What Tata’s new UK battery gigafactory means for the supply chain
Tata’s announcement of a new battery plant in Somerset is a significant development for the future of UK automotive manufacturing. Automotive Logistics looks closer at what it means for the supply chain’s bottom lines.
Tata Group confirmed today that it will build a £4 billion ($5.2 billion) battery cell gigafactory in Somerset in the UK, establishing a regional battery supply chain for JLR. Tata formed a new subsidiary known as Agratas for its global battery business, which was also announced on the same day. As the first Agratas plant, the gigafactory will have capacity to produce 40 GWh of battery cells annually for customers of JLR, which is owned by Tata, and Tata Motors across the UK and Europe. Tata said it will begin with a ramp-up phase towards its strategic growth plans for flexible manufacturing capacity and will start production at the plant in 2026.
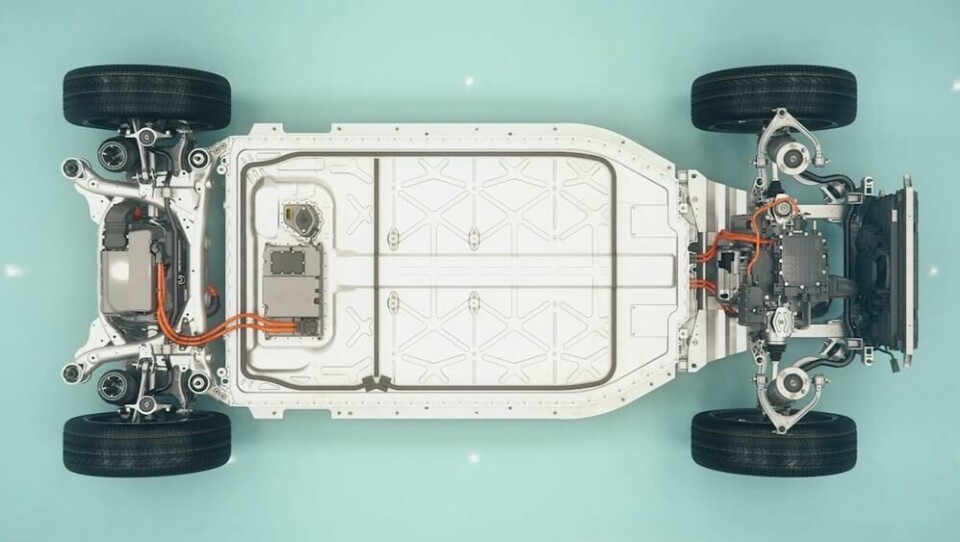
The cell factory was welcomed by many in the industry and is expected to create significant efficiencies in logistics and manufacturing for JLR. But in terms of securing an electrified future for the UK car industry, the UK government’s industrial strategy has been lacking, and risks the UK automotive sector seriously falling behind other regions such as Europe, the US and China.
Brexit and rules of origin
The issue here is that the Trade & Cooperation Agreement (TCA) or ‘Brexit trade deal’ as it is more informally known, stipulates a phase-in of Rules of Origin tariffs. This means that from next year, 45% of the value of an EV built within the UK or EU must be sourced from the UK or EU to qualify for tariff free trade into or out of the EU. And this threshold will increase to 65% in 2027.
However, for an EV, just the battery can be as much as 40% of the value of the vehicle, therefore the battery must be sourced from the EU or incur 10% tariffs, which would make them uncompetitive.
The Society of Motor Manufacturers and Traders (SMMT) in the UK has been asking the UK government to delay the implementation of the Rules of Origin tariffs until 2027. While the SMMT welcomed Tata’s announcement today, it is worth noting that even if the tariffs are pushed back, it would only give the Agratas plant one year of production before the Rules of Origin are implemented.
Major OEMs, such as Ford and Stellantis have stated that they will struggle to meet these rules of origin due to the recent uptick in raw material and energy prices. Both OEMs are therefore also pressing for a renegotiation of the Brexit trade deal so that the current rules are kept in place until 2027, to allow more time for the battery supply chain to develop in the UK and EU.
Subsidies, incentives and support
The wider context here is that to secure the future of highly valuable car industries in their regions, governments around the world are essentially in a subsidy arms race to attract battery plants. For example, huge government subsidies are being offered in the US with the Inflation Reduction Act (IRA), and the EU is looking to respond with subsidies – albeit without infringing EU state aid laws. In that scenario, the UK government has had to respond with grants, subsidies and research funding – which in this case is reported to be up to £500m, although this was not confirmed in today’s announcement.
But why is the UK so exposed?
Whilst many European based OEMs will struggle to meet the rules of origin, UK-based OEMs are particularly exposed. This is partly due to Brexit and the potential trade tariffs, bureaucracy and costs that brings, but there are other factors too. The UK automotive industry is heavily export-orientated with around 80% of vehicles exported, 55% of which were exported to the EU. In contrast, most EU-produced vehicles stay within the single market (with Germany being the only other significant exporter out of the EU). So in that context, the UK is more exposed to the rules of origin and resulting trade tariffs than almost every other EU based OEM.
Supply agreements
On the face of it, this first major new gigafactory is great news for the UK car industry, and that should be celebrated. But there is another dimension to this announcement which is often overlooked. Whilst Tata will build the gigafactory and supply JLR with batteries, will it supply other UK-based OEMs also? And it’s also unclear what experience or technological expertise Tata has in building cutting edge EV batteries. What chemistry or cell format will they use? Most OEMs want to source from the major leading cell manufacturers, such as CATL, LG, Panasonic and Samsung, because they have the best technology, economies of scale and performance and price ratios, which makes the range performance and price of EVs fitted with those batteries more competitive. But what happens when CATL, LG and Panasonic have a 10-20% lead in price, performance or energy density? Will Tata continue to supply JLR in that scenario? Will Tata remain viable in that competitive environment? This lack of technological experience at producing batteries and lack of a major supply agreement with OEMs were some of the main reasons that the BritishVolt gigafactory never got off the ground.
The simple answer is that Tata may need to partner with an established battery cell company, or licence their battery technology, as CATL have done in the US for Ford’s Michigan battery plant.
But this situation also demonstrates that the UK desperately needs not one, but several major gigafactories from a wide range of cell providers. This would allow UK based OEMs to have multiple supply agreements and to shift suppliers as the technology evolves, retaining a competitive edge.
Without that, the future viability of the UK car industry is seriously in doubt.