in Wolfsburg. Appointed to lead battery cell logistics at the beginning of 2022, his growing team then set out to shape a new vision for the logistics at what would become PowerCo, designing an end-to-end material and information flow for SalzGiga from R&D to customers, bill of material, logistics providers and suppliers.
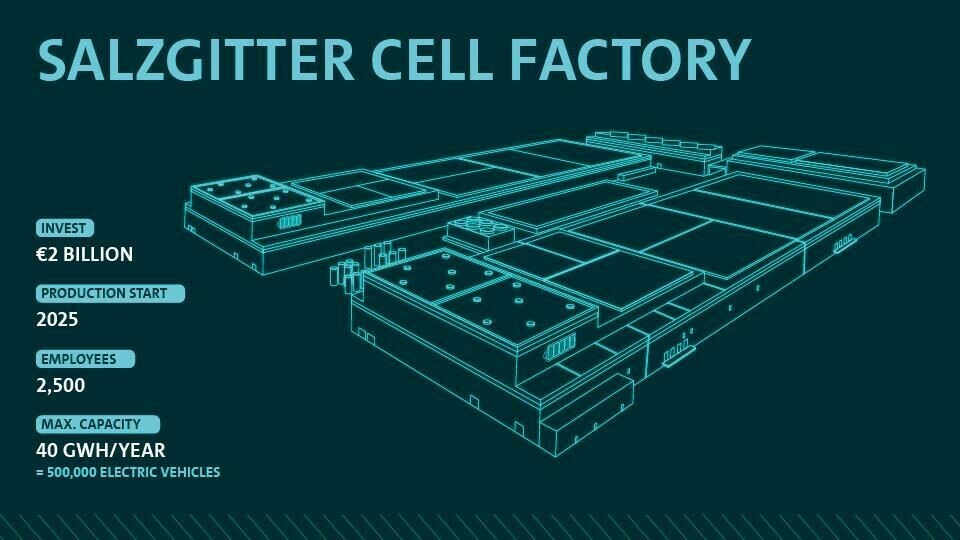
It is a framework that aims to optimise the specific chemical and regulatory processes in battery cell production – whether managing dangerous goods across transport and warehouses, battery cell ageing processes, or sustainable transport. The team set out objectives such as a high use of automated guided vehicles (AGVs) and shelving in plants, managing an automated flow across dry clean rooms, and shipping the majority of finished products via rail.
To achieve these objectives, logistics teams have been involved in designing plant and facility layouts – designs that will also form part of the blueprint for future facilities. For high levels of rail transport, for example, the plant needed not only a direct rail connection, but a separate repackaging area in the inbound goods area for overseas containers that will come directly to the plant.
We have worked with our colleagues in operations and manufacturing to make sure that the setup is optimised for logistics requirements as well as for production – Matthias Braun, PowerCo
“In logistics, we have a high influence on the structure, layout and space in our building,” says Braun. “We have worked with our colleagues in operations and manufacturing to make sure that the setup is optimised for logistics requirements as well as for production. It was important to define these requirements right at the beginning, as it will help us to be efficient in the future, too.”
Upstream visibility also requires new ways of gaining data and collaborating with tier-N suppliers. As the battery supply chain involves materials and minerals from around the world, including a large share currently in Asia, obtaining more detailed, early information could prevent problems in production. As PowerCo nominates new suppliers and localises more in Europe, the logistics team must also help to ensure the company takes a total cost of ownership perspective covering transport, labour and land requirements.
“It’s a new way of thinking to make the whole company aware of the complexities of our logistics network worldwide, and that is supporting our new framework, where PowerCo is making strategic partnerships with our suppliers and their suppliers to make an end-to-end approach possible. The great collaboration with our purchasing team helps us a lot in realising this,” Braun says.
Open data, open sharing
Critical to this approach is Braun’s wider vision to achieve ‘Logistics 5.0’ – a supply chain based on maximising connectivity, open data and integrated planning. That includes updates in schedules at vehicle assembly plants and real-time supplier visibility, with all information aligned to trade, inventory and production data.
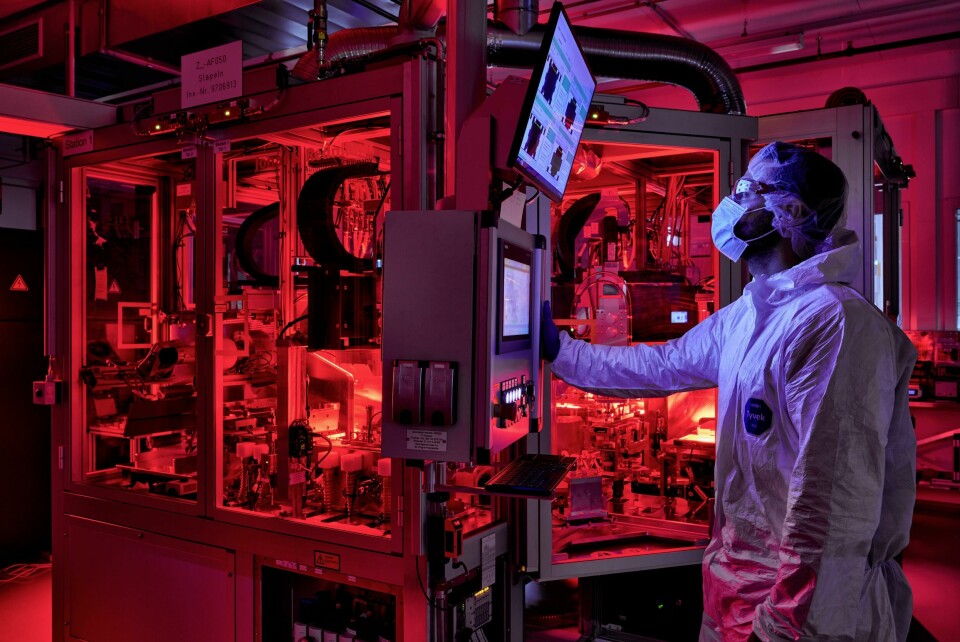
“We want to combine logistics resilience with information from the supply chain, whether from a border, customs process or flood, integrated with information on real time operations so that we can understand the impact,” he says. “So far, I have not seen this integration, so we have put it into our philosophy and way of working.”
The principle of open sharing applies to people and supplier relations, too. As Braun expands the company’s central logistics at a fast rate, he wants a diversity of skills and backgrounds. He is most interested in people ready to learn and to help shape PowerCo’s logistics. Equally, supplier and logistics providers should come to PowerCo ready to share ideas and help the company to evolve processes and technology in battery logistics.
Finally, building lasting relationships and becoming a “customer of choice” will be at the heart of PowerCo’s approach, too. Although it has ambitions to become one of the most important players in battery production, Braun is humble about where the company is starting: unlike vehicle production, it cannot always use its scale and purchasing power across suppliers, including logistics. It must work with suppliers as equals and ensure both sides are learning from each other.
“I don’t want to come with the approach that I’ve learned for more than 20 years in automotive logistics, telling these companies what they need to do,” he says. “I know what I would like to have, but I want to learn to make the best approach, including from how logistics providers work from other customers, for example.
“This is a change in philosophy and approach to really involve these providers as partners to ensure we are growing together and that we make the best combination of the different industries from which we come from, whether the chemical industry or automotive. This is our understanding of a ‘One-Team approach’.” [main text continues below box]
More logistics responsibility
Along with highly connected and integrated logistics, Matthias Braun’s idea of supply chain differentiation includes stronger involvement for logistics in choosing and localising suppliers, as well as working actively to support the upstream supply chain.
For example, Braun expects more shared responsibility between purchasing and logistics departments in managing key suppliers. Logistics will help the company’s purchasing team to be fully aware of the extent of supply chain risks when nominating a supplier, as well as the implications for localisation on both PowerCo and its suppliers. That means supporting not only PowerCo’s purchasing teams, but those of its suppliers, too.
“We need to have close communication with our strategic partners’ purchasing team to understand the total cost of ownership and optimisation options,” he says. “For example, we could look to bring these suppliers closer to production at a supplier park, and better understand the space that is needed, the transport, storage and container costs to make it works for suppliers.”
We need to have close communication with our strategic partners’ purchasing team to understand the total cost of ownership and optimisation options – Matthias Braun, PowerCo
Across the wider battery supply chain, Braun wants PowerCo to learn from the mistakes OEMs made in managing the semiconductor supply chain, when many kept chip suppliers at arm’s length via tier-1 suppliers. He wants to ensure both a deeper understanding of battery suppliers and logistics providers, as well as more humility and partnership in working with them.
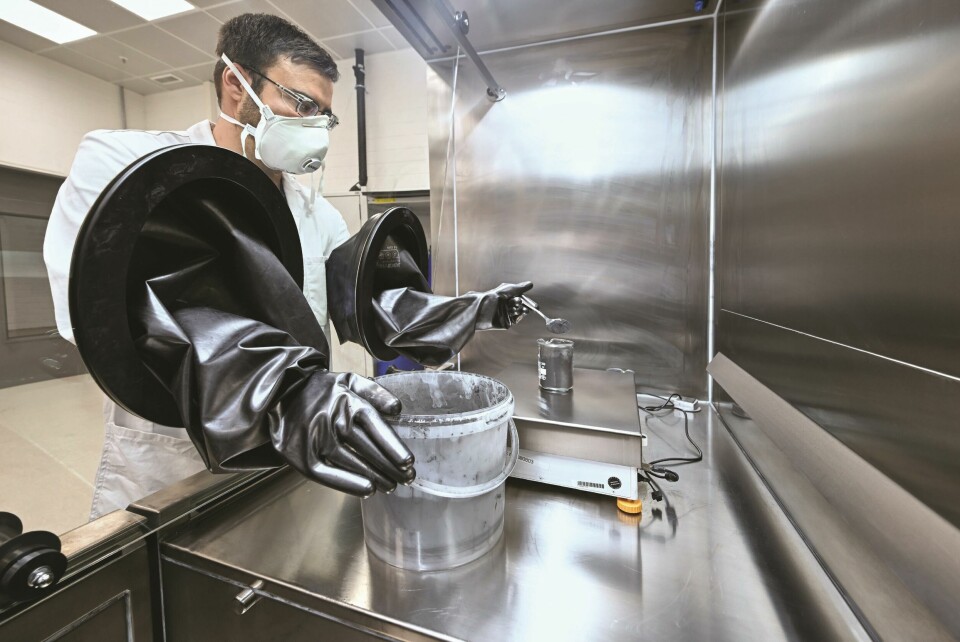
“We have learned a lot from the ongoing challenges in semiconductor supply together with our colleagues in purchasing, including how important it is to understand the end-to-end supply chain and work together to find solutions,” he says. “If we make a supplier nomination, we need to look beyond tier ones to tier-ns, because if you don’t have raw materials, then you are lost.”
Braun believes that the logistics team should be ready to intervene directly in the upstream supply chain where necessary to manage inventory and support expedited deliveries, for example. “Purchasing will be involved and is responsible to those strategic partners, but I would predict that our competencies in logistics will also be required to support daily issues when something is happening and where we might need to accelerate supply.”
Battery logistics 5.0
As someone who has worked across the Volkswagen Group’s myriad of legacy systems and still made real progress in establishing web-based and API-based microsystems, the prospect of establishing a brand-new IT infrastructure is a dream come true for Matthias Braun. He wants systems that allow for an open, seamless flow of information – and he wants people and providers who understand how to manage information in parallel to material.
To that end, information should always flow to the most direct decision maker. His aim is to have a strong central view of the end-to-end supply chain, but with access across operations and plants to ensure agile decision making.
Braun wants to better connect information and changes from suppliers, and their suppliers in turn, whereever possible, while he also wants to integrate information coming from vehicle assembly plants to help PowerCo to continuously adapt its logistics flows.
From a systems point of view, this will not entirely reinvent the wheel. PowerCo will have its own core SAP enterprise resource planning (ERP) systems that brings together business functions. The ERP will connect to a manufacturing execution system (MES) at plants. Other systems, such as transport management, will help to manage logistics scheduling and network design.
Our aim to avoid scrap and waste, and wherever we have it, to use or reuse it in a recycling process, which we are designing – Matthias Braun, PowerCo
Braun envisions multiple layers to this transparency and data connectivity. A central pillar will be to install a control tower in PowerCo plants that shares critical information from suppliers and transport flows, plant logistics, packaging areas and material moving through dry rooms. The control tower will allow teams to quickly adapt delivery and manufacturing schedules, expediting material or supporting specific suppliers where necessary based on a holistic view of the supply chain rather than siloed information.
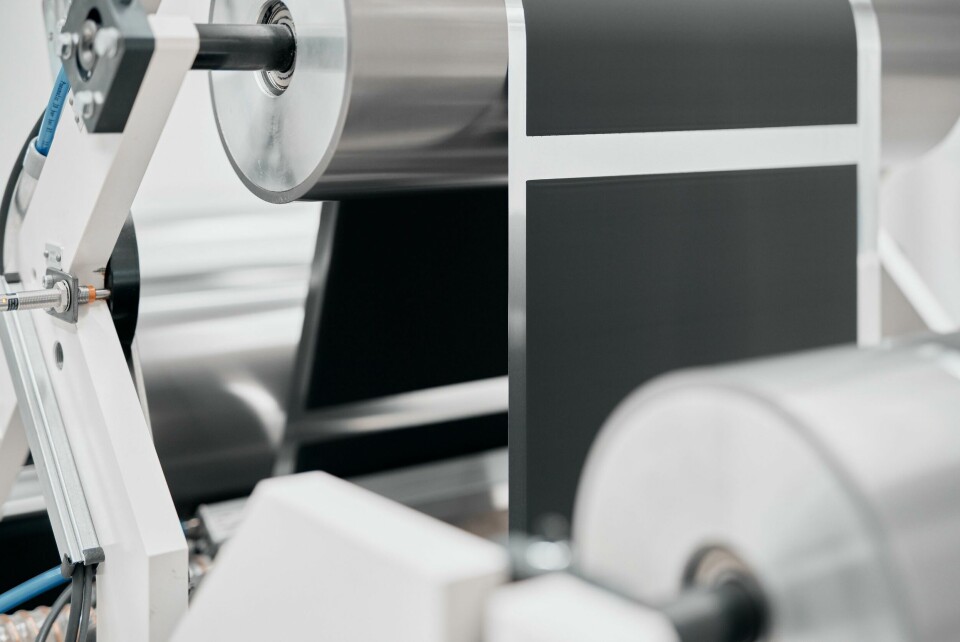
Battery packaging complexity
Although battery and EV supply chains are noted for having fewer moving parts than combustion engines, the requirements in transport, storage and handling are often more complicated. One of the most notable issues is the strong requirements to control the conditions and temperatures for materials in battery production, requiring specific equipment, packaging and warehousing. But this is also an area that is driving innovation.
For example, humidity and cleanliness requirements are far greater in cell production than for ICE powertrains. For that reason, dry rooms must be sealed with airlocks to prevent contamination, which in part leads to disconnected processes in production. Maintaining safe and legal transport requires multiple checks and repackaging at different stages.
Plants will have highly automated logistics and handling to reduce people going into these stages, including AGVs and tugger trains.
These distinct processes also require new approaches to packaging. For example, the way a product is transported from a supplier is different to the way it is stored, different to the way a tugger train brings it through the airlock and again at the point of use on the assembly line. To manage this, PowerCo will use a so-called ‘onion’ concept for packaging. Raw materials for battery cells have different layers of packaging, each specified to each environment across the supply chain, which each layer peeled off at different stages.
This helps PowerCo to manage production materials and keep material dry and clean, but it presents challenges over disposing of waste. “Our aim to avoid scrap and waste, and wherever we have it, to use or reuse it in a recycling process, which we are designing,” Braun says. “This is a big difference compared to an automotive environment, and why it is so important to learn and adapt new solutions.
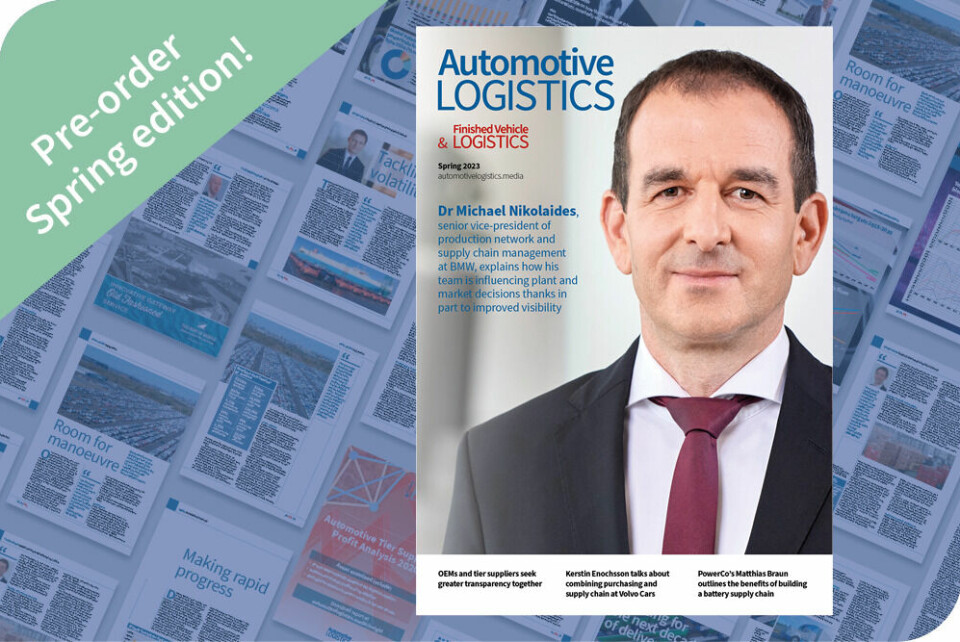
For Braun, this desire to learn and implement new processes and technology – from packaging design to automated transport to supplier visibility – will be at the centre of PowerCo’s logistics strategy and culture. And with the growth and ambitions across the battery supply chain, there will be considerable opportunity to learn and develop new ideas.