The electrifying influence of logistics
Volkswagen’s ramp up of battery and electric vehicle production is transforming its supply chain, and Simon Motter wants to make sure that it takes the right decisions for logistics costs and performance, including an increased use of rail for battery-related transport.
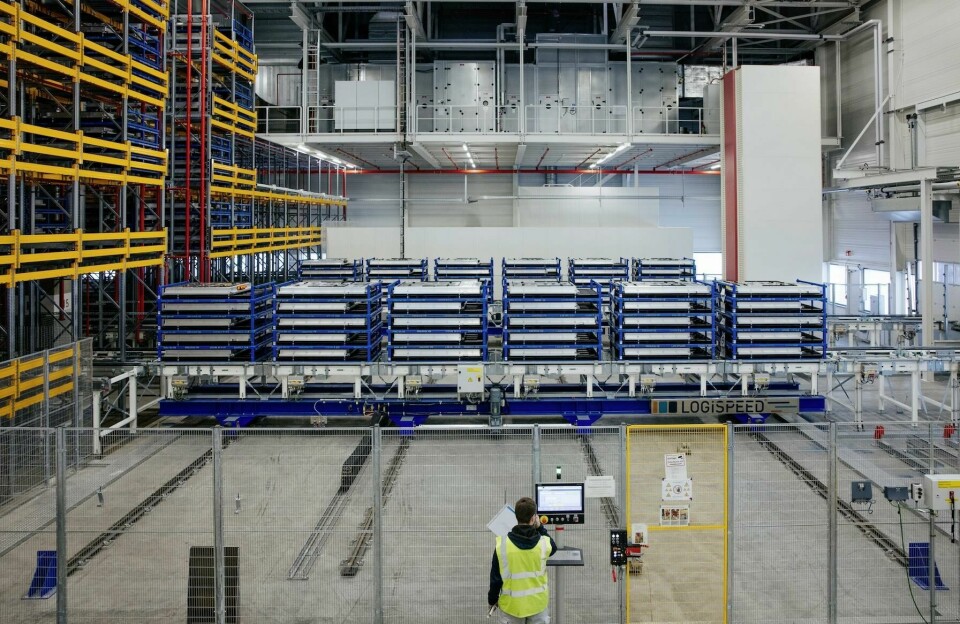
Adding battery cell and modules into production and supply chain is bringing new raw materials, liquids, bulk goods and new requirements across logistics operations
Volkswagen Group Logistics series: Simon Motter on securing the supply chain
-
How Group Logistics is overcoming crises and shaping Volkswagen's future supply chain
-
Ready for any crisis, anywhere in Volkswagen Group’s supply chain
-
The electrifying influence of logistics
-
The many roads, fuels and tech leading to zero emission logistics at Volkswagen Group
-
The quest for one source of truth in Volkswagen Group’s digital supply chain
Volkswagen Group’s electric vehicle offensive has been among the most important supply chain transformation projects since Simon Motter took over as head of Group Logistics in 2021. Electrification is not just a new set of products to manage, he says, but a complete reorganisation of the group’s production and supply network.
“An incredible amount is changing. The battery, which is the heaviest, most valuable component, is not just assembled on the doorstep of the plant in many cases, but requires close control of raw materials of complicated cell production processes with different chemistries and new requirements,” he says. “As logisticians, we’re now dealing with liquids, bulk goods, and whole sets of input that are not yet ‘automotive materials’.”
Volkswagen Group has made significant investments both to convert several factories in Germany to produce only EVs – including Zwickau, Emden and Dresden – and to add the EV-based MEB platform across many factories in Europe, North America and China; recently Porsche started production at its plant in Leipzig on the new PPE platform, which it developed together with Audi.
Group Logistics has been involved from early on in adapting component, supplier and battery flows to match these changes. For example, it developed a battery transport system using special containers to move battery cells by rail from suppliers in Poland to powertrain facilities in Braunschweig, in Lower Saxony, and then to its EV plant in Zwickau, in Saxony, including automated loading and unloading. The service has demonstrated the crucial role that rail plays in battery logistics, says Motter. The battery train links have since expanded to production in Emden, in Lower Saxony on the northwest coast, and to Skoda’s plant in Mlada Boleslav, near Prague, Czech Republic.
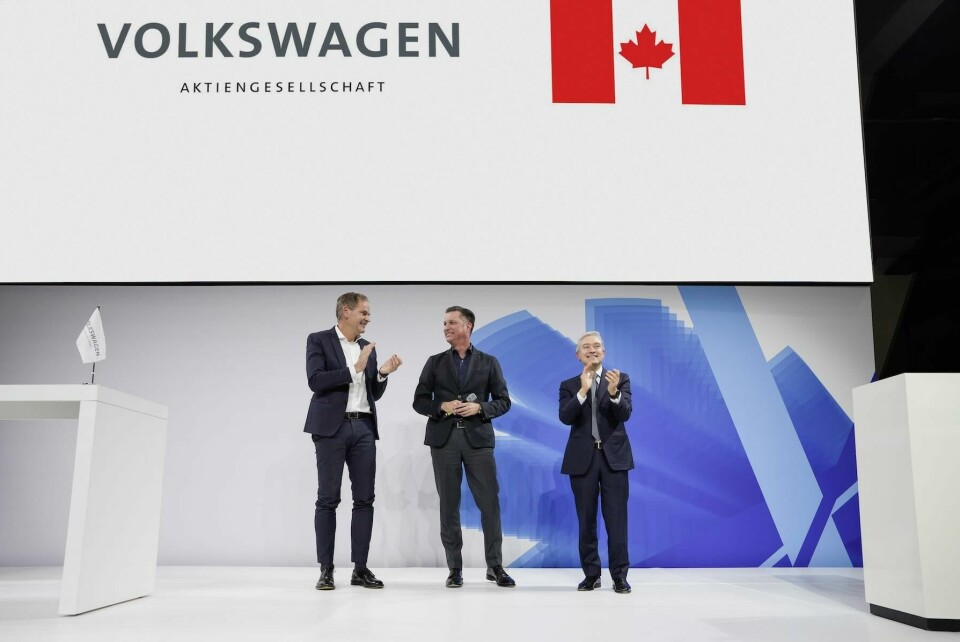
Logistics and supply chain considerations have played key roles in choosing new gigafactory locations for Volkswagen’s PowerCo battery company, including Sagunto, Spain and St. Thomas, Canada
Over the past two years, Volkswagen has gone even deeper into the battery supply chain, investing directly in battery cell production through a wholly owned battery cell company, PowerCo. The company is building a gigafactory in Salzgitter, in Lower Saxony, scheduled to start production in 2025. Group Logistics has supported PowerCo’s growing logistics team in defining processes and governance – and it is also currently helping to coordinate the import of specialist production and automation equipment, most of it from Asia.
Importantly, Group Logistics has also helped to analyse and choose locations for these gigafactories, including the selection of Sagunto, close to Valencia, Spain, for PowerCo’s second gigafactory, which is slated to start production in 2026. It was closely involved in selecting St. Thomas, in Ontario, Canada as the third plant, which will come online in 2027. Both locations were chosen for their access to key materials and minerals, renewable energy and favourable logistics. Proximity to port and rail infrastructure are critical both for inbound battery parts and for serving vehicle plants in an efficient and sustainable way, Motter says.
“The railway will be the main mode of transport for battery modules, battery cells and packs when they need to be transported, and that make rail connections extremely important for such factories,” he says.
Motter maintains that if logistics and supply chain experts don’t get involved early in terms of planning sourcing, locations and supply patterns, then “big mistakes can happen for decades”. On the other hand, setting up the right infrastructure now will have positive benefits long into the future.
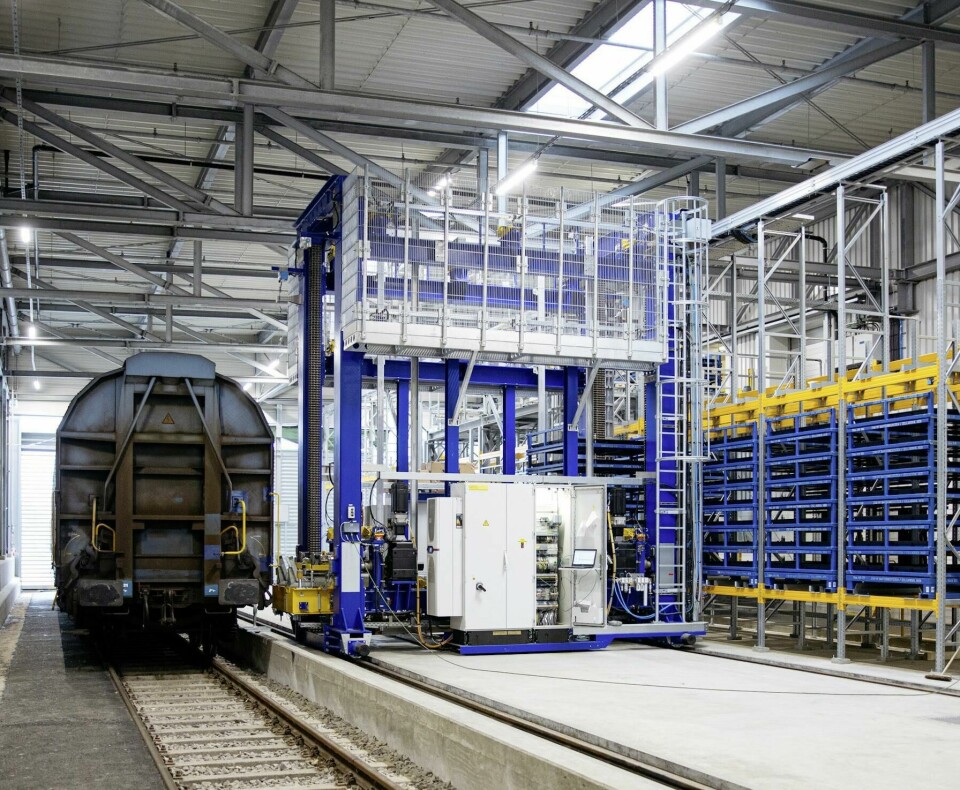
Group Logistics has increased rail transport between battery suppliers, battery assembly and vehicle production locations
Learning many more lessons in battery logistics
The group will face further logistics complexity along with supply and volume uncertainty. Demand rates for EV remain hard to predict, with indications that the initial growth curve may be slowing more than first anticipated, for example. Managing critical supplies and output of batteries will require flexibility and careful capacity management. To avoid future imbalances, logistics teams will need to understand the multiple facets and tiers of battery production to the same specificity that they have learned for semiconductors.
“The railway will be the main mode of transport for battery modules, battery cells and packs when they need to be transported, and that make rail connections extremely important for such factories.”
Simon Motter, Volkswagen Group Logistics
There will be considerably more requirements to learn and adapt for Group Logistics, PowerCo and each of the brands. For example, OEMs need to adapt their delivery and inventory sequence to match the patterns of battery production, aspects of which must run constantly, rather than in a pull sequence. “A battery module is manufactured at an early stage and in batches 365 days per year, which means that even as we produce vehicles on demand, there will be a constant push from behind for batteries that we need to manage,” says Motter.
Group Logistics continues to evolve its battery rail container system, too. The service won a notable award in 2023 from the German Automotive Industry Federation (VDA), but Motter sees considerable room to improve further. One example is to further standardise the container for transporting battery modules, which would improve automation and fill rates. Preparations are underway to prepare PowerCo’s first gigafactory in Salzgitter – which is on the site of an existing engine plant – to receive material and ship battery cells by rail.
“We are focused on establishing new standards and harmonises processes from PowerCo to vehicle plants,” says Motter. “We will continue to redesign our production network on the one hand for electrification, and on our processes and technology on the other.”