Core connections for quality output at JLR
JLR is one carmaker that has been working hard over the last few years to transform manufacturing and supply chain operations up to an Industry 4.0 standard of efficiency and connectivity.
At this year’s inaugural Automotive Logistics and Supply Chain Digital Strategies conference in Germany, Paulina Chmielarz, industrial operations digital and innovation director at JLR, outlined the concerted efforts the carmaker has made in developing a digitally supported strategy for product lifecycle management in its assembly plants, one that ultimately relied on a core IT infrastructure. Chmielarz has also been working to promote greater cross-functional collaboration between supply chain, procurement and manufacturing within JLR, and ensuring teams are fully aligned in the shared use of good quality data, including an end-to-end view of the bill of materials (BOM) from engineering through to logistics and aftermarket.
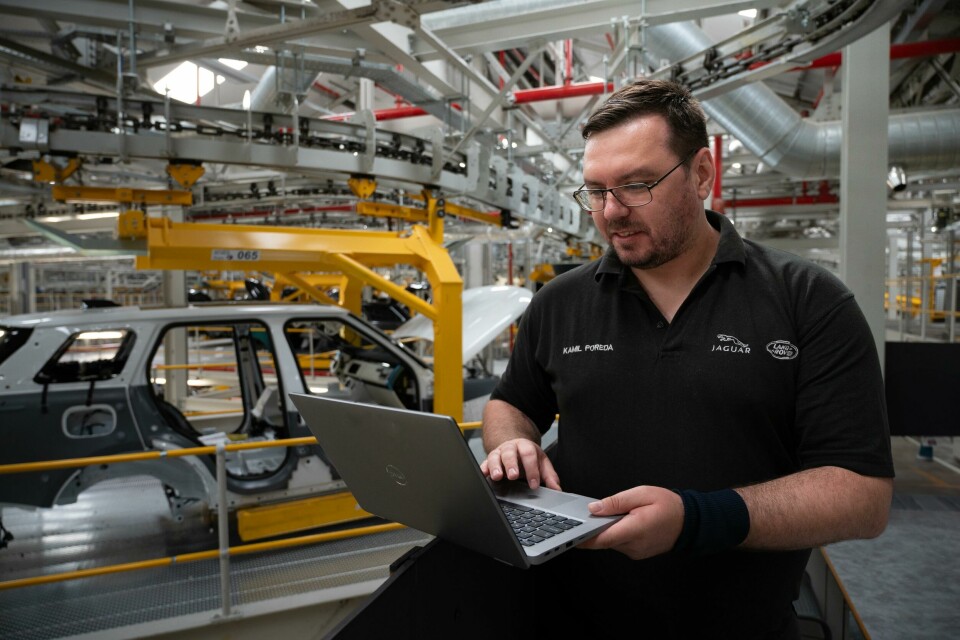
“If you don’t have a master data model that is fully agreed on by cross-functional business teams it is never going to fly,” said Chmielarz.
Digital landscape
JLR’s new digital landscape is built on data from the ground up through five layers of digital architecture, with a foundational IT infrastructure that is modular and connected between business applications by APIs.
“It all starts with a basic infrastructure and basic tools,” said Chmielarz, explaining that a lean core IT system, with minimal customisation, that can deliver transactions and records to business applications and AI, is essential if those business applications are to succeed.
That basic IT infrastructure gathers information on everything in the assembly plant from the conveyors, the programme logic controllers (PLCs), direct current (DC) tools, computers and mobile devices – everything that communicates data is connected to the infrastructure. That relies on 600km of cabling on average in each assembly facility to support Wi-fi connectivity.
The core applications built on this infrastructure includes a large SAP-based enterprise resource planning (ERP) platform and a product lifestyle management (PLM) tool from Dassault Systems for strategic unified bill of materials (BOM) management of the end-to-end journey of each automotive part.
The investment in a modernised digital landscape is part of JLR’s wider Reimagine strategy that includes electrifying its model range, ambitious sustainability targets and developing more resilient supply chain, led by executive director of industrial operations, Barbara Bergmeier. This past summer, Chmielarz was promoted to lead digitalisation and innovation across industrial operations, which includes manufacturing, procurement and supply chain.
JLR, owned by Tata, includes brands including Jaguar, Discovery, Range Rover and Defender.
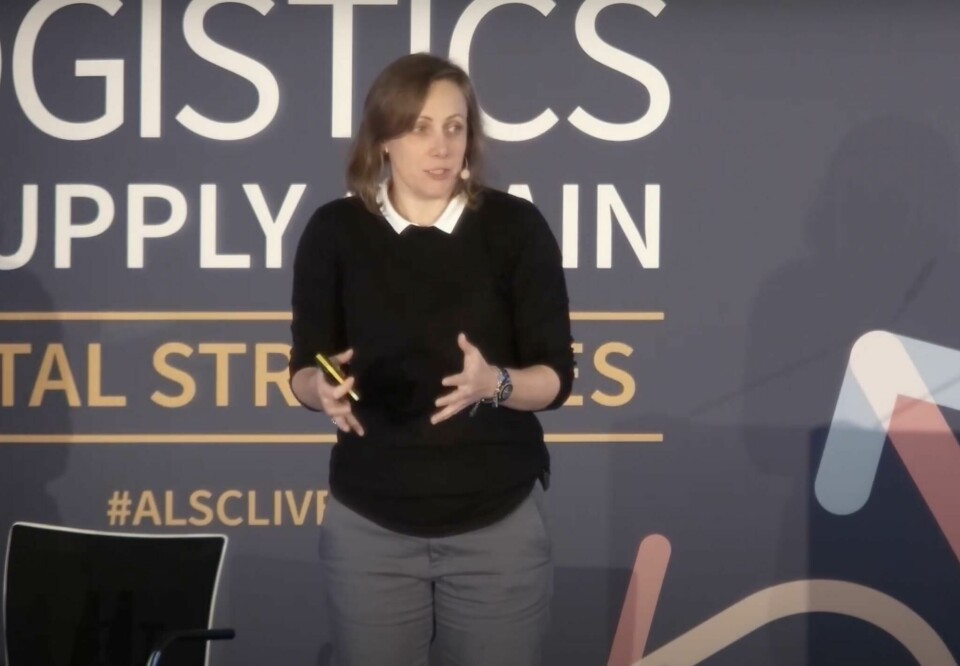
Digital applications
With that core infrastructure in place the carmaker can focus on advanced applications.
“Only then do we talk about data platforms and the digital applications,” said Chmielarz, adding that the data platform is what brings everything together making it an enterprise capability. In terms of digital applications, she said some of them are “very cool and available on the market. And some of them are things that we self-develop.”
The important thing to remember, according to Chmielarz, is that in a market proliferating with advanced digital applications and in-house creativity, it was crucial to balance those digital products with the core systems from which they derived their data.
The development of applications in-house for an assembly plant can have wider repercussions and Chmielarz pointed out that JLR’s owner Tata Group has shown interest.
“There are situations where we as JLR will develop a product for an automotive plant and the whole Tata Group wants it,” she said. “Tata is a gigantic corporation and there are a lot of avenues there. There are some things that we do that are very interesting to the wider world…[.] There is a lot of creativity out there.”
Collaboration with teams
The creativity in designing apps and in developing the data platforms which rest on a strong IT core infrastructure also involves a greater collaboration across teams at JLR. That includes supply chain, engineering, industrial operations, product information and sales – everyone who is concerned with having good, properly scheduled BOM and MRP systems in place.
“It is an enterprise collaboration,” said Chmielarz. “[You need to] work with other departments, not just supply chain. Your enterprise data warehouse is key.”
JLR is transferring all legacy bill of materials data derived from older IT systems, Excel spreadsheets and bespoke applications into the unified BOM on a subscription model that every other system will be able to use, according to Chmielarz. It means that all relevant supply chain personnel are getting into PLM, not exclusively engineering teams.
Chmielarz said that reengineering and modularising master data was important to ensure the product lifecycle is constantly updated and that again depended on talent as much as technology.
“Give your people tools to manage this data,” she said. “Send the initial instance data to SAP, then enrich it, let your people do their other jobs while the actual production release is coming in. Unless you start looking at it you are never going to fix it.”