Six notes on a supply chain crisis: key takeaways from ALSC Global 2022
Summing up what was said at this year’s Detroit event: flexibility rules the waves of logistics, but supply chain managers want better visibility and data to make decisions, while investing in the right skills and labour.
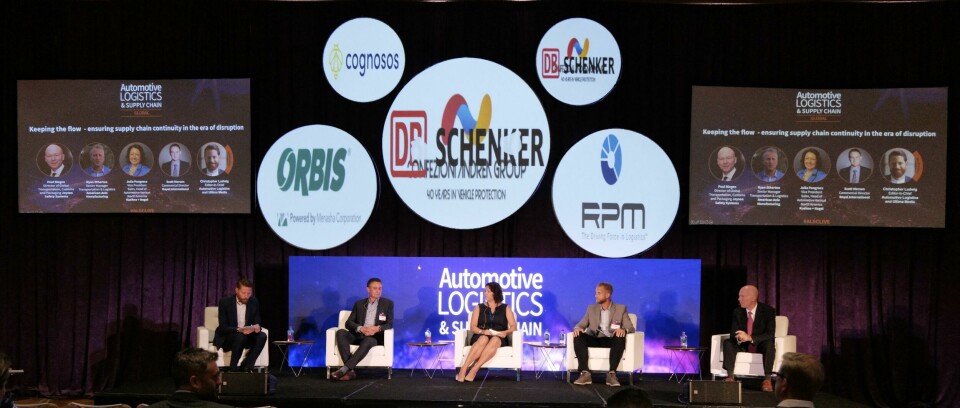
The 2022 Automotive Logistics & Supply Chain Global conference, held September 20-22 in Detroit, was the first full-fledged version of the event since the pandemic, with a smaller event held in October last year. The re-emergence was a record in attendance and speaker numbers as the North American automotive logistics community rushed to come back together to share ideas and common challenges. For many in the industry, it was still one of the first major opportunities to reconnect with partners and colleagues.
However, it was not just the pent-up demand to reconnect face to face that powered the event. As speakers, workshops and side discussions showed, demand for logistics solutions and supply chains insights were in extremely high demand. The value of such services has risen since the pandemic and subsequent shortages in semiconductors, materials, logistics capacity and labour.
That rising value was evident in many of the common themes that emerged across the event, especially in the demand for extreme flexibility and versatility in logistics. OEMs also expressed more willingness to invest in capacity and services than previously to mitigate disruption – but they were also keen to shift from tactical responsiveness to become more predictive in supply chain and logistics planning. Better data integration and sharing play key roles in that, as do investing in transport and freight digital systems. But data and technology must support clear collaboration and decision making in the supply chain, whether internally within manufacturers or across external stakeholders.
Below is a snapshot of key takeaways from the event.
Extreme flexibility in transport management
Disruptions in the supply chain have led automotive manufacturers to work with logistics providers across operations to quickly shift logistics where needed, including changing transport modes, shifting ports or working with new combinations of freight and providers to prevent line stoppages or slowdowns. OEMs have always needed a degree of flexibility – but now they need to be ready to change almost constantly, as confirmed by leaders from General Motors, Stellantis and Toyota. In some cases, this also requires more creative ways of monitoring supply chains, such as digital control towers and improved transport management systems, as implemented by tier one American Axle, or online systems to book and confirm premium freight services, as indicated by tier one supplier Joyson Safety Systems.
More willingness to spend on logistics resiliency
The philosophy of most major manufacturers would still be that the ‘best logistics is no logistics’, in that reducing unnecessary transport is more efficient than even the best designed logistics. But in the face of shortages, there has been more readiness among OEMs and shippers to spend on the logistics services and capacity necessary. In some cases, this has been a necessity because of rates or premium freight requirements. But it has also become more tactical: OEMs including General Motors have even taken to pre-booking extra transport capacity as ‘insurance’ to ensure they had enough, for example for ocean or air freight. The extra costs for this freight have at times helped manufacturers to mitigate disruption and downtime.
Revaluating trade-offs in inventory, capacity and logistics
The extreme flexibility, high logistics costs and disrupted production and delivery have led some OEMs and automotive suppliers to re-evaluate the trade-offs between inventory levels and logistics. Where possible, manufacturers such as GM are holding more inventory and buffer stock, willing to change lean principles. Agricultural equipment manufacturer Agco said it was especially “aggressive” in securing inventory. This is a delicate balancing act as many manufacturers don’t have the margins or working capital to make to take on extra inventory – as confirmed by tier-1 suppliers such as IAC Group, Adient and American Axle, while Stellantis said it was also less actively increasing inventory. However, for some commodities and trade lines, these buffers can ultimately save costs elsewhere.
Tier N supply chain visibility and control
OEMs typically having good visibility of their tier one suppliers including their production, inventory and general logistics. Crises over the years have exposed gaps upstream, with the semiconductor and microchip shortages the most dramatic. There have been stronger efforts among OEMs not only to improve visibility of their tier-1 suppliers’ critical inventory and map out the upstream supply chain, but also to gain more directly involved in tracking those movements or in some cases even taking control. For example, more OEMs are now tracking the progress of the various stages of microchip supply and production – i.e., wafer fab, packaging house, etc – and even intervening or supporting processes where necessary. This extends to other parts of the supply chain where OEMs such as Stellantis and GM are building closer communication and IT links with tier two, tier three and other tier N suppliers. The goal is to better understand critical capacity needs and to better forecast and communicate possible disruption – and take necessary action.
Predictive over reactive logistics management
The broader trend towards investing in supply chain flexibility and resilience has required fast reactions. But as a result, more OEMs and shippers want to shift their freight and supply chain management towards being more proactive and predictive. That is leading to a strong interest and focus on data analytics across trade lanes and deliveries, with manufacturers such as Nissan, Johnson Electric and technology companies focused on improving this visibility. The challenge for many remains that whilst certain tools can provide predictions on key arrivals of given parts of the supply chain (i.e., ships arriving in port), they struggle to gain predictive ‘milestone’ events – i.e., when a specific container or pallet will load onto a truck or arrive at a dock. But the interest in such systems and tools is significant and there is greater willingness to invest.
Logistics talent unchained
The war for talent in logistics extends across the automotive supply chain, with the most critical needs in securing truck drivers, maintenance workers and facility workers across road and rail services. Carmaker such as Stellantis are fielding new initiatives to recruit drivers, while OEMs and tier ones are also evaluating production and delivery patterns to better suit drivers, including moving away from ‘warehouse on wheels’ concepts. As well as frontline logistics workers, the industry is also looking to develop experienced IT, data miners and scientists. One key objective across manufacturers and providers was to develop diverse and dynamic talent, including creating more career pathways for women across logistics. The good news is that, according to Nissan data, supply chain is already offering women more growth opportunities than more shift-based work in manufacturing, however there were still strong lessons in team and staff development across the sector. Companies need to continue to work closely with universities, such as Michigan State and Wayne State, and associations such as AIAG to further extend skills to current and future staff.
A stronger voice for logistics in decision making
The cumulative result of the supply chain crises has been to put it in sharp focus for top senior level management across OEMs. Most carmakers now cite the supply chain in quarterly earnings call, which is leading to more focus from CFOs. OEMs such as General Motors now point to weekly or regular meetings with CEOs and boards as part of updates on critical issues, and has led to much stronger integration of cross-functional teams in logistics, manufacturing, sales and purchasing, with supply chain acting as the conductor. GM has cited such integration as one reason why it has recently been able to regain market share and increase production of key models, including electric vehicles. Some OEMs, such as Toyota, already have logistics strongly integrated into early product and production planning, however for most manufacturers this voice is becoming even more critical not just for immediate decisions about production, sales forecasts and inventory levels, but also wider decisions on plant and supplier localisation; on product launches; on vertical integration; and on making more sustainable and energy-efficient supply chain decisions.
This role will be critical not just in navigating the current and ongoing disruption, but as OEMs such as Nissan pointed out, they will also support electrification and battery supply chain decisions, as well as in the shift to decarbonise production and operations.